Discours d'Edwards Deming au Japon en 1978.
"Un aperçu rapide de quelques nouveaux principes de gestion"
Ce qui suit est une transcription d'un discours oublié prononcé à Tokyo en 1978 par W. Edwards Deming pour l'Union des scientifiques et ingénieurs japonais (JUSE). L’original étant une mauvaise photocopie, de petites portions de texte ne peuvent pas être déchiffrées. Transcription aimablement fournie au Deming Institute (USA) par Mike McLean. Source: www.qualitydigest.com
La traduction de l'article est complétée par des commentaires et des liens vers des documents complémentaires sur notre site Web, mis en évidence en italique dans des blocs séparés. Traduction et commentaires : directeur scientifique du Centre AQT Sergueï P. Grigoriev
Le libre accès aux articles ne diminue en rien la valeur des matériaux qu'ils contiennent.
Le saut spectaculaire dans la qualité de la plupart des produits fabriqués au Japon, de la troisième classe à une qualité et une fiabilité supérieures, avec des économies de production étonnantes, a commencé par une explosion rapide en 1950 et se poursuit encore aujourd'hui. Le monde entier connaît la qualité japonaise et l’essor soudain qui a débuté en 1950, mais peu de gens comprennent comment cela s’est produit.
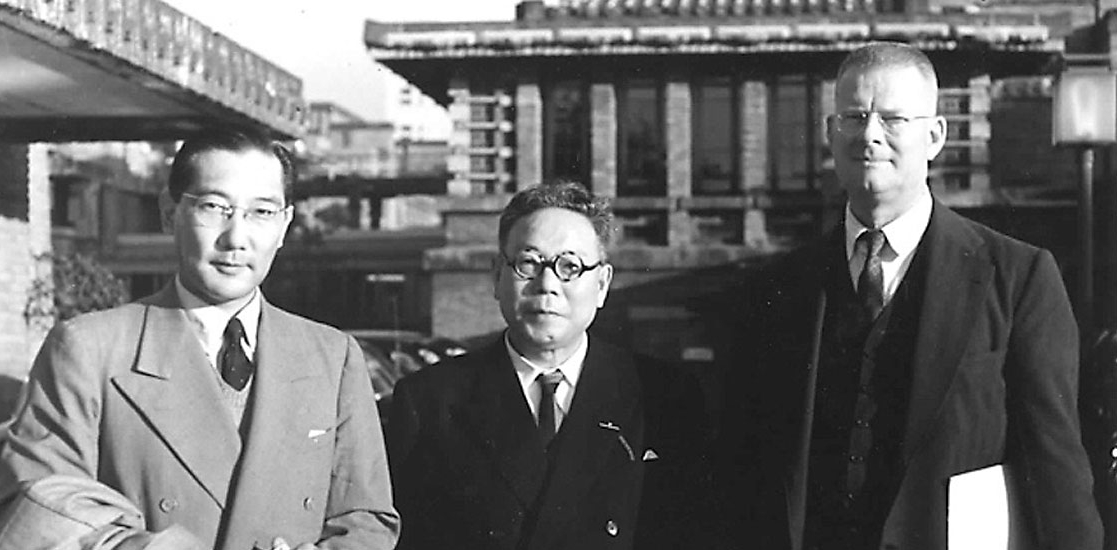
Photo. Dans les années 1950, Eizaburo Nishibori, membre de JUSE, et Shigeichi Moriguchi de l'Université de Tokyo ont invité W. Edwards Deming à donner une conférence sur les méthodes statistiques commerciales lors d'une session organisée par Keidanren, la société exécutive la plus prestigieuse du Japon, sous la direction de son président Ichiro Ishikawa ( également président JUSE). Source: L'Institut Deming .
Il semble utile de rassembler en un seul endroit les principes statistiques de gestion qui ont rendu possible la révolution de la qualité au Japon, car même à l'heure actuelle, la plupart de ces principes ne sont généralement pas compris ou mis en pratique en Amérique.
