Manières correctes et incorrectes d’utiliser les champs de tolérance. Faut-il trier les produits selon des marges de tolérance pour les produits défectueux et non défectueux, ou faut-il essayer de personnaliser le processus ?
Article : [26] DONALD J. WHEELER : « Bonnes et mauvaises façons d'utiliser les spécifications. Trier ou ajuster ?
Traduction, notes et matériel graphique supplémentaire avec explications : Directeur scientifique du Centre AQT
Sergueï P. Grigoriev
, en utilisant le matériel gracieusement fourni par Donald Wheeler.
Le libre accès aux articles ne diminue en rien la valeur des matériaux qu'ils contiennent.
Dans cet article, nous examinerons l'historique et l'objectif des champs de tolérance, ainsi que deux manières courantes de les utiliser dans la pratique. À l'aide d'exemples simples, j'illustrerai les manières correctes et incorrectes d'utiliser les champs de tolérance (spécifications).
Remarque Sergey P. Grigoryev : L'article démontre clairement que l'ajustement opérationnel du processus par l'opérateur de la machine par rapport aux champs de tolérance n'a de sens que pour les processus instables et/ou non centrés dans le champ de tolérance, tandis que la correction des processus stables et des processus bien centrés dans le champ de tolérance conduisent à une variabilité encore plus grande (une plus grande diffusion des données autour de la moyenne), ce qui prive les travailleurs de la compréhension de « ce qui se passe ? en essayant d'améliorer la qualité des pièces qu'il produit.
Voix du client
Il y a environ 220 ans, Eli Whitney a créé une égreneuse à coton avec des pièces remplaçables. L’utilisation de pièces interchangeables constituait une avancée technologique de l’époque. Peu de temps après son succès avec l'égreneuse de coton, Whitney a reçu un contrat pour fournir à l'armée américaine des mousquets dotés de pièces interchangeables. En essayant de produire un grand nombre de pièces afin qu'elles puissent être utilisées de manière interchangeable, il a immédiatement découvert un fait qui hante chaque production depuis : il n'y a pas deux choses identiques.
Ainsi, au lieu de rendre les choses identiques, ils ont dû se contenter de les rendre similaires. Une fois qu’ils ont accepté cela, la question s’est immédiatement posée : « dans quelle mesure les pièces sont-elles suffisamment similaires ? » Pour tenter de répondre à cette question, des conditions techniques (champs de tolérance, spécifications) ont été créées. Il était évident que des écarts mineurs pouvaient être tolérés puisque les pièces fonctionneraient toujours. Cependant, à mesure que les variations augmentent, il viendra un moment où il reviendra moins cher de jeter la pièce que d’essayer de l’utiliser. Et les champs de tolérance (spécifications) étaient destinés à déterminer ce seuil de perte.
Il y a deux cents ans, l’économie de production de masse était telle qu’on pouvait tolérer de grandes quantités de déchets. Dans les années 1840, l’outil de jauge (réussite-échec) a été inventé. Dans les années 1860, cela a évolué vers la « jauge go-no-go » qui permettait de trier économiquement de grandes quantités de pièces en bonnes et mauvaises pièces. Cette technologie des années 1860 est toujours utilisée aujourd’hui. Des champs de tolérance ont été créés pour séparer les produits acceptables des produits inacceptables. Chaque fois qu'un flux de produits contient des éléments non conformes pouvant être identifiés par des tests non destructifs, le recours à des tests à 100 % reste une stratégie raisonnable lorsqu'elle peut être réalisée de manière économiquement réalisable. Une fois que vous avez brûlé votre pain grillé, que pouvez-vous faire à part nettoyer les morceaux brûlés ?
Exemple
Les figures 1 et 2 montrent les 100 valeurs de test finales ainsi que leur histogramme et la carte X Shewhart pour les valeurs individuelles. Ces valeurs sont dérivées d'une opération de fabrication dans l'une des usines de mon client. Les bandes de tolérance pour ces valeurs vont de 67 à 71. L'histogramme montre que ce processus n'a qu'un rendement de 34 %, tandis que la carte X montre que ce processus fonctionne de manière imprévisible. La marge de tolérance nous permet de différencier les articles conformes et non conformes, mais un rendement de 34 pour cent est inacceptable.
Avez-vous besoin de faire quelque chose ?
Une solution populaire consiste à essayer d’améliorer le rendement en procédant aux ajustements appropriés du processus. Supposons que nous puissions ajuster le processus après chaque résultat de mesure d'une pièce sélectionnée pour l'inspection (test) et que chaque ajustement affectera les produits fabriqués ultérieurement. Nous utiliserons les limites de tolérance de 67 et 71 pour déterminer la zone morte de nos ajustements. Autrement dit, nous ajusterons le processus uniquement lorsque nous recevrons un résultat de test inapproprié. Si, disons, nous avons un résultat de test de 65, alors nous ajusterons le processus de 4 pour cibler le processus à une valeur de tolérance moyenne de 69, et si nous avons un résultat de 75, alors nous ajusterons le processus de 4 à la baisse. 6. Cependant, si le résultat du test est 67, 68, 69, 70 ou 71, nous n'apporterons aucune modification à ce processus. Nous appellerons par la suite ce type de réglage « contrôleur P ».
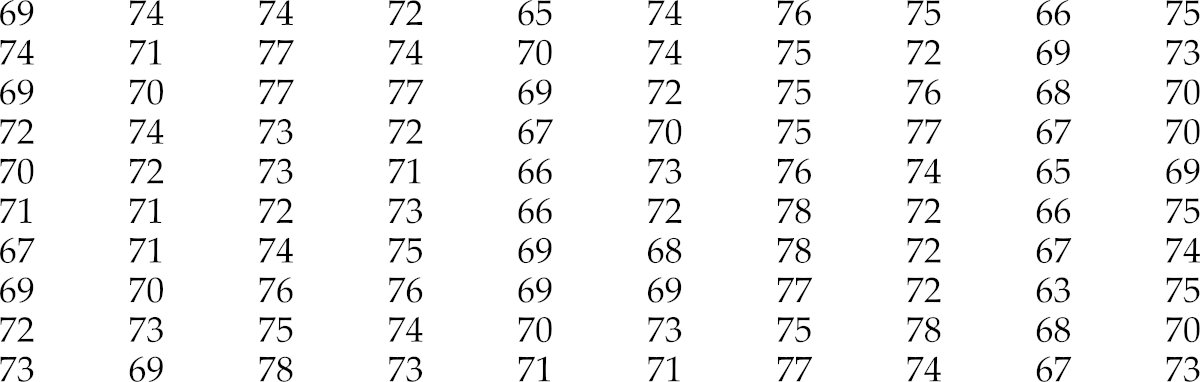
Vous pouvez télécharger les données de la liste triée au format CSV pour construire votre propre carte de contrôle XmR : télécharger .
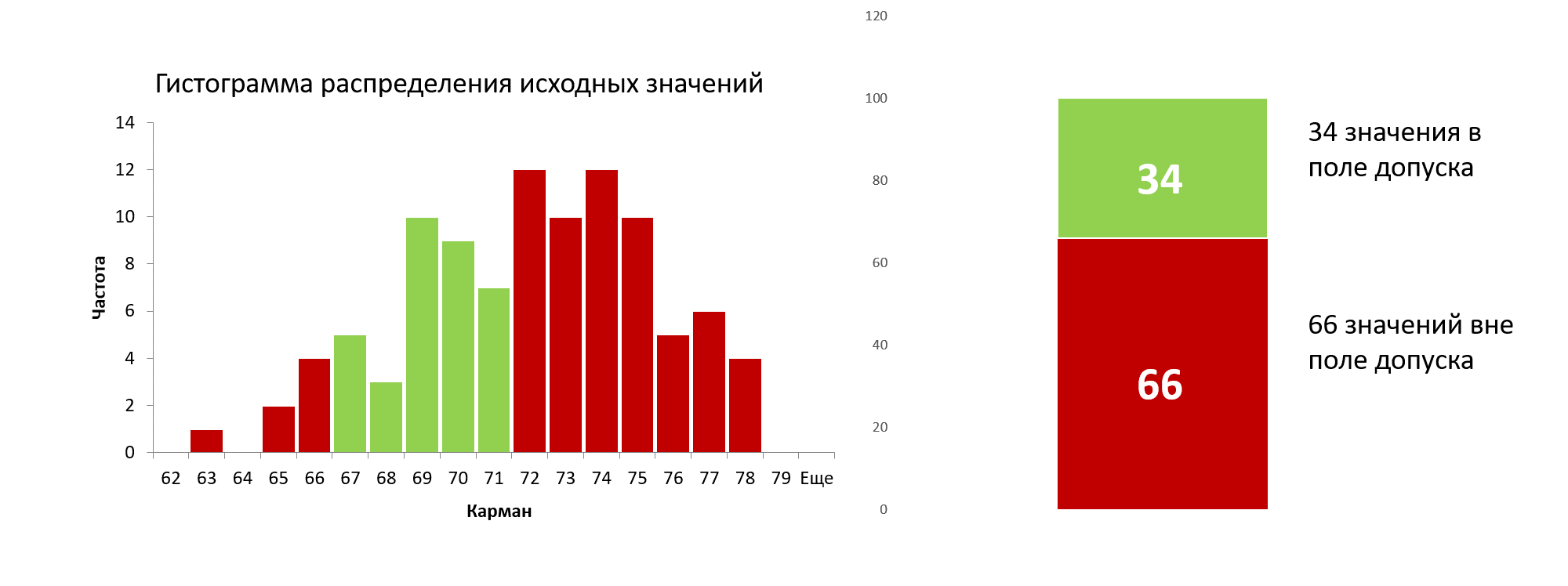
Figure 1 : Histogramme de la distribution de 100 valeurs initiales d'un procédé instable et mal centré avant ajustement.
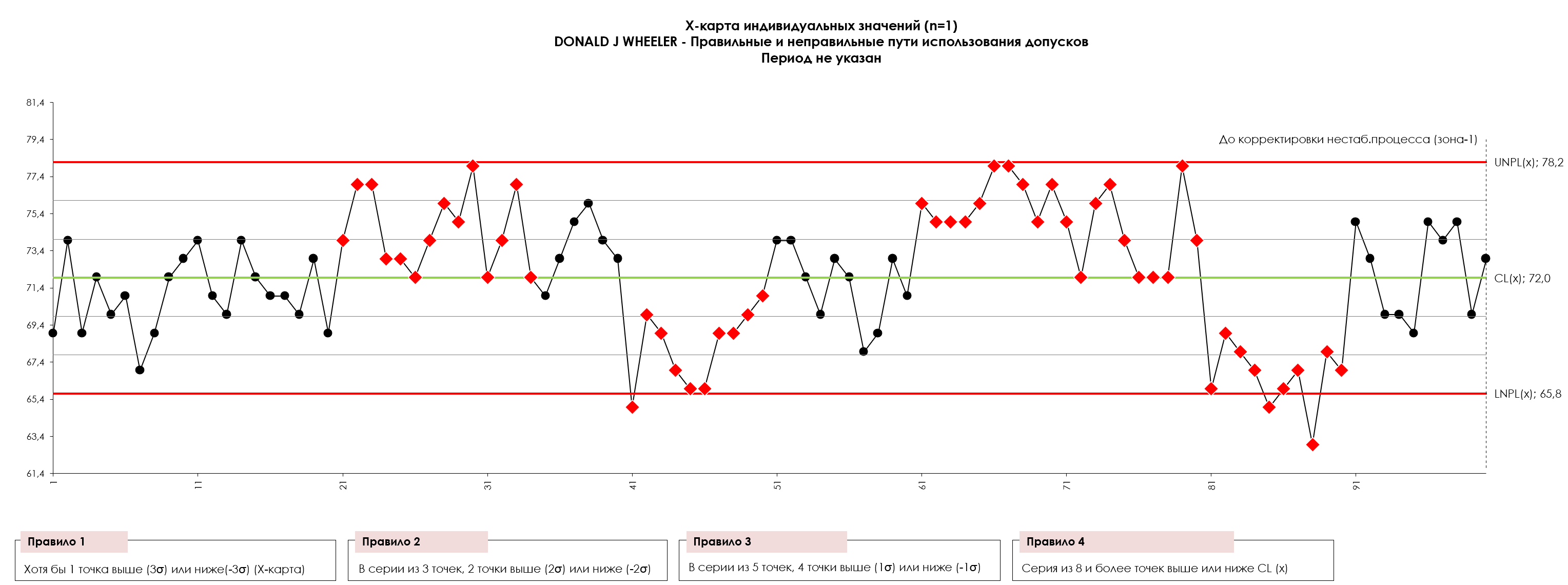
Figure 2 : X-map des valeurs individuelles (voix du processus) 100 valeurs initiales d'un processus instable et mal centré avant correction de l'opérateur. Les lignes rouges sont respectivement les limites naturelles supérieure et inférieure du processus, la ligne verte est la ligne centrale (moyenne) du processus. Les points rouges (séries de points) signalent la présence de causes particulières, indiquant un état statistiquement incontrôlable du processus. Le dessin a été préparé à l'aide de notre logiciel développé « Cartes de contrôle Shewhart PRO-Analyst +AI (pour Windows, Mac, Linux) » .