L’importance relative de certains des principes décrits ici a bien sûr changé au fil des années depuis 1950. Certains des principes énoncés ici sont apparus comme corollaires de principes antérieurs. D’autres conséquences pourraient s’ajouter, presque à l’infini.
Le saut qualitatif au Japon n’est pas accidentel. Ce fut un succès qui faisait suite à un effort concerté, déterminé et méthodique dans toute l’industrie japonaise, à tous les niveaux de production, y compris, bien sûr, la direction, pour faire fonctionner les méthodes statistiques. Des visites répétées, ainsi que des cours à différents niveaux pour cadres, ingénieurs et artisans, organisés par l'Union des scientifiques et ingénieurs japonais, ont guidé et consolidé ces efforts. Peut-être qu’un tel mouvement concerté n’est possible qu’au Japon.
De toute évidence, reconnaître les problèmes de qualité, d’uniformité et d’économie, et évaluer les tentatives visant à les résoudre, nécessite des méthodes et une réflexion statistiques. Les méthodes statistiques couvrent chaque étape de la chaîne de production, depuis la spécification et le test des matériaux entrants, jusqu'aux tests de produits en cours d'utilisation, en passant par la recherche client, la conception et la refonte du produit. C'est pourquoi, comme je l'ai dit Walter A. Shewhart , le contrôle statistique de la qualité est le terme le plus large possible pour désigner les problèmes de production au plus juste.
Principe 1.
Attirer l'attention d'un ouvrier de production sur un produit défectueux qu'il a fabriqué alors qu'il est dans un état de contrôle statistique quant à la cause de ce défaut est démoralisant et coûteux. 1 . Cela ne l'aidera pas du tout, puisqu'il a en fait les yeux bandés et prélève des échantillons de perles blanches et rouges dans une boîte de perles rouges et blanches soigneusement mélangées. Il ne peut pas contrôler l'apparition aléatoire de billes rouges dans ses échantillons, son produit ; il ne peut pas battre le système. Il est gêné par la part des billes rouges dans le système. Seule la direction peut modifier la proportion de perles rouges dans la boîte.
Voir description L'expérience d'E. Deming avec des perles rouges .
En effet, si vous attirez son attention sur un élément défectueux alors que sa performance est sous contrôle statistique quant à la cause de ce défaut, il tentera de modifier sa procédure... [texte perdu], espérant en vain une amélioration. Le résultat de sa modification sera... [texte perdu] une augmentation des variations de ses résultats – un retour de flamme qui annule ses efforts.
Voir l'explication dans l'article de Donald Wheeler que nous avons traduit. Manières correctes et incorrectes d’utiliser les champs de tolérance. Faut-il trier les produits selon des marges de tolérance pour les produits défectueux et non défectueux, ou faut-il essayer de personnaliser le processus ?
L’argument selon lequel un ouvrier de production a le droit de connaître l’état de ses affaires et qu’il ne le saura pas tant qu’il n’aura pas vu les articles défectueux qu’il produit est l’une des idées fausses en matière de gestion les plus répandues aujourd’hui dans les écoles de commerce. L'erreur expliquée ici résulte d'une incapacité à comprendre les meilleurs principes de gestion.
Principe 2.
Si un salarié a atteint un état de contrôle statistique dans son travail, mais que ses performances en termes de qualité ou de quantité ne sont pas satisfaisantes, il vaut mieux le muter vers un tout autre emploi.
Voir l'explication dans la solution ouverte Un regard critique sur l'utilisation des KPI dans le système de motivation du personnel. Ou comment le management se prive des informations les plus importantes pour gérer l'entreprise et détruit le travail d'équipe. .
Principe 3.
La formation et le recyclage d'un travailleur qui n'a pas atteint un état de contrôle statistique de son travail seront toujours efficaces pour lui.
Principe 4.
Les limites supérieure et inférieure de la plage de tolérance d'un produit constituent à elles seules un point de référence coûteux et insatisfaisant pour le travailleur de production. Par exemple, les limites de tolérance du diamètre extérieur comprises entre 1,001 et 1,002 cm indiquent à un ouvrier de production qu'un diamètre de 1,0012 cm se situe dans la plage de tolérance, mais cela ne l'aide pas à produire moins de défauts et à améliorer la productivité, contrairement à ce qu'il pourrait obtenir avec moins d’effort en utilisant des méthodes statistiques. (Déclaré il y a plusieurs années par le Dr Shewhart.)
Voir l'explication dans l'article de Donald Wheeler que nous avons traduit. Manières correctes et incorrectes d’utiliser les champs de tolérance. Faut-il trier les produits selon des marges de tolérance pour les produits défectueux et non défectueux, ou faut-il essayer de personnaliser le processus ?
Principe 5.
Par conséquent, afin d'économiser de l'argent, sa description de poste devrait l'obliger à réaliser un contrôle statistique de son travail avec la répartition des éléments individuels dans la zone de tolérance. Dans le cadre de ce système, ses produits respecteront la plage de tolérance sans le coût élevé d'une inspection détaillée. Les travailleurs soumis à un contrôle statistique mais dont les performances ne sont pas satisfaisantes peuvent être transférés et formés à un autre emploi.
Principe 6.
Une bonne qualité ne signifie pas nécessairement une qualité élevée. Cela signifie principalement uniformité et fiabilité à faible coût et qualité répondant aux exigences du marché.
Principe 7.
Un écart de la caractéristique de qualité par rapport à la valeur nominale entraîne des pertes, même si les écarts se produisent dans la plage de tolérance. Avec une plus grande uniformité, un fabricant peut réaliser des économies dans le processus de production, par exemple en réduisant certaines étapes ou en utilisant des matières premières moins chères, tout en respectant les spécifications. Ainsi, une plus grande homogénéité permet a) au producteur et à son consommateur - tous deux - de réaliser des économies plus importantes ; et b) fournit une meilleure base pour faire des affaires ensemble 2 .
Les exemples abondent, mais ils ne sont peut-être pas aussi connus. Par exemple, l'uniformité des produits agricoles est également importante pour la transformation économique des aliments et autres dérivés.
Voir description Fonctions de perte de qualité Taguchi .
Principe 8.
Dans un état de chaos (mauvaise supervision, mauvaise gestion, manque de contrôle statistique), l'ouvrier de production ne peut pas développer ses capacités potentielles et assurer l'uniformité et la productivité des produits.
Les méthodes statistiques telles que les cartes de contrôle de Shewhart fournissent des signaux indiquant la présence d'une cause spécifique d'hétérogénéité nécessitant une action corrective.
Principe 9.
Il convient de diviser les raisons des coûts de production élevés avec perte de compétitivité des entreprises en deux catégories :
Causes systémiques (causes générales ou environnementales) - 85 %.
Ces échecs restent dans le système jusqu'à ce que la direction les corrige. Leur effet combiné est généralement facile à mesurer. Certaines causes individuelles peuvent être identifiées sur la base du jugement. Le reste peut être déterminé expérimentalement ; certains en examinant les enregistrements des opérations et des matériaux.
Raisons spéciales - 15%.
Ces raisons sont spécifiques à un travailleur ou à une machine particulière. La carte de contrôle Shewhart détecte un signal d'une cause particulière que le travailleur peut généralement identifier et corriger.
Les pourcentages indiqués indiquent seulement que, d’après mon expérience, les causes systémiques éclipsent les causes particulières. La conception des produits et les tests de services font partie du système et relèvent de la responsabilité de la direction.
Les causes communes tirent leur nom du fait qu’elles sont communes à tout un groupe de travailleurs : elles appartiennent au système.
Aucune amélioration du système ni aucune réduction des causes particulières des écarts et des problèmes ne se produiront si la direction ne s'attaque pas aux causes communes.
La confusion entre les deux types de raisons entraîne une frustration à tous les niveaux et conduit à une plus grande variabilité et à des coûts plus élevés – exactement le contraire de ce qui est nécessaire.
Principe 10.