La figure 2 animée ci-dessous montre comment la procédure d'ajustement fonctionnera avec les données originales de la figure 1. Par exemple, une valeur initiale de 69 n'entraînera pas l'ajustement des valeurs ultérieures. Une deuxième valeur de 74, plus un ajustement de zéro à la mesure précédente, donne une valeur ajustée de 74. Cela entraîne un ajustement de -5 à un objectif de processus de 69. Une troisième valeur de 69 plus un ajustement de mesure précédent de - 5 donne une troisième valeur ajustée de 64. Cela entraîne un ajustement de +5 valeurs de processus suivantes, etc.
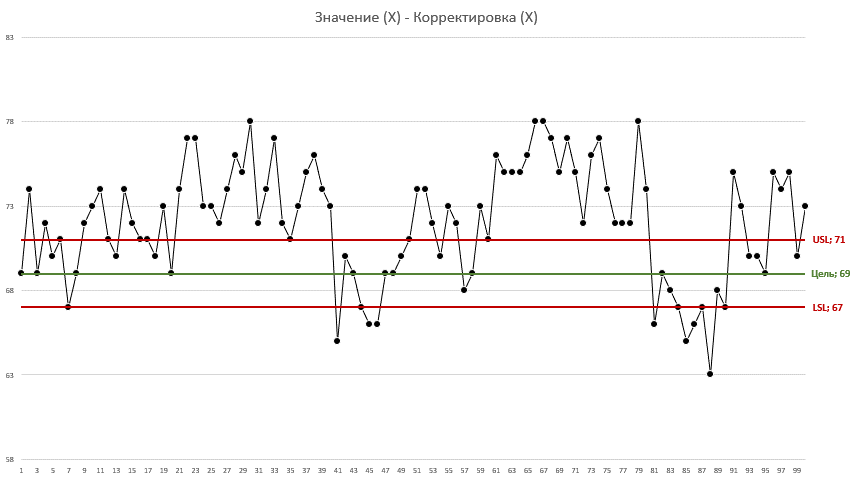
Figure 3 : L'animation de l'évolution des 100 valeurs initiales comme un processus instable et mal centré est corrigée. USL est la limite supérieure de la tolérance, Target est la valeur nominale du champ de tolérance, LSL est la limite inférieure du champ de tolérance.
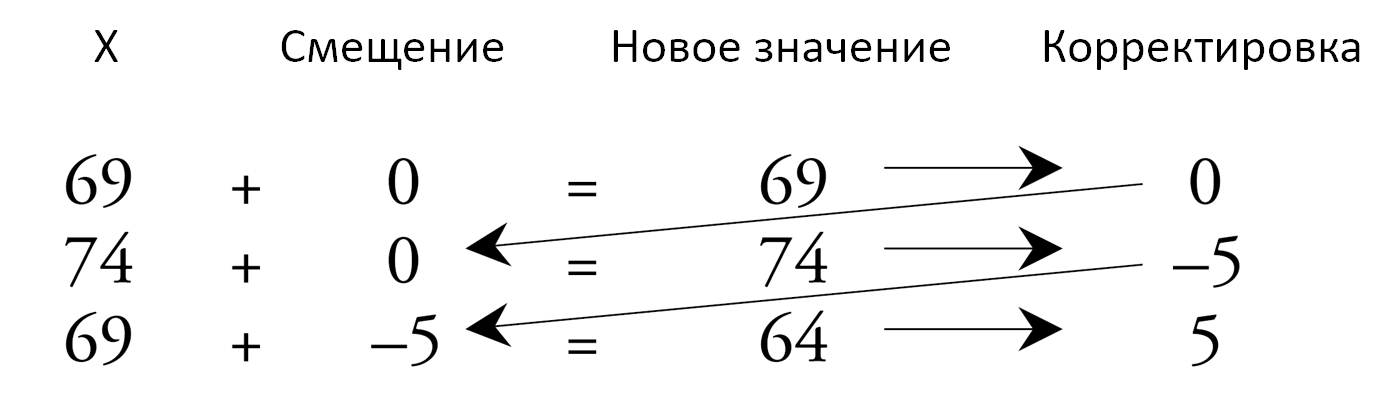
Figure 4 : Règle de réglage du procédé par mesure d'une pièce « défectueuse ».
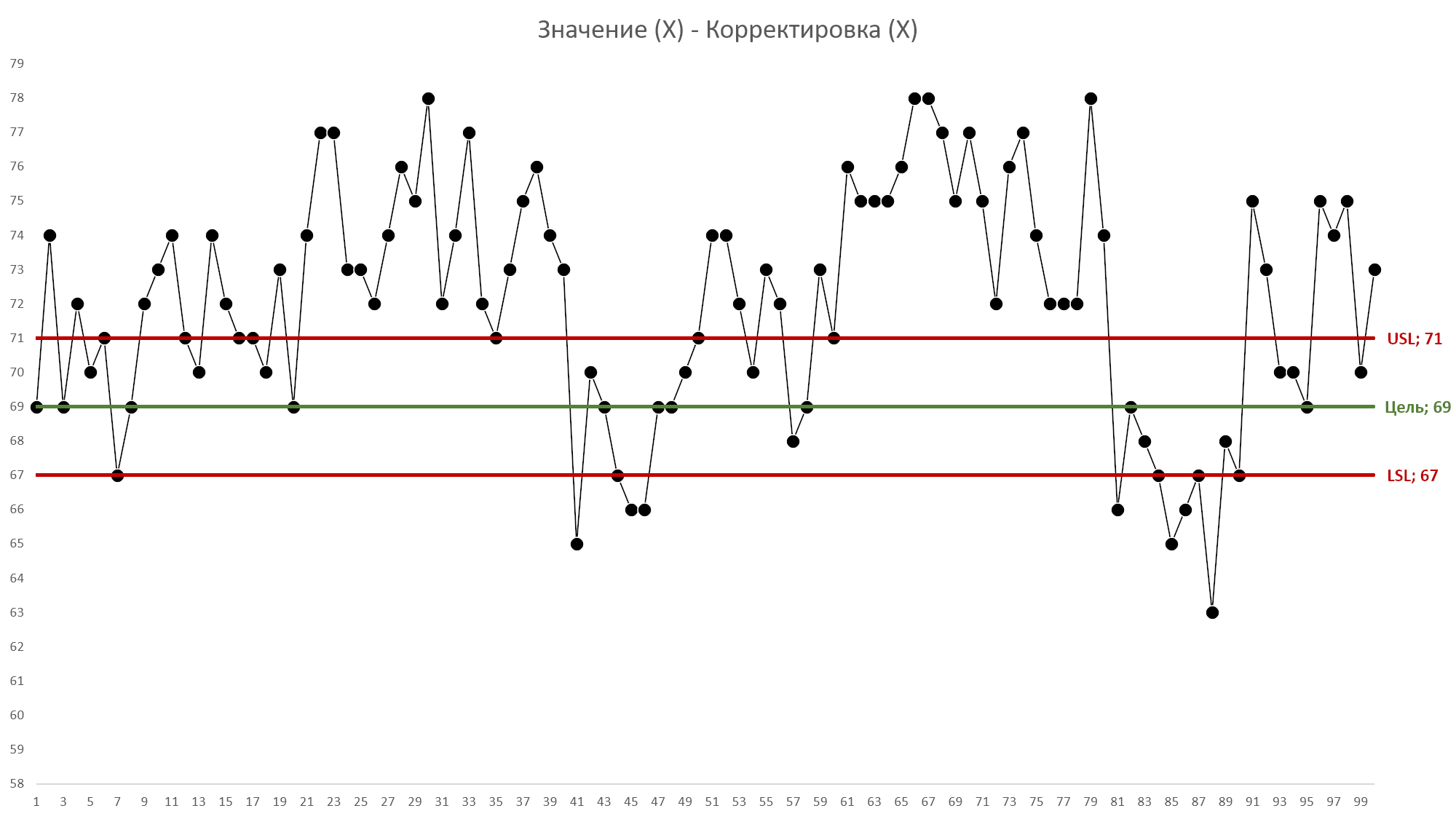
Figure 5 : Graphique de 100 (cent) valeurs initiales avant ajustement d'un processus instable et mal centré par rapport aux champs de tolérance (voix du client). USL est la limite supérieure de la tolérance, Target est la valeur nominale du champ de tolérance, LSL est la limite inférieure du champ de tolérance.
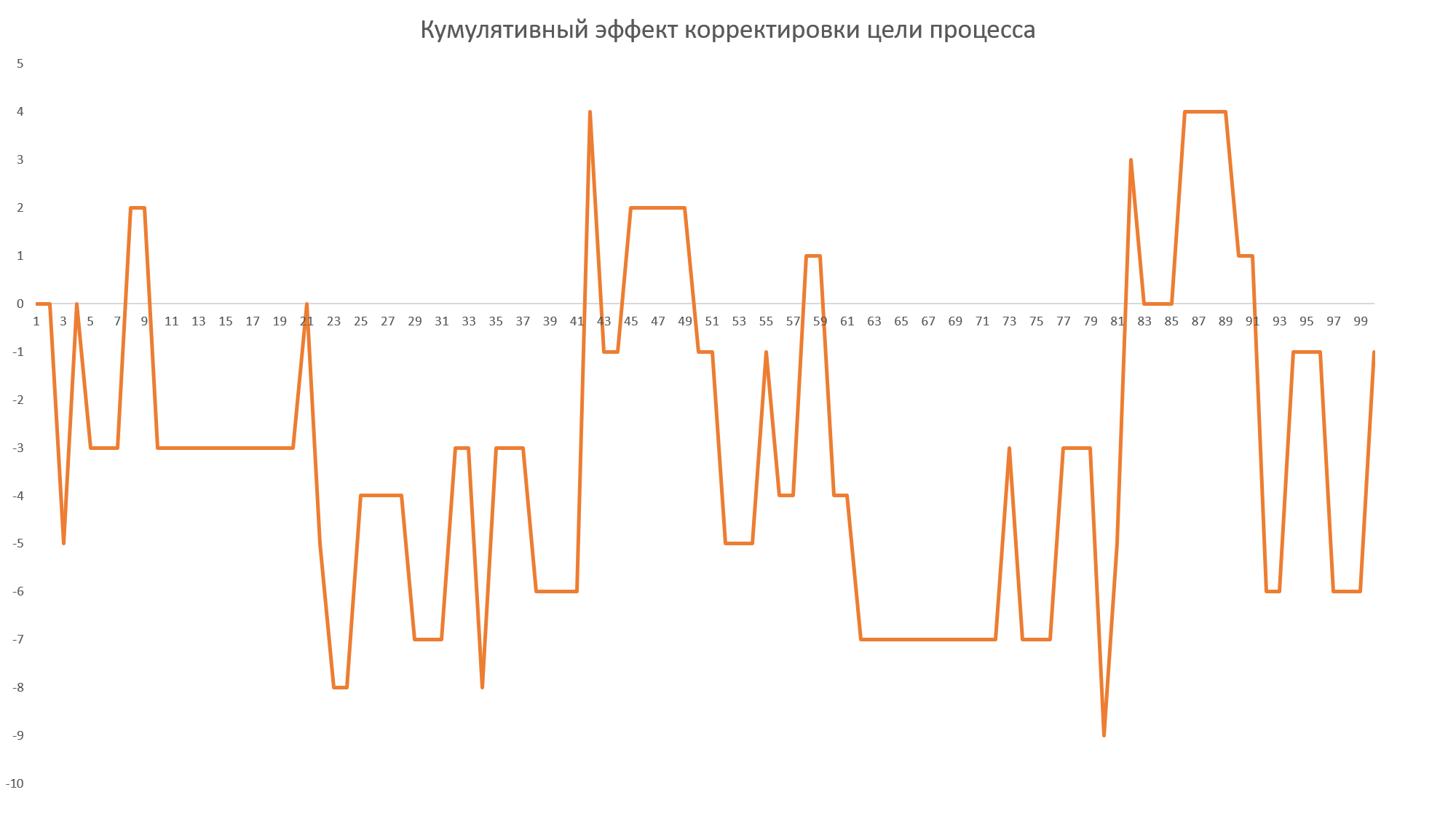
Figure 6 : Effet cumulatif de l’ajustement d’un processus incontrôlé et mal centré.
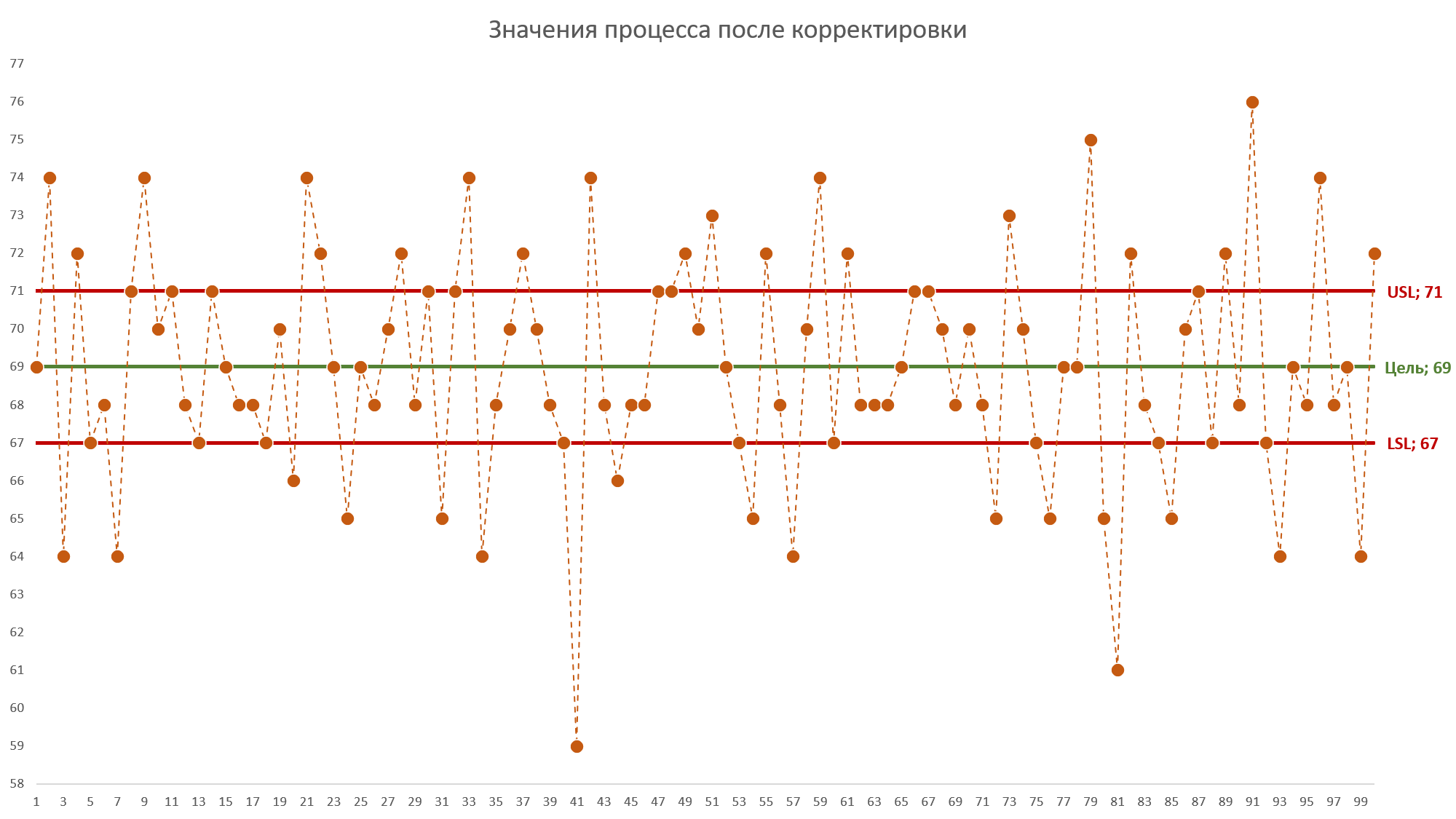
Figure 7 : Données résultant d'un processus incontrôlé et mal centré après conversion par un contrôleur P utilisant des bandes de tolérance comme zone morte. USL est la limite supérieure de la tolérance, Target est la valeur nominale du champ de tolérance, LSL est la limite inférieure du champ de tolérance.
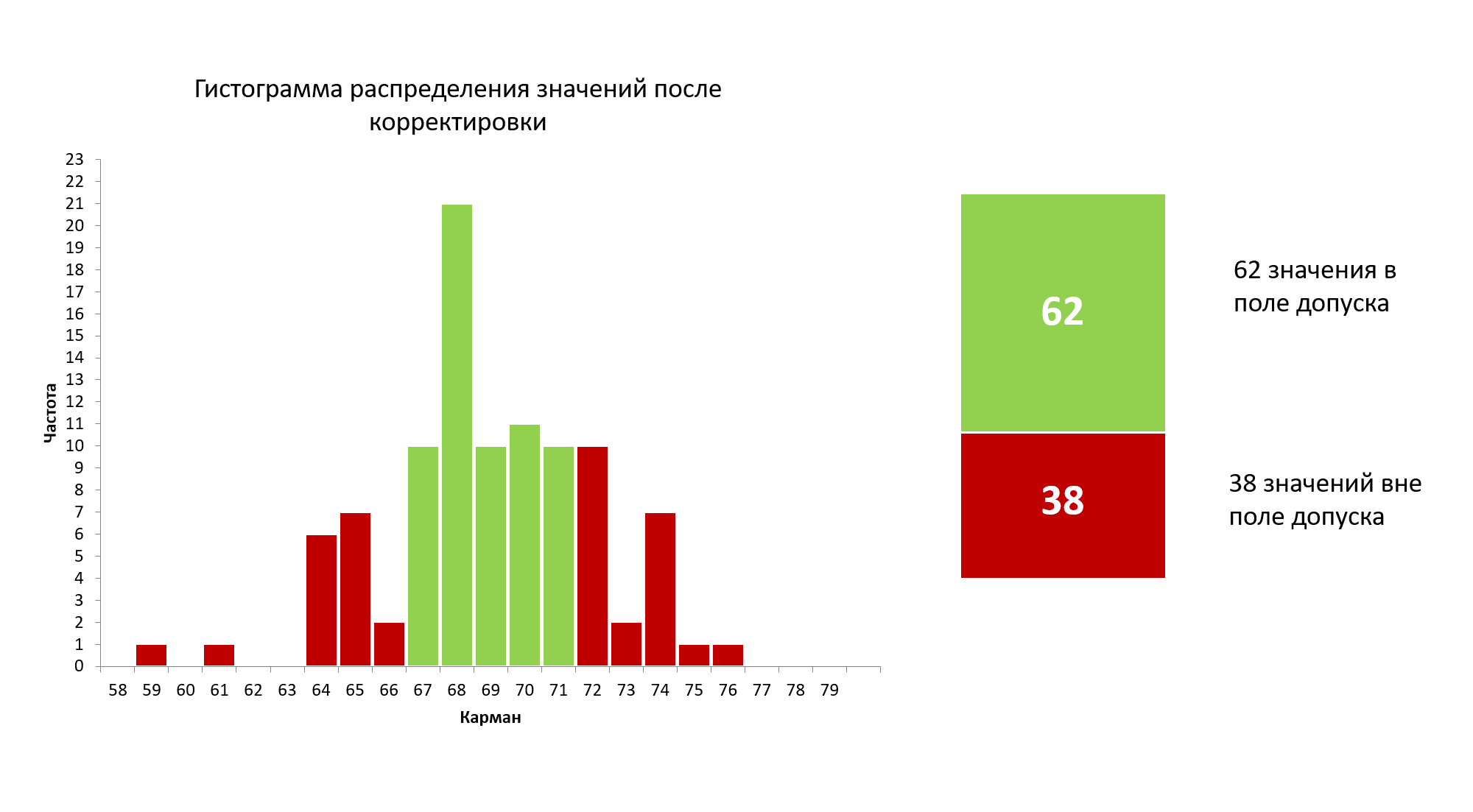
Figure 8 : Histogramme de la distribution de 100 nouvelles valeurs après correction d'un processus instable et mal centré.
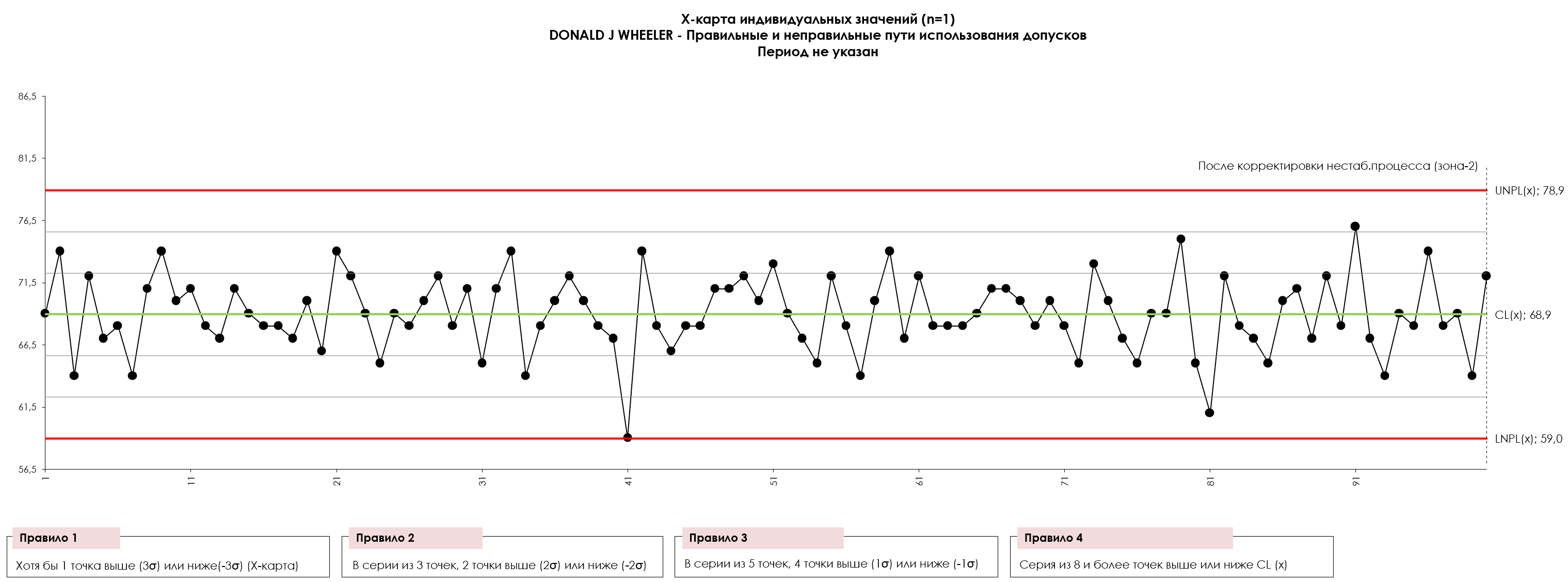
Figure 8.1. : Carte X des valeurs individuelles (voix de processus) 100 valeurs après correction par l'opérateur du processus instable et biaisé (non centré) illustré à la figure 2. démontre un état statistiquement stable. Le dessin a été préparé à l'aide de notre logiciel développé « Cartes de contrôle Shewhart PRO-Analyst +AI (pour Windows, Mac, Linux) » .
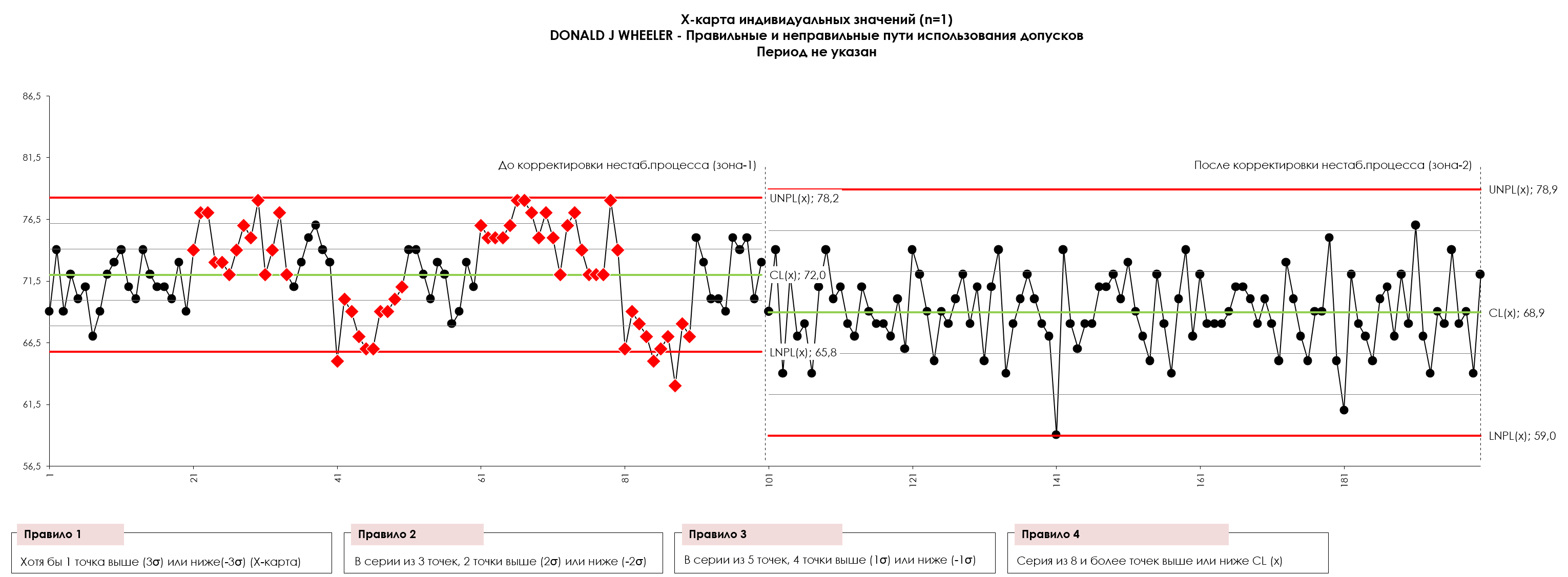
Figure 8.2. : Carte X de valeurs individuelles (voix de processus) de 100 valeurs avant (zone-1) et après (zone-2) correction d'un processus instable et biaisé (non centré) démontre une stabilité statistique État. Le dessin a été préparé à l'aide de notre logiciel développé « Cartes de contrôle Shewhart PRO-Analyst +AI (pour Windows, Mac, Linux) » .
Alors, comment avons-nous fait face ? Le contrôleur P utilisant des limites de tolérance pour déterminer la zone morte a augmenté le rendement de 34 pour cent à 62 pour cent. Une amélioration très impressionnante. Cela s'est produit parce que ce processus n'était pas concentré dans la zone de tolérance et était contrôlé de manière imprévisible. En raison de ces deux aspects des données présentées dans la figure 2, bon nombre des trente-deux (32) ajustements étaient en fait nécessaires pour une amélioration, et par conséquent, le contrôleur P a amélioré les performances.