Heureusement, cette confusion peut être éliminée presque sans faute. Des méthodes statistiques simples telles que les distributions, les organigrammes de processus, les cartes de contrôle de Shewhart, toutes expliquées dans des livres, fournissent des signaux qui indiquent à l'opérateur quand prendre des mesures pour améliorer l'uniformité de son travail. Ils lui disent également quand abandonner le processus.
Principe 11.
Ces méthodes statistiques simples minimisent le coût de deux erreurs courantes :
1. Sur-correction (sur-régulation), recherche trop souvent d'une cause spécifique et prise de mesures qui ne font qu'augmenter la variabilité et l'écart par rapport à l'objectif.
2. Inaction (faire trop peu ou ne rien faire) lorsqu'il y a des signes de causes particulières.
Chacune des erreurs est facile à éviter complètement. Vous pouvez éviter l'erreur n°1 (du premier type) en ne faisant rien pour des raisons particulières, faisant ainsi l'erreur n°2 aussi souvent que possible. Le résultat est le chaos. Ou vous pouvez éviter l’erreur n°2 (type 2) en agissant au moindre signe d’écart à la hausse ou à la baisse. Le résultat est une variabilité accrue et un chaos encore plus grand.
Les méthodes statistiques sont le seul moyen rentable d’atteindre la stabilité et de minimiser les pertes dues aux deux erreurs.
Ce qui n'est pas dans les livres, qui n'est pas clair ou qui est généralement inconnu des ingénieurs en contrôle qualité, c'est que les mêmes cartes de contrôle qui envoient des signaux statistiques au travailleur de production fournissent également à la direction une mesure de l'ensemble des problèmes liés au système lui-même (causes courantes). 3 .
Explication du paragraphe précédent de l'article d'Edwards Deming (Sergey P. Grigoryev)
Lorsqu'une carte de contrôle Shewhart montre la présence de causes particulières de variabilité selon Critères zonaux de Western Electric , cela indique un comportement instable (imprévisible) du processus et indique à l'ouvrier de production que les variations observées dans les points « rouges » sont dues à des raisons particulières qui doivent être éliminées et, si elles ne peuvent pas être éliminées immédiatement, prises sous contrôle - dans la plupart des cas, cela peut être fait au niveau du magasin.
Dans le même temps, les limites de contrôle (lignes rouges supérieure et inférieure) d'un processus instable démontrent le potentiel minimum de l'état du processus auquel il parviendra après élimination des causes particulières au niveau de l'atelier. Ces mêmes limites de contrôle et position du processus (Central Line, CL) démontrent une condition due à des raisons générales (systémiques), alors que d'autres améliorations dans la grande majorité des cas dépendent de la manière dont le processus est conçu, et cela relève de la compétence du responsable de l'entreprise. la haute direction. Mais les changements systémiques ne devraient être entrepris qu’une fois que les causes spécifiques de variation ont été éliminées ! Sinon, vous ne pourrez pas évaluer leur efficacité.
Si la carte de contrôle Shewhart démontre un comportement stable (prévisible) du processus, les limites de contrôle et la moyenne du processus démontrent que le processus est dans le meilleur état dont il est capable dans le système existant de causes communes. Et si cet état du processus ne satisfait pas aux exigences, alors seuls des changements systémiques peuvent améliorer la situation, et cela ne dépend que de la haute direction de l'entreprise, mais pas de l'atelier. L'état stable du processus vous permettra de suivre l'efficacité des tentatives faites pour améliorer le système dans lequel ce processus fonctionne.
Exiger que le personnel du magasin améliore de manière indépendante un processus stable signifie créer des conditions démotivantes pour les travailleurs dans lesquelles naissent petits et grands mensonges. Et toute tentative sincère du personnel en activité pour améliorer un tel processus ne mène qu'à augmentant sa variabilité , ce qui ne fait qu’aggraver le processus et provoquer une déception quant à ses propres capacités.
Principe 12.
La première étape pour améliorer tout processus de fabrication ou de mesure consiste à réaliser un contrôle statistique d’une caractéristique clé du produit, puis d’une autre, puis d’une autre. Une fois le contrôle statistique des principales caractéristiques qualitatives du processus réalisé, le processus est prêt pour l'étape suivante : l'amélioration, et cela relève de la responsabilité de la direction.
Tenter d’estimer l’effet des mesures prises pour réduire les causes communes sera risqué et trompeur à moins que les processus n’aient été préalablement soumis à un contrôle statistique.
Les causes systémiques (générales) subsistent même si le contrôle statistique des caractéristiques de qualité les plus importantes d'un produit a été réalisé (comme l'a enseigné le Dr [Joseph M.] Juran il y a longtemps). Encore une fois, les causes systémiques (générales) constituent des défis pour la direction.
Principe 13.
Un ou plusieurs régulateurs mécaniques qui maintiennent simplement les caractéristiques de qualité dans la plage de tolérance n’offrent pas une meilleure uniformité du produit et n’en tirent aucun avantage économique. Cela n'améliore pas le système. Les contrôleurs mécaniques peuvent être utilisés avec succès en conjonction avec des équipements informatiques pour créer des cartes de contrôle qui fourniront des signaux à l'opérateur indiquant quand une cause spécifique d'écart s'est produite et que des ajustements de processus sont nécessaires.
Principe 14.
La direction ne fait pas son travail à moins que l'usine ne maintienne des cartes de contrôle Shewhart pour montrer quelle proportion des problèmes reconnus est attribuable au système et donc à la responsabilité de la direction.
L'affirmation habituelle de la direction, en l'absence de méthodes statistiques, selon laquelle « nous faisons tout ce que nous savons pour améliorer la qualité et réduire les coûts », bien que vraie, n'est qu'un vœu pieux sans comprendre et utiliser les méthodes de gestion statistique.
Une déclaration typique de la direction pourrait être : « Je comprends suffisamment le contrôle qualité pour le gérer efficacement depuis mon bureau de président. » Une compréhension superficielle n'apparaît que lorsque des problèmes surviennent 4 .
La direction américaine suppose généralement que les ouvriers de production sont responsables de tous les problèmes de production et de qualité. En l’absence de méthodes statistiques, le management part du théorème selon lequel si les travailleurs ne commettaient pas d’erreurs, il n’y aurait pas de problèmes. Cet élégant théorème n’améliore pas l’uniformité du produit ni ne réduit les déchets. C’est une attitude coûteuse. Cela cache les responsabilités et les capacités de la direction et garantit que les problèmes continueront.
La raison du rappel des voitures pour correction, familière à tout le monde, se produit chaque fois que quelque chose n'allait manifestement pas, n'est pas liée à la qualité de l'exécution, mais à la qualité de la conception, du système, donc de l'erreur de gestion.
Le moral de l'ouvrier de production serait remonté s'il voyait une réelle tentative de la part de la direction d'améliorer le système et de tenir l'ouvrier de production responsable uniquement de ce dont l'ouvrier de production est responsable et peut contrôler, et non des déficiences qui lui sont assignées par le système, ne peut être surestimé.
Principe 15.
Un processus n’a d’uniformité et de capacités prévisibles que s’il est dans un état de contrôle statistique. Dans cet état, les caractéristiques de qualité de base du produit de demain se situeront de manière fiable dans des limites prévisibles. Le volume de production peut être prédit, ainsi que le coût de production.