Cependant, un rendement de 62 pour cent n’était pas tout ce que le procédé était capable de réaliser. Ca aurait pu être mieux. Une fois que nous avons identifié les causes particulières de la variation exceptionnelle illustrée à la figure 2 et pris des mesures pour contrôler ces causes particulières en production, nous avons abouti au processus illustré à la figure 9 (ci-dessous).
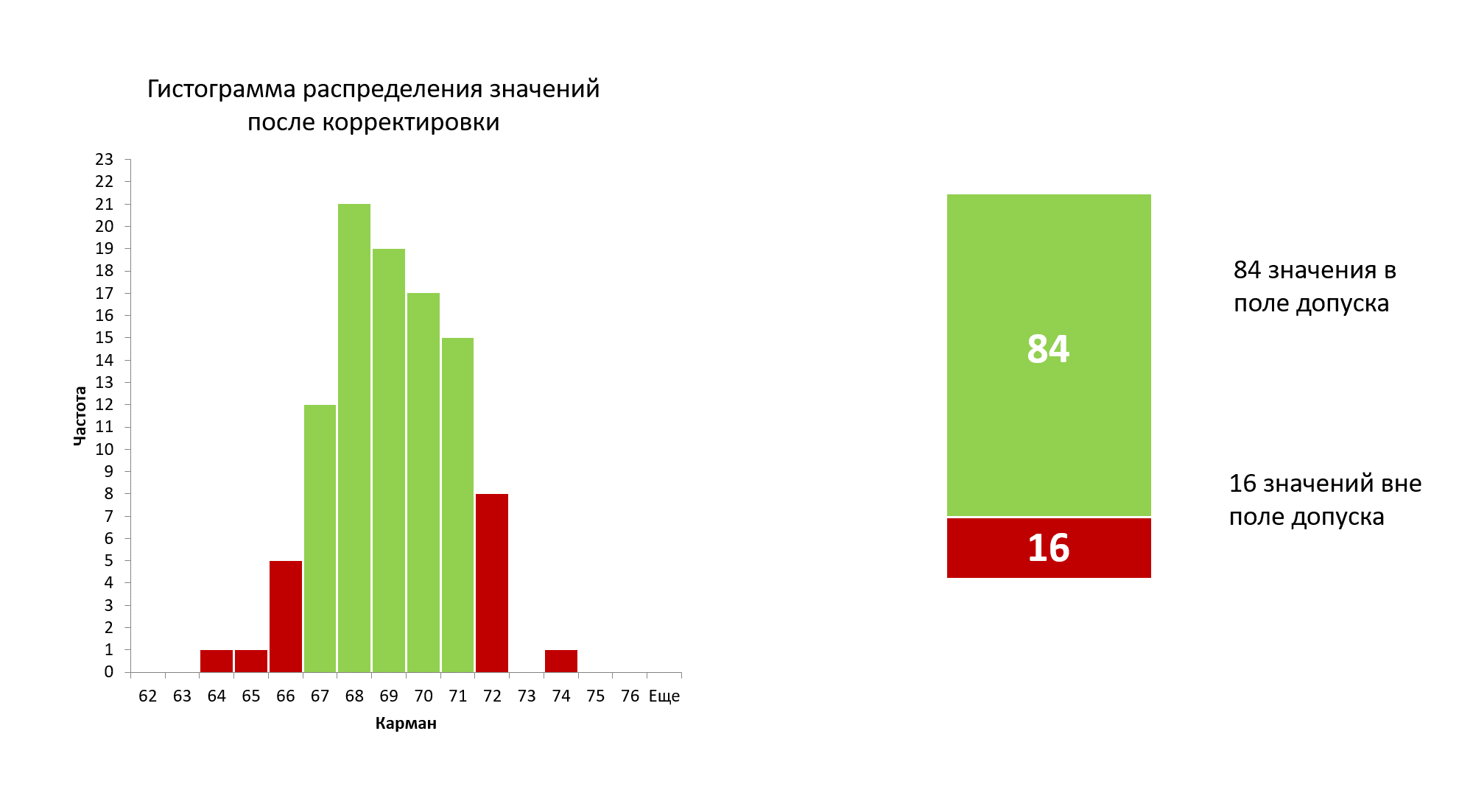
Figure 9 : Histogramme de la distribution de 100 nouvelles valeurs après suppression des causes particulières de variabilité précédemment identifiées.
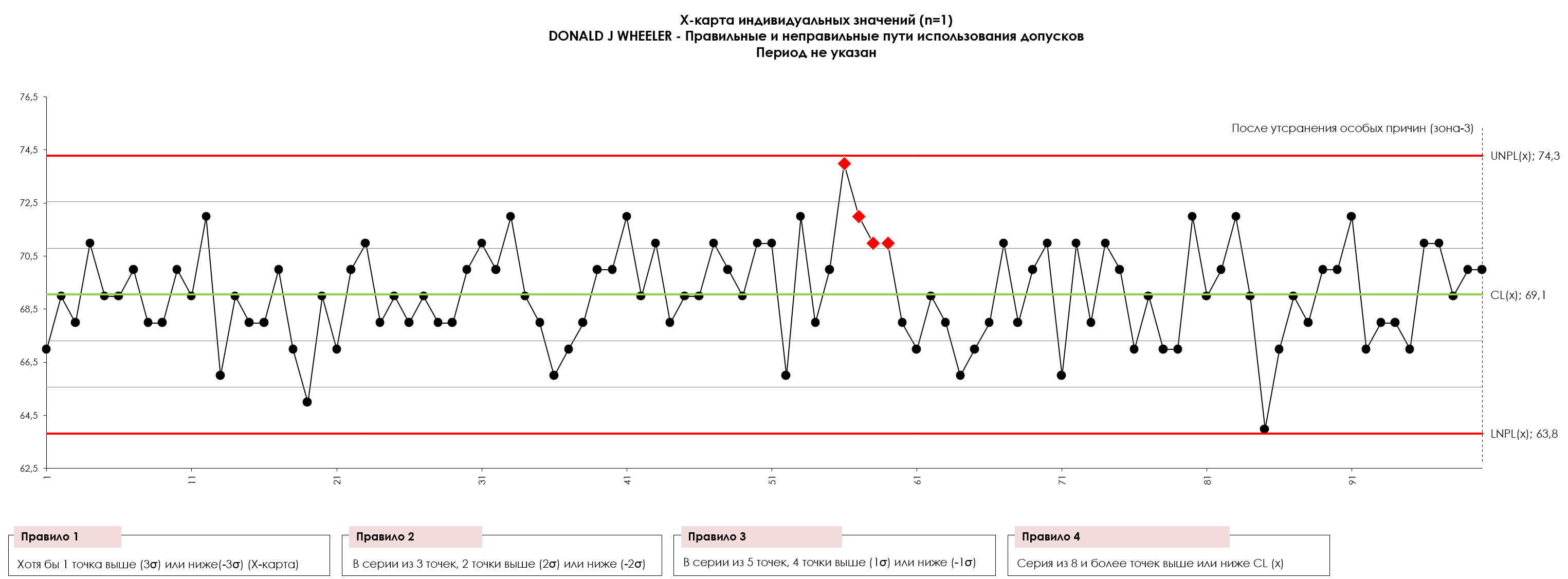
Figure 10 : Carte X des valeurs individuelles (voix de processus) 100 valeurs. Le processus illustré dans la figure fonctionne de manière tout à fait prévisible. Les causes particulières de variation précédemment manifestées ont été éliminées, à l'exception d'une série de points 55, 56, 57, 58, 59, 60 dans lesquels d'éventuelles nouvelles causes particulières de variabilité sont apparues. UNPL est la limite naturelle supérieure de contrôle du procédé, LNPL est la limite inférieure de contrôle naturel du procédé, CL est la ligne médiane (moyenne). Le dessin a été préparé à l'aide de notre logiciel développé
« Cartes de contrôle Shewhart PRO-Analyst +AI (pour Windows, Mac, Linux) »
.
Remarque Sergey P. Grigoryev : Vous pouvez télécharger les données de processus stabilisées dans une liste triée au format CSV pour créer indépendamment un diagramme XmR de contrôle :
télécharger
.
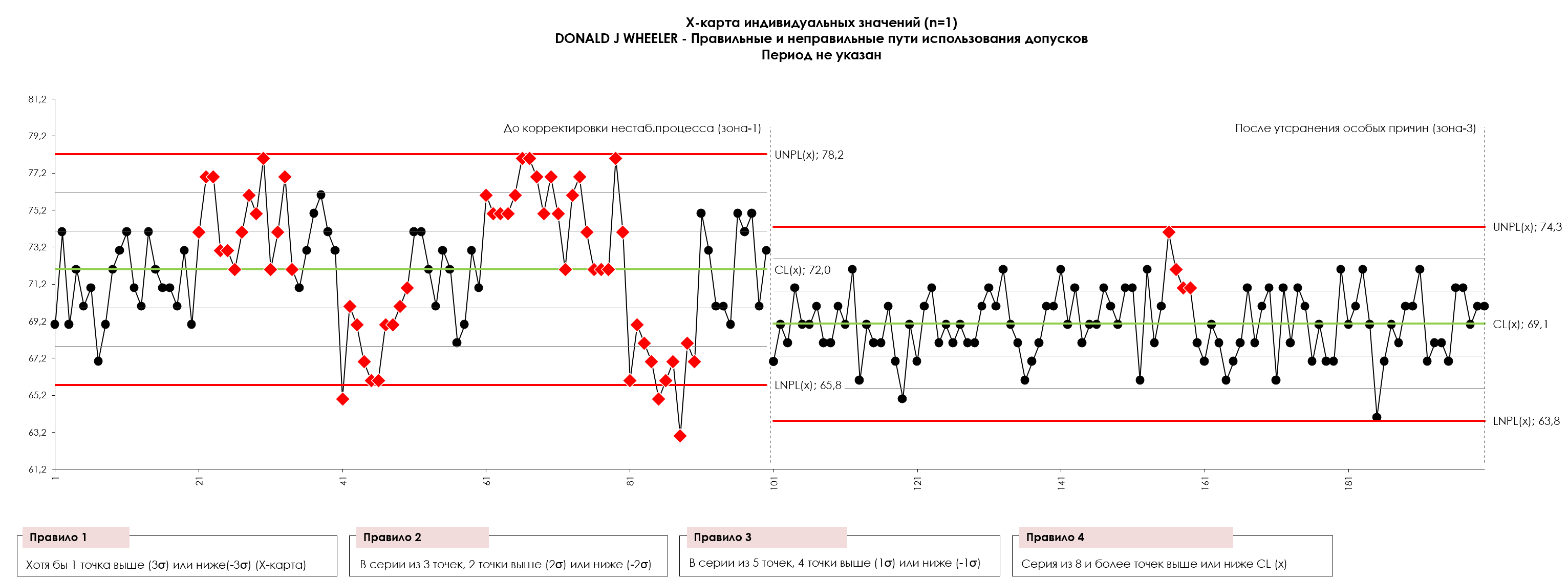
Figure 10.1 : Carte X de valeurs individuelles (voix de processus) de 100 valeurs avant d'éliminer les causes particulières de variabilité dans un processus instable (Zone-1) et après (Zone-3). UNPL est la limite naturelle supérieure de contrôle du procédé, LNPL est la limite inférieure de contrôle naturel du procédé, CL est la ligne médiane (moyenne). Le dessin a été préparé à l'aide de notre logiciel développé « Cartes de contrôle Shewhart PRO-Analyst +AI (pour Windows, Mac, Linux) » .
Lorsqu'ils ont commencé à gérer ce processus de manière prévisible et jusqu'à atteindre son objectif (valeur de tolérance), leur rendement a atteint 84 pour cent. C’est là tout le potentiel de ce processus dans son état actuel. Un rendement de 84 pour cent n’est pas un objectif impossible, mais simplement ce que le procédé est capable de produire lorsqu’il fonctionne à son plein potentiel. Le travail prédictif minimisera la variation des résultats du processus, tandis que les objectifs de travail en fonction du processus maximiseront la conformité du produit fabriqué.
Essayons d'améliorer un processus stable en utilisant la même méthode
Mais le processus ne permet toujours pas de produire des produits conformes à 100 %. Ne pouvons-nous pas faire quelque chose concernant les 16 pour cent de produits non conformes ? Et si nous appliquions un contrôleur P avec une zone morte dans le champ de tolérance des données de la figure 10 ? Lorsque nous faisons cela, nous obtenons les données de la figure 11.