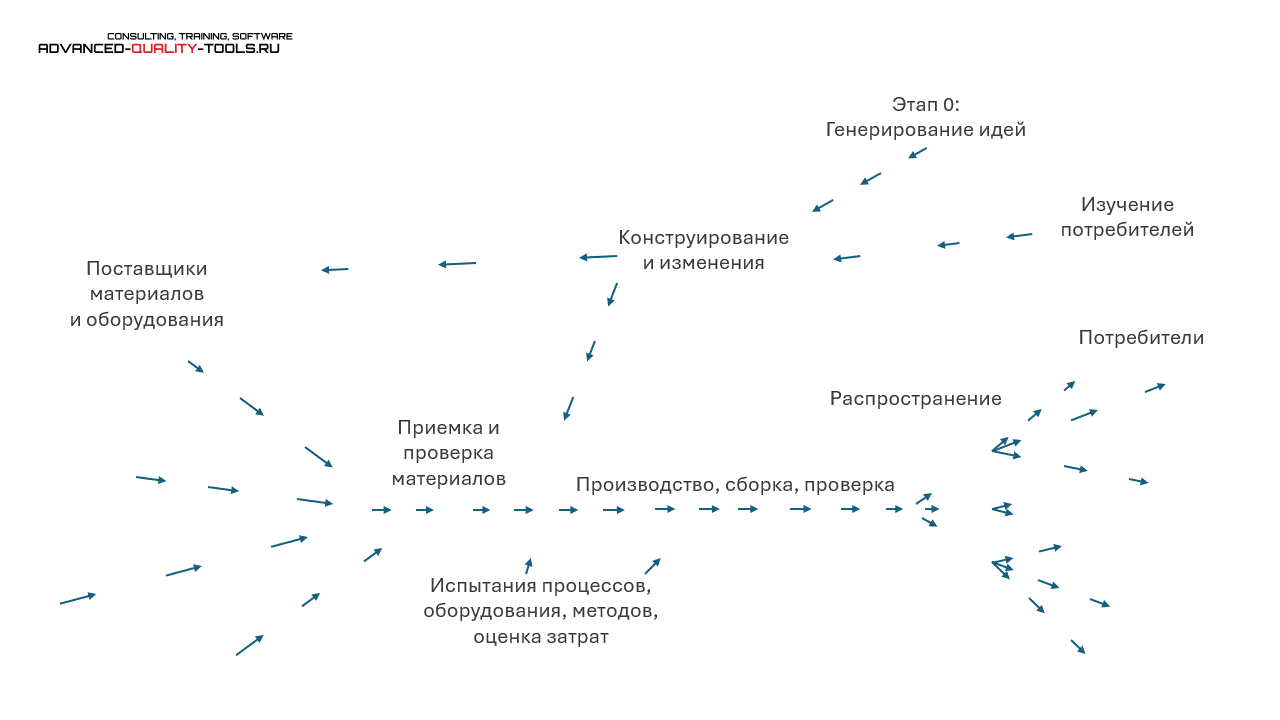
Dessin. Chaîne de production, de la conception, des matières premières au consommateur. Les données issues des recherches des clients et des exigences de service constituent la base de la refonte des produits et des modifications des exigences en matière d'intrants de production.
Principe 16.
Le consommateur est le point le plus important de la chaîne de production. La recherche sur les besoins des consommateurs et les tests de services sont des tâches statistiques.
Principe 17.
La performance d’un produit est le résultat de l’interaction entre trois composants : 1) le produit lui-même ; 2) l'utilisateur et la manière dont il utilise le produit, comment le client l'installe, comment il en prend soin et les conditions d'utilisation (exemple : le client a laissé de la saleté pénétrer dans un roulement à rouleaux) ; 3) instructions d'utilisation, formation des clients, services de réparation, formation des réparateurs et disponibilité des pièces de rechange.
Le fabricant de l'équipement pour lequel les enregistrements de service sont conservés peut examiner en permanence les enregistrements, apprendre comment les défauts sont répartis entre les trois composants et comment améliorer de la manière la plus rentable possible les performances de son produit.
Des offres:
1. Effectuer des répartitions de fréquences pour le diagnostic des défauts par type de client, par personnel de service, par type d'équipement. Un certain changement aléatoire du personnel de service entre les clients et les types d'équipement fournirait la base d'une meilleure formation du personnel de service.
2. Il en est de même à la demande du client, selon le type d'équipement. Les résultats montreront quels types de clients et quelles conditions d’utilisation sont les plus susceptibles d’être satisfaits et lesquels sont les plus susceptibles de provoquer une insatisfaction.
3. Surveiller la dynamique du nombre de défauts par type de défaut et type d'équipement.
Principe 18.
Les critères permettant de tester un produit pour déclarer qu'il répond ou non aux exigences du cahier des charges (tolérances techniques) sont complètement différents des critères d'évaluation des performances d'un produit. 18 .