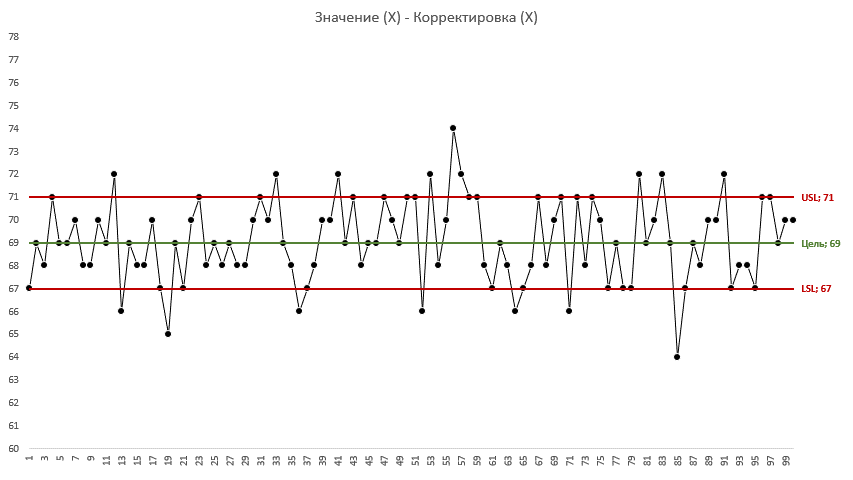
Figure 11 : Animation de l'évolution des 100 valeurs initiales alors qu'un processus stable et bien centré est ajusté. USL est la limite supérieure de la tolérance, Target est la valeur nominale du champ de tolérance, LSL est la limite inférieure du champ de tolérance.
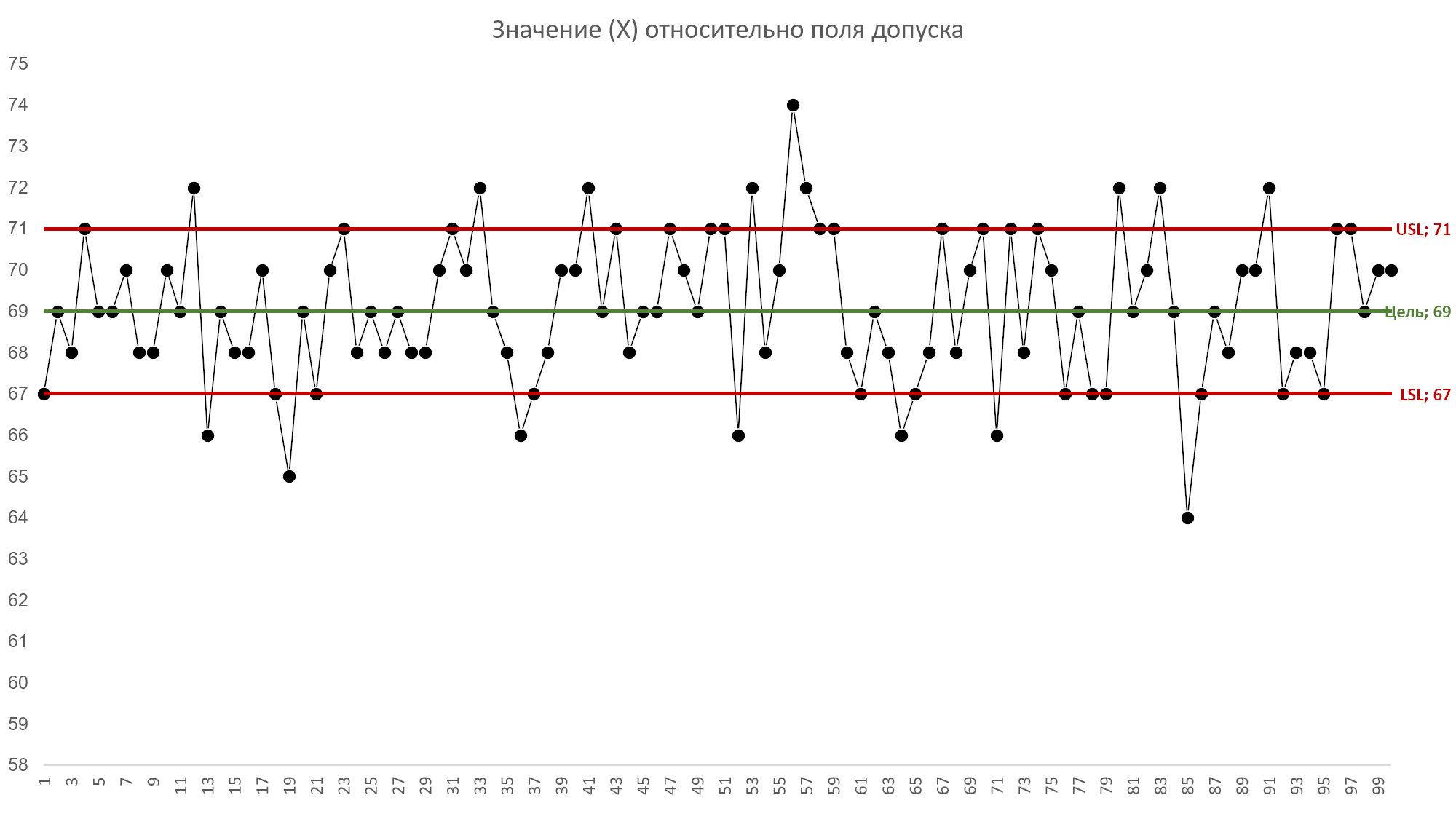
Figure 12 : Tracé d'une centaine de valeurs initiales avant d'ajuster un processus stable et bien centré par rapport aux marges de tolérance (voix du client). USL est la limite supérieure de la tolérance, Target est la valeur nominale du champ de tolérance, LSL est la limite inférieure du champ de tolérance.
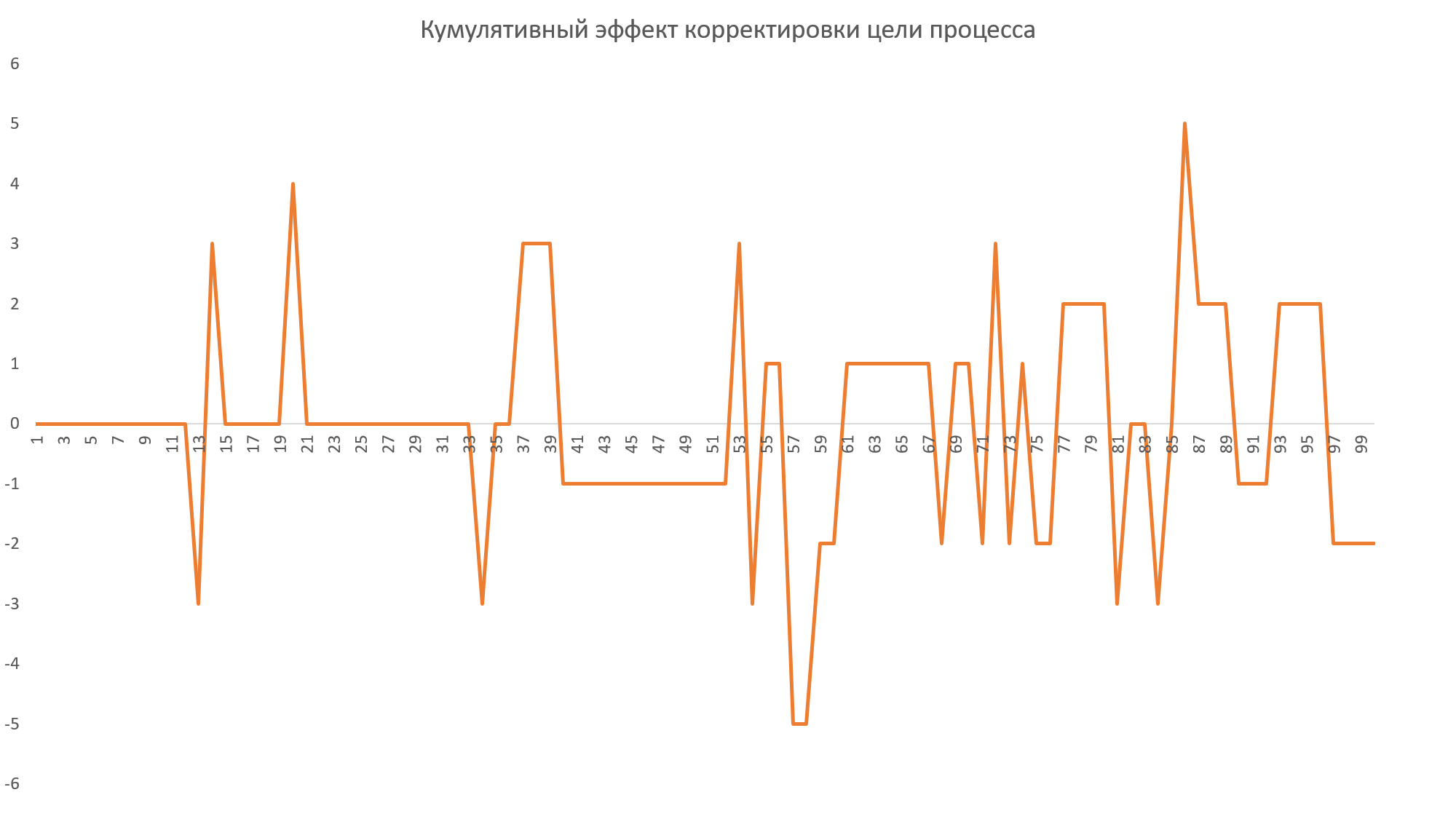
Figure 13 : Effet cumulatif de l’ajustement d’un processus stable et bien centré.
Note de Sergey P. Grigoryev : Veuillez noter que le graphique de l'effet cumulatif des ajustements pour un processus stable et bien centré présenté dans la figure 13 diffère par sa symétrie par rapport à l'axe (X) du même graphique pour un processus instable et non centré. (Figure 6). Ce qui, dans le cas de la figure 13, suggère qu'en essayant d'ajuster un processus stable et bien centré, nous nous contentions de déplacer certaines valeurs vers le bas et d'autres vers le haut, ne faisant qu'empirer les choses. "Nous voulions le meilleur, mais cela s'est avéré comme toujours." - CONTRE. Tchernomyrdine.
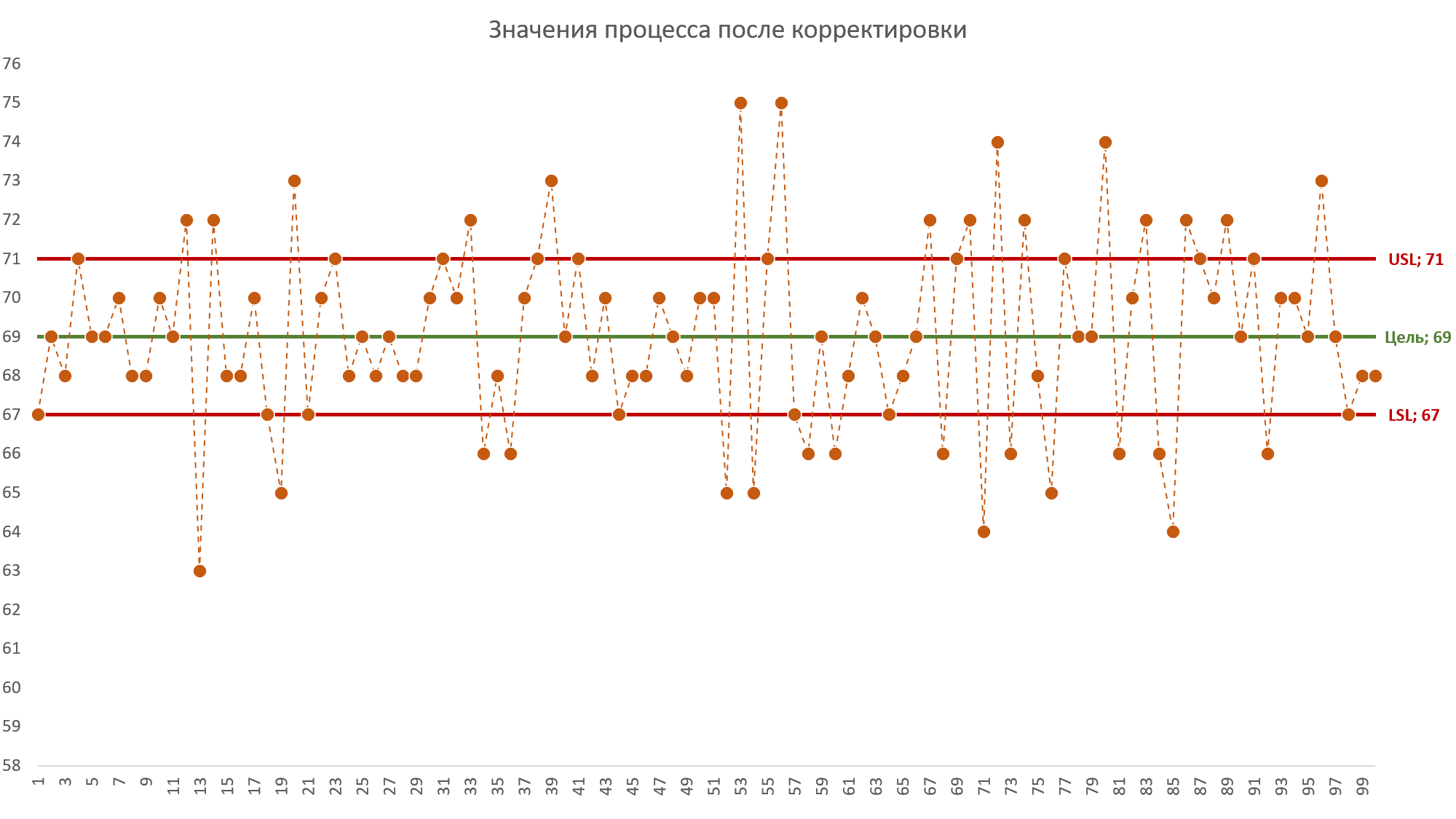
Figure 14 : Données résultantes d'un processus stable et bien centré après conversion par un contrôleur P utilisant des bandes de tolérance comme bande morte. USL est la limite supérieure de la tolérance, Target est la valeur nominale du champ de tolérance, LSL est la limite inférieure du champ de tolérance.