Principe 19.
La livraison à temps d'un produit démontre une livraison anticipée de quelques jours et une livraison tardive de quelques jours supplémentaires.
Ce principe m'est venu à l'esprit un jour au Japon lorsque je suis monté sur le quai d'un train qui arrivait et que j'ai remarqué qu'il restait 10 secondes avant l'heure d'arrivée prévue. "Bien sûr", ai-je remarqué, "il devrait être en avance la moitié du temps et en retard la moitié du temps si son taux d'arrivée devait être défini comme étant à l'heure."
Voir l'explication de l'opération dans l'article :
1.
Définition opérationnelle
.
Principe 20.
Lors de la production et de la commercialisation d'un produit, la direction est confrontée à deux types de problèmes (défis) : 6 :
A. Que faire avec un produit déjà fabriqué. Est-il adapté pour être envoyé sur un marché ou à un acheteur spécifique ?
B. Comment améliorer le futur produit.
Le problème A se pose toujours pour le fabricant : que faire du produit d'aujourd'hui ? Travailler sur le problème B est un investissement. Chaque degré de réussite dans la tâche B rend la tâche A plus facile à l'avenir.
Il fut un temps où le contrôle qualité consistait en le problème A à la quasi-exclusion du problème B. L'inspection du produit final pour identifier les unités défectueuses était censée garantir que seuls les bons produits étaient envoyés sur le marché ou à un client particulier.
Il est désormais connu qu’aucun test de produit en fin de ligne ne peut garantir la qualité du produit. Certains articles défectueux peuvent passer à travers et susciter de la mauvaise volonté parmi les acheteurs. De plus, en fin de compte, il existe un besoin constant de renoncer aux exigences pour éviter une perte de temps et des coûts de retouche ou de remplacement. Plus nous nous appuyons sur l’inspection, plus grande est la proportion de produits défectueux qui arriveront sur le marché.
L’idée selon laquelle la solution réside dans le contrôle et les tests supplémentaires a parfois cédé la place à l’idée qu’il faut faire quelque chose au sujet du processus pour réduire le taux de défauts produits.
Les procédures d'acceptation statistique devraient être la première sous-tâche prioritaire de la tâche A.
Les méthodes statistiques offrent également une approche rentable du problème B, l’amélioration des processus.
Principe 21.
Le coût de production de plusieurs unités et de leur test ne fournit pas suffisamment d’informations pour prédire les coûts des produits, même lorsqu’il est combiné à une prévision du marché. Il est également nécessaire de savoir comment le client vérifiera la conformité des lots aux exigences. Chaque pièce doit-elle répondre aux spécifications ? (Ce n'est bien sûr pas possible si le test est destructif.) Ou le client utilisera-t-il un plan d'acceptation qui n'exige pas une conformité à 100 % ?
Principe 22.
La mesure, simple ou complexe, est un processus de fabrication 7 . Le produit est caractérisé par des nombres obtenus à l'aide d'un système de mesure. Il n'existe aucun système de mesure identifiable à moins qu'il ne soit soumis à un contrôle statistique, y compris l'échange d'observateurs. Le contrôle statistique n'est pas une question d'opinion, mais une question de respect de certains tests statistiques de hasard.
D'après mon expérience, des instruments et des mesures peu fiables sont à l'origine de nombreux problèmes et litiges dans le secteur de la fabrication. Le produit est-il défectueux ou les mesures sont incorrectes ?
Chaque fabricant est confronté quotidiennement à des défis liés aux différences entre ses propres résultats de mesures et ceux obtenus par son client ; entre ses mesures et réactifs étalons et les mesures et réactifs étalons de son client.
Tout fabricant de produits alimentaires peut se souvenir de l’horrible expérience de voir un produit, déjà distribué ou prêt à être distribué, s’avérer défectueux, au moins temporairement, en raison de résultats de tests faussement positifs qui ont ensuite été attribués à une contamination dans son propre laboratoire.
Principe 23.