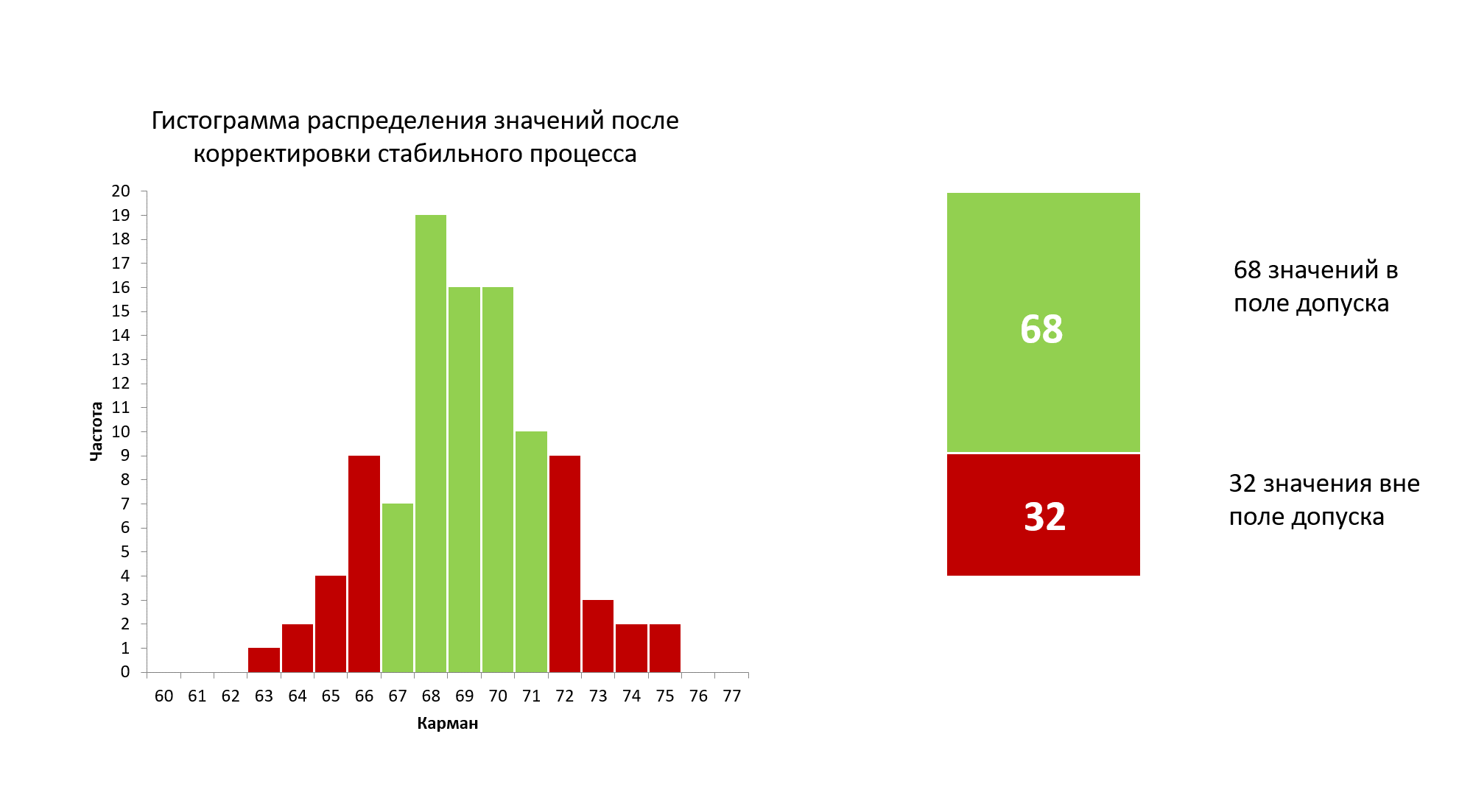
Figure 15 : Histogramme de la distribution de 100 nouvelles valeurs après tentatives d'ajustement d'un processus stable et bien centré.
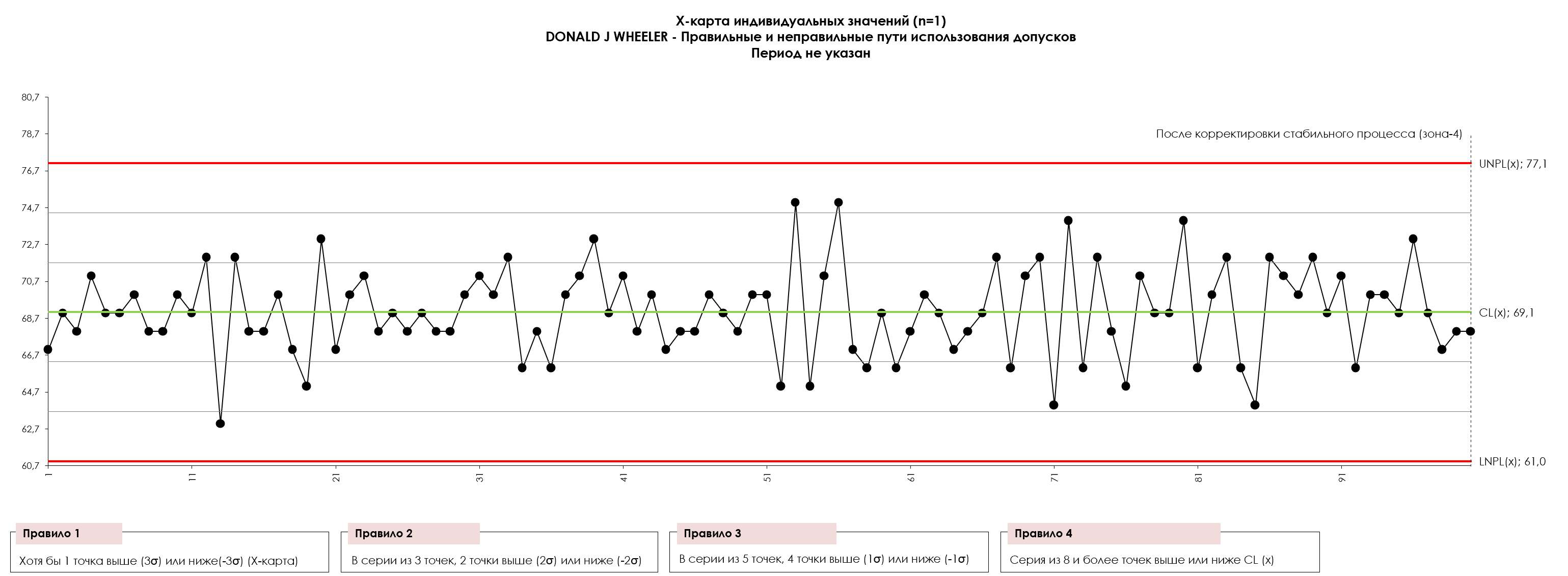
Figure 16. Carte X de valeurs individuelles (voix de processus) de 100 valeurs après avoir tenté d'ajuster un processus stable et bien centré. UNPL est la limite naturelle supérieure de contrôle du procédé, LNPL est la limite inférieure de contrôle naturel du procédé, CL est la ligne médiane (moyenne). Le dessin a été préparé à l'aide de notre logiciel développé « Cartes de contrôle Shewhart PRO-Analyst +AI (pour Windows, Mac, Linux) » .
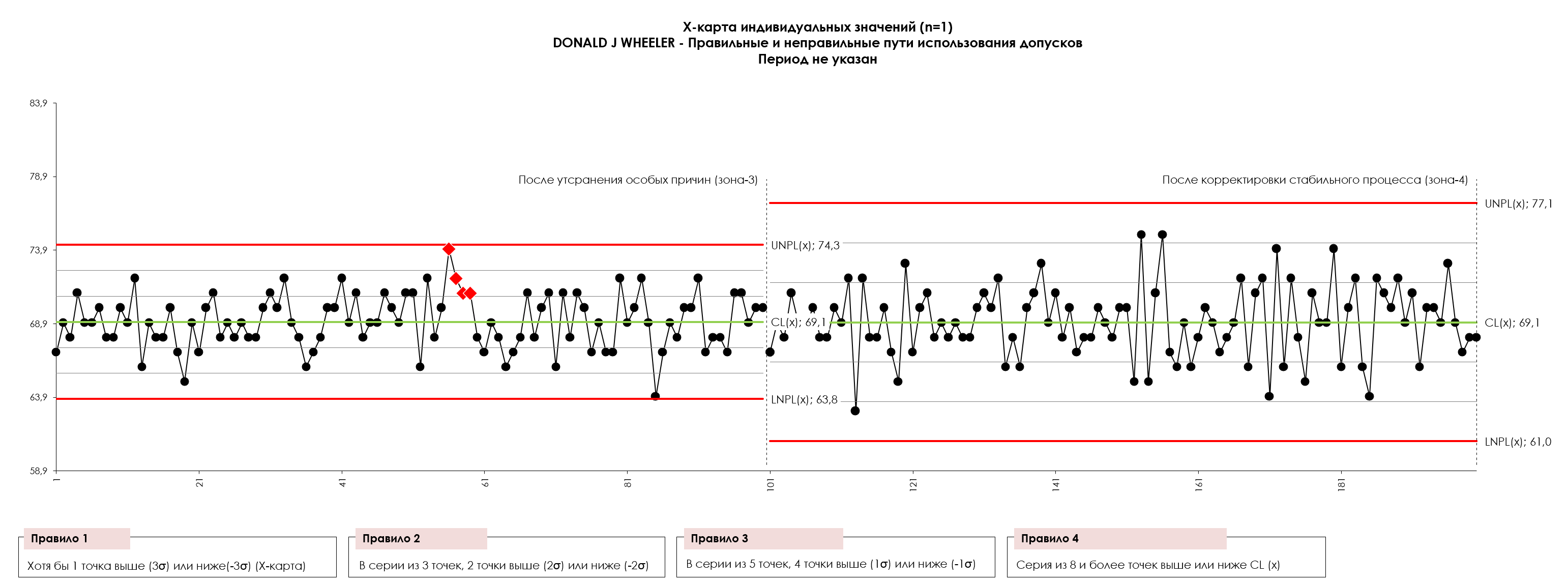
Graphique 16.1. Carte X des valeurs individuelles (voix du processus) 100 valeurs avant (Zone-3) après (Zone-4) la tentative de l'opérateur de corriger un processus stable et bien centré. UNPL est la limite naturelle supérieure de contrôle du procédé, LNPL est la limite inférieure de contrôle naturel du procédé, CL est la ligne médiane (moyenne). Le dessin a été préparé à l'aide de notre logiciel développé « Cartes de contrôle Shewhart PRO-Analyst +AI (pour Windows, Mac, Linux) » .
Ici, le contrôleur P, utilisant la bande de tolérance comme zone morte, a converti un processus présentant un taux de conformité de 84 % en un autre processus présentant un taux de conformité de 68 % ! La part des produits non conformes a doublé, passant de 16 à 32 pour cent.
Pourquoi est-ce arrivé? Cela était dû au fait que le contrôleur P réagissait au bruit et effectuait des réglages inappropriés. Avec seulement quelques ajustements dans le premier cas (Figure 2), le contrôleur P a commencé à produire des résultats positifs, mais finalement les ajustements inutiles ont éloigné le processus de l'objectif et ont aggravé la situation.
Note de Sergey P. Grigoryev : Pour tenter d'améliorer un processus stable, il a fallu procéder à 32 ajustements. Le temps perdu pour les ajustements n'a fait qu'aggraver la situation avec les mêmes actions que dans le premier cas (Figure 2). Cela peut plonger tout opérateur hautement qualifié dans une stupeur totale. Que pensez-vous que l’opérateur fera dans ce cas ? La direction l'aidera-t-elle à résoudre ce problème ? Oh, si seulement la direction pouvait savoir ça ! Le résultat de toute tentative de correction d'un processus bien centré et stable est expliqué dans un langage simple dans l'expérience avec entonnoir et cible Edouard Deming.
« Nous allons tout détruire nous-mêmes grâce à nos propres efforts persistants. »
Sur la figure 2, le processus n'était pas centré dans le champ de tolérance et se comportait de manière imprévisible. Là, le contrôleur P, utilisant la bande de tolérance comme bande morte, a vraiment amélioré les choses. Dans la figure 14, ce processus était centré et prévisible. Là, le contrôleur P a simplement ajouté du bruit au processus, ce qui a augmenté la variation du flux de produit et a aggravé la situation.
Alors, à quelle conclusion en sommes-nous arrivés ? Pouvons-nous utiliser la tolérance pour réguler un processus qui se trouve dans un état statistiquement incontrôlable ? Bien qu'il soit préférable d'utiliser un contrôleur P utilisant la bande de tolérance comme zone morte que de ne rien faire, cela ne vous permet pas de tirer le meilleur parti de votre processus.