La diligence requise dans la fabrication ne peut pas être définie de manière opérationnelle ; par conséquent, toute exigence de diligence raisonnable dans la production ne peut être légalement exécutoire. Cependant, le soin apporté à la production peut être défini et mesuré. La preuve du soin est fournie par des enregistrements de tests sous la forme de données significatives (qui peuvent prendre la forme de graphiques et de calculs statistiques), complétés par des enregistrements d'actions correctives et de résultats. Les instructions d'utilisation du produit et les avertissements en cas de mauvaise utilisation font partie d'un protocole qui indique une certaine prudence de la part du fabricant.
Voir l'explication de l'opération dans l'article :
1.
Définition opérationnelle
.
Principe 24.
La pratique consistant à décerner une soi-disant récompense au mérite à un employé de production ou à un groupe d'employés pour la meilleure performance (ventes les plus élevées, moins de défauts, production la plus élevée) au cours d'une période comptable peut très bien être démoralisante à moins que la récompense ne soit basée sur une mesure statistique satisfaisante. cela distinguera une bonne performance d’une simple chance. Si la récompense n’est pas basée sur une mesure statistique de la performance, alors le système de récompense n’est qu’une loterie. Pour autant que je sache, il n'y a rien de mal à la loterie si elle s'appelle loterie, mais la loterie peut faire beaucoup de mal si elle s'appelle mérite. Le résultat sera une baisse de productivité, une mauvaise qualité et une insatisfaction au travail. Confondre chance et mérite coûte cher.
Voir l'explication dans les articles sur notre site internet :
1.
Ne confondez pas chance et succès
;
2.
Les primes ou les dépréciations pour les employés de l'entreprise sur la base des résultats de la période de référence dans le système sont les mêmes que les récompenses pour avoir gagné à la loterie ou les punitions pour avoir perdu.
.
Principe 25.
Les méthodes statistiques ne sont pas mises en œuvre dans les entreprises ou les organismes gouvernementaux. Les méthodes statistiques proviennent de la connaissance et de l'expérience. La connaissance de la théorie statistique est fondamentale. Il n’existe aucune recette de livre de cuisine garantie que vous devez suivre.
Liens
1. Les principes 1 à 17 ont été décrits plus en détail dans mon article « Sur certaines aides statistiques à la production économique », Interfaces, Vol. 5, n° 4, août 1975 : p. 1 à 15 ; également dans « Mon point de vue sur le contrôle qualité au Japon », Reports of Statistical Applications Research, vol. 22, n° 2, juin 1975 : p. 73-80.
2. Smith, Richard D. « Sauver les superaliments », The Sciences, Vol. 16, 1976 : p. 13-18.
3. Pour des exemples, voir W. Edwards Deming, « On Some Statistical Aids to Economic Production », Interfaces, vol. 5, août 1975 : pp.
4. Golomsky, Guillaume. « Taille du département », Quality Progress, août 1976, p. 13.
5. Ce principe a été constamment souligné par Harold F. Dodge, bien entendu, dès 1944.
6. Ce principe a été formulé par George Edwards de Bell Telephone Laboratories en 1942. contributions à l'échantillonnage d'acceptation et au cours de son long mandat en tant que président du comité E-11 de l'American Society for Testing and Materials.
7. Shewhart, Walter A. « Méthode statistique du point de vue du contrôle qualité » , The Graduate School, Département de l'Agriculture, Washington, 1939 ; pp. 110-119. (Shewhart, Walter A. "Méthode statistique du point de vue du contrôle de la qualité", USDA Graduate School, Washington, 1939 ; pp. 110-119).
Ku, Harry H. « Mesure et étalonnage de précision » , Bureau national des normes, Washington, vol. 1, publication 300, 1969. (Koo, Harry H. « Precision Measurement and Calibration », National Bureau of Standards, Washington, Vol. 1, publication 300, 1969).
Cameron, Joseph M. « Assurance des mesures » , Bureau national des normes, Washington, Bulletin no. NBSIR 77.1240, 1977. (Cameron, Joseph M. «Measurement Assurance», National Bureau of Standards, Washington, Bulletin n° NBSIR 77.1240, 1977).