Pourquoi le contrôleur P est-il inefficace lorsque le processus fonctionne de manière prévisible et est centré dans la plage de tolérance ? Tous les mécanismes de contrôle de processus manuels et automatisés sont intrinsèquement réactifs. Qu'il s'agisse d'un simple contrôleur P ou d'un contrôleur PID plus complexe, ils ne peuvent pas agir tant qu'ils n'ont pas reçu un signal détecté. Étant donné que le processus initial était imprévisible et non centré dans la tolérance, le contrôleur P a capté de nombreux signaux réels. Cependant, il y avait également des signaux faibles (bruit) auxquels le contrôleur P répondait, ce qui entraînait des ajustements inutiles. Si la zone morte est complètement désaccordée avec la voix du processus, votre mécanisme d'ajustement du processus entraînera trop d'ajustements. Dans les deux cas, le résultat sera une variabilité accrue du flux de produits. L’utilisation d’un contrôleur automatique pour un processus stable entraîne généralement une plus grande variabilité que celle dont le processus est capable lorsqu’il fonctionne à son plein potentiel.
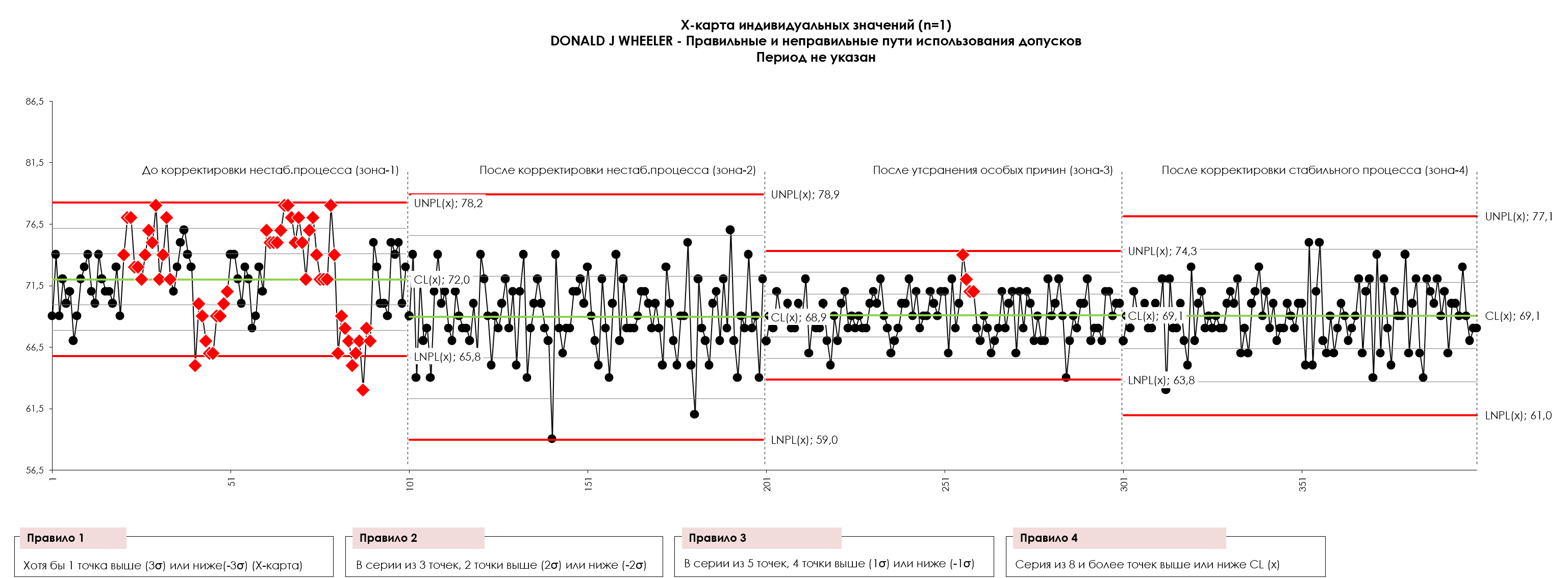
Figures 2 ; 8.1 ; dix; 16. Carte X des valeurs individuelles (voix de processus) 100 valeurs pour tous les cas abordés dans l'article ci-dessus. UNPL est la limite naturelle supérieure de contrôle du procédé, LNPL est la limite inférieure de contrôle naturel du procédé, CL est la ligne médiane (moyenne). Le dessin a été préparé à l'aide de notre logiciel développé « Cartes de contrôle Shewhart PRO-Analyst +AI (pour Windows, Mac, Linux) » .
Voir un exemple d'intervention d'un opérateur dans le processus de contrôle du débit de gaz dans une entreprise produisant du méthane biogénique dans l'article : Le concept de variabilité dans le contrôle des processus .
Erreur du premier type
- "Mais ça veut dire que vous ne réagirez pas aux valeurs hors spécifications !"
Oui, les valeurs non conformes de 64, 65, 66 et 72, 73, 74 font partie de ce que produit ce processus lorsqu'il se déroule de manière prévisible et bien centré dans la tolérance. Permettez-moi de répéter. Comme vous pouvez le voir sur les figures 9 et 10, lorsque ce processus fonctionne à son plein potentiel, il produira un produit compris entre 64 et 74 (axe Y). Prises une à la fois, ces valeurs ne signifient pas que quelque chose ne va pas avec le processus, même si elles peuvent être hors spécifications. Les champs de tolérance sont conçus pour trier les produits appropriés des produits inappropriés. Ils sont la voix du client, pas le processus. Les champs d’autorisation ne doivent jamais être confondus avec la voix du processus lui-même.
- « Êtes-vous en train de dire que je devrais ignorer les produits non conformes ?
Le produit non conforme doit être refusé. Mais si votre processus est contrôlé de manière prévisible et adapté à l’objectif, le fait qu’un élément ne soit pas conforme ne vous indique pas qu’un ajustement du processus est nécessaire.
Note de Sergey P. Grigoryev : Dans ce cas, d'autres améliorations nécessiteront des changements systémiques (changement de matières premières, de technologie, d'équipement, d'outils, formation des opérateurs, etc.).
Bien entendu, le contrôle des processus ne peut pas être contrôlé de manière prévisible et centralisée sans tracer un diagramme de comportement du processus (graphique Shewhart XmR des valeurs individuelles), il ne devrait donc y avoir aucune conjecture. Si vous ne disposez pas d'un diagramme de comportement de processus, il y a au moins 10 chances sur 1 que vous exécutiez votre processus de manière imprévisible. Si tel est le cas, un contrôleur de processus automatique ne vous permettra d'obtenir qu'une fraction de ce dont votre processus est capable.
Information brève
Le mouvement moderne de qualité consiste à apprendre à arrêter de brûler des toasts. Cela ne veut pas dire que nous n’aurons pas à éplucher les toasts de temps en temps ; cela signifie que nous avançons en amont pour travailler sur le processus plutôt que de trier les bons matériaux des mauvais à la fin de la chaîne de production. Les champs de tolérance sont toujours d’actualité, ils définissent toujours la voix du client, mais il est important de les distinguer de la voix du processus. Même si nous souhaitons que la voix du processus soit alignée sur les champs de tolérance (voix du client), les champs de tolérance ne fournissent pas les informations correctes sur ce qui doit être fait pour exploiter tout le potentiel de votre processus.
Un autre cas simple (Sergey P. Grigoryev)
Je suis sûr qu'il est nécessaire de considérer une autre situation où le processus est dans un état statistiquement stable (contrôlé), mais n'est pas centré dans le champ de tolérance. Dans un exemple d'un tel processus, 77 valeurs sont en dehors de la plage de tolérance.
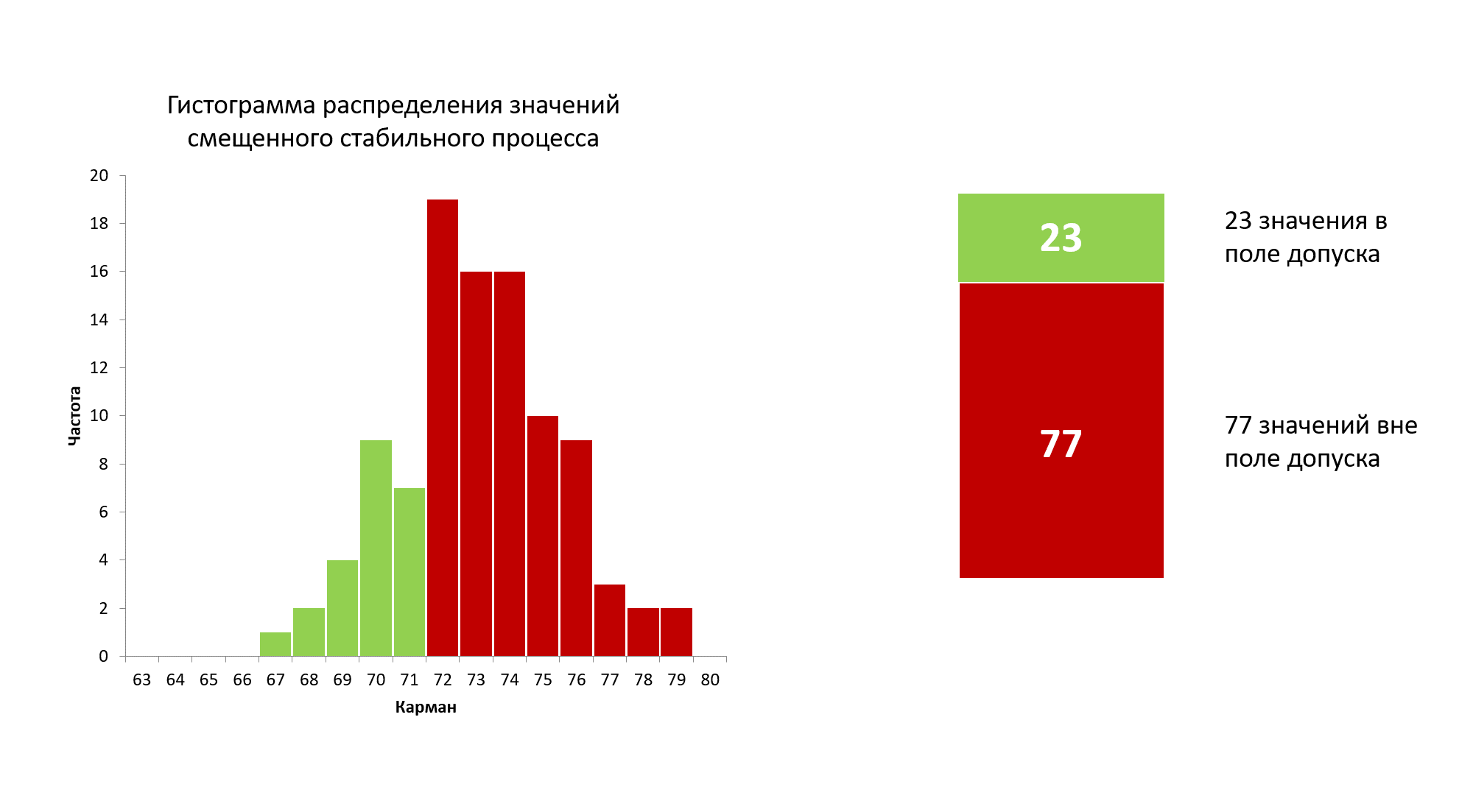
Figure 17 : Histogramme de la distribution de 100 valeurs initiales d'un processus stable mais mal centré.
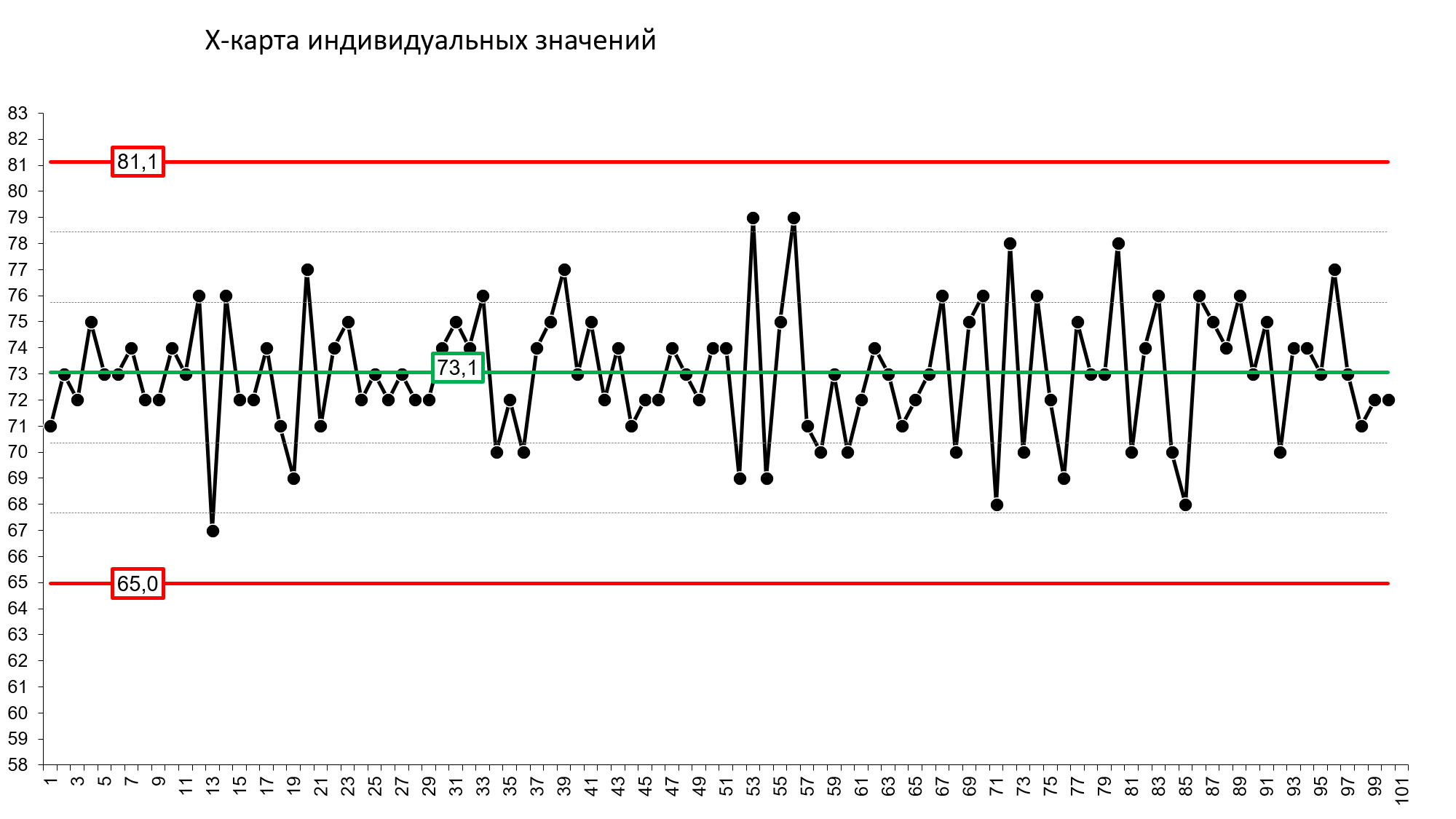
Figure 18. Carte X des valeurs individuelles (voix du processus) de 100 valeurs initiales d'un processus stable mais mal centré. Les lignes rouges sont respectivement les limites naturelles supérieure et inférieure du processus, la ligne verte est la ligne centrale (moyenne) du processus.
Dans ce cas, un seul réglage sera nécessaire pour centrer le procédé dans la plage de tolérance. Modifiez simplement le réglage de la machine une fois pour décaler le processus stable moyen du centre de la zone de tolérance.
Donc, si la moyenne d'un processus stable et mal centré est de 73,1, et que le centre du champ de tolérance est de 69. Le déplacement d'un processus stable et mal centré : 69,0-73,1 = -4,1
C'est par la quantité de déplacement qu'il faut modifier les réglages de la machine qui produit ces pièces. Et appelez le service technique qui devra installer la machine. Voir le résultat ci-dessous.
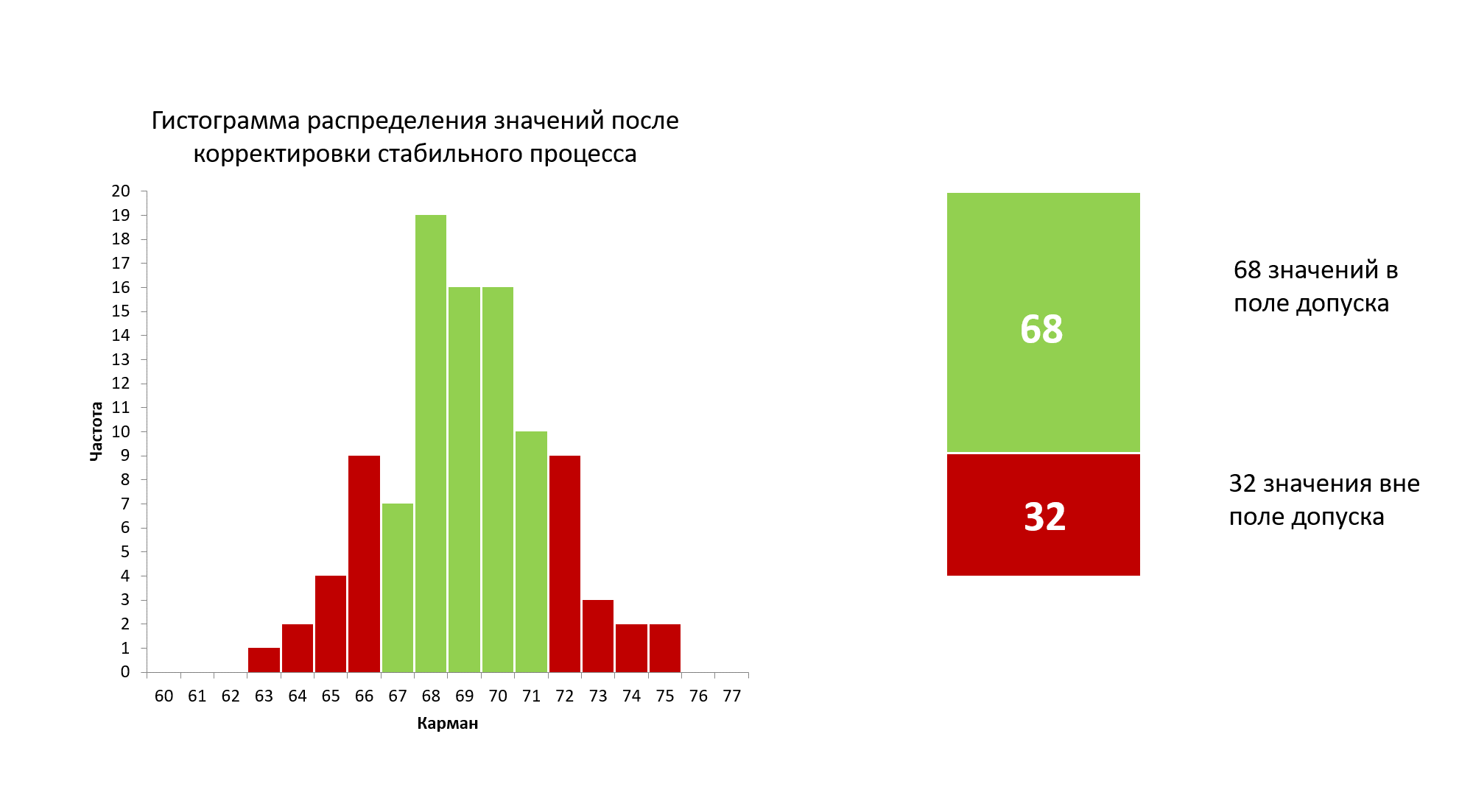
Figure 19 : Histogramme de la distribution de 100 nouvelles valeurs après centrage dans le champ de tolérance d'un procédé stable.
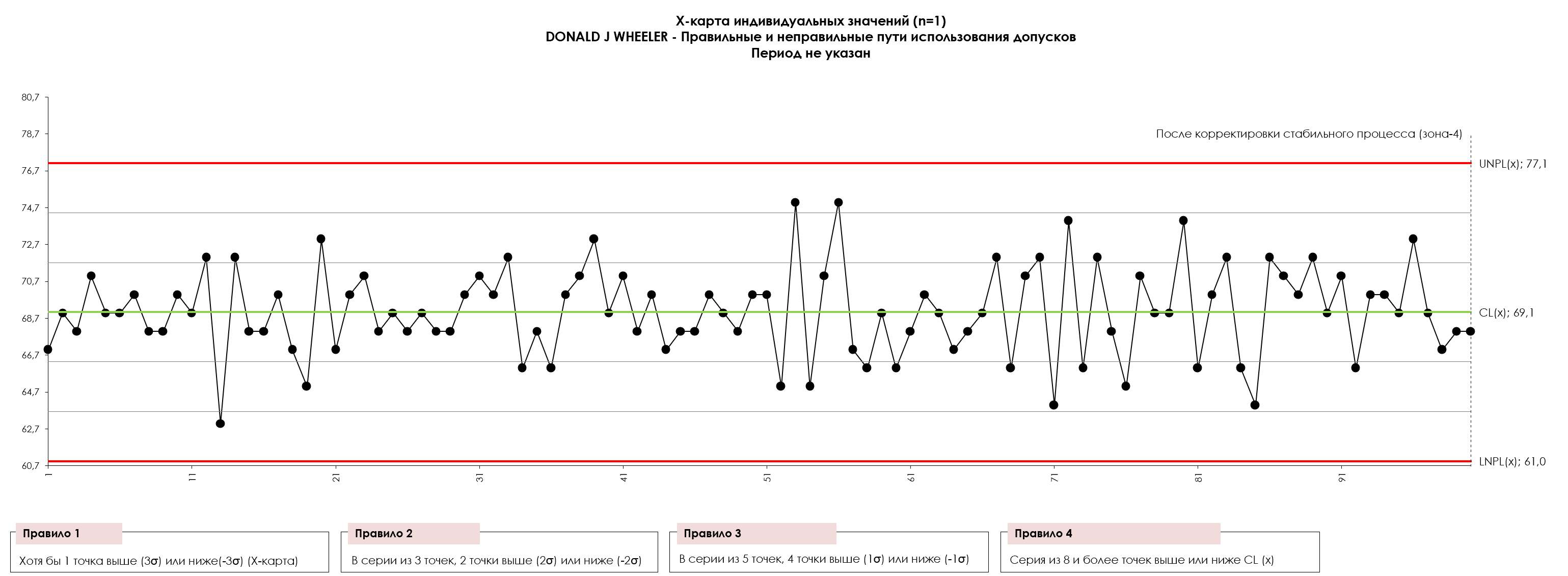
Figure 20. Carte X des valeurs individuelles (voix de processus) 100 nouvelles valeurs après centrage dans le champ de tolérance de processus stable. Les lignes rouges sont respectivement les limites naturelles supérieure et inférieure du processus, la ligne verte est la ligne centrale (moyenne) du processus. Le dessin a été préparé à l'aide de notre logiciel développé « Cartes de contrôle Shewhart PRO-Analyst +AI (pour Windows, Mac, Linux) » .
Si vous pensez que ce dernier cas est rare, vous vous trompez lourdement. Si vous ne conservez pas de cartes de contrôle de vos processus et ne construisez pas d'histogrammes de distribution des indicateurs par rapport aux champs de tolérance, vous ne pouvez même pas en juger. Si vous connaissez les indices de performance du processus (reproductibilité) Cp (indice d'espace de vie) et Cpk (indice de centrage du processus), alors sachez que Cpk dans la grande majorité des cas est inférieur à Cp, ce qui indique un décalage de la moyenne. processus du centre du champ de tolérance vers la limite de tolérance inférieure ou supérieure. Dans tous les cas, le centrage des processus stables et instables dans la zone de tolérance réduit la part des pièces de processus défectueuses qui dépassent les limites de tolérance en « un clic ». Dans les cas où le processus fonctionne dans la zone de tolérance, le centrage améliore considérablement la qualité des pièces et assemblages (DSE), rapprochant la plupart des pièces du centre de la zone de tolérance (pour les zones de tolérance symétriques). La dernière déclaration explique Fonction de perte Taguchi .
Améliorations des processus de 77 pièces défectueuses à 32 avec un seul ajustement.
« Comment trouves-tu ça, Elon Musk ? »
Important!
- La seule façon économiquement réalisable d’améliorer significativement la qualité est de commencer par amener le processus dans un état statistiquement contrôlé, et ensuite seulement de commencer à le centrer dans la zone de tolérance.
- Avant toute recherche de processus, assurez-vous que votre système de mesure , qui est utilisé par l'opérateur qui ajuste le processus technologique, est dans un état statistiquement contrôlé, ne présente pas de biais significatif, découvrez si sa précision est suffisante pour évaluer le processus, si les mesures uniformes sont adéquates (profondeur de mesure) ou, à l'inverse, si vous enregistrez du bruit. - Voir la description de notre logiciel Cartes de contrôle Shewhart .
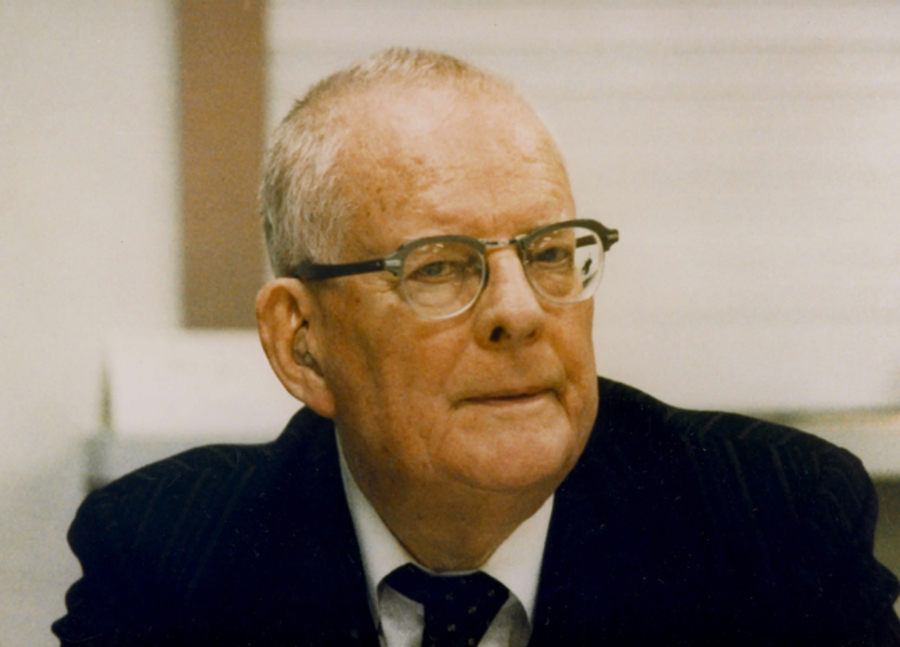
"Rien ne remplace la connaissance. Mais la perspective d'utiliser la connaissance est effrayante."