Lors de la conception en CAO, comptez-vous tester un modèle numérique construit à sa valeur nominale ? Attendez-vous alors à des problèmes d’assemblage des composants et de comportement du produit fini en conditions réelles
Matériel préparé par : Directeur scientifique du Centre AQT Sergueï P. Grigoriev
Le libre accès aux articles ne diminue en rien la valeur des matériaux qu'ils contiennent.
L'analyse de la variabilité des processus de production contribuera à réduire l'impact négatif variations inévitables sur la qualité dimensionnelle du produit, son coût et son délai de commercialisation.
Vous trouverez ci-dessous les preuves d’une sous-optimisation généralisée du modèle numérique lui-même, sans tenir compte des objectifs que le modèle numérique était censé servir.
Notre équipe a pris la parole lors d'une réunion dans une société russe de recherche et de production avec un rapport sur la nécessité de comprendre les capacités des processus de production réels en termes de variabilité des indicateurs de qualité clés dans la conception et la production de produits.
L'une des sections du rapport était consacrée aux problèmes de qualité des produits conçus sans comprendre l'état statistique et les capacités des processus de production réels, tant les nôtres que ceux des fournisseurs. En particulier, le concepteur général adjoint (ZGK) d'une des entreprises de cette société a indiqué que la construction d'un nouveau centre de données (centre de stockage et de traitement des données) réduirait les tests à grande échelle.
Notre attitude face à la déclaration ZGK : Tant que vous ne connaissez pas les possibilités des processus réels, nous vous recommandons de vous méfier de telles déclarations. Même un prototype à grande échelle (prototype) n'est pas un produit en série.
"Tests inadéquats des prototypes.
Le prototype est unique, ses paramètres sont artificiellement proches des paramètres nominaux. Sans connaissance des variations, la variabilité ne peut être prédite. »
Lorsque vous envisagez de remplacer les tests à grande échelle par des tests sur modèles numériques, vous devez comprendre ce que vous êtes prêt à négliger et dans quelle mesure. En termes simples, vous devez comprendre à quel point les résultats des tests d'un modèle numérique seront différents des tests à grande échelle de modèles expérimentaux, et plus encore de ceux de produits en série. En supposant l'insignifiance de l'influence des facteurs que vous êtes prêt à ignorer, vous devez comprendre que la résultante de ceux-ci et des facteurs non pris en compte (ignorés, indifférenciés et/ou numériquement non mesurables), compte tenu de leur variabilité inhérente, peut considérablement, de la du point de vue de la finalité des tests, dépassez vos hypothèses. Pensez-vous que ce n'est pas vrai ? Comment sais-tu cela? De quelles données disposez-vous pour tirer de telles conclusions ?
Laissez-moi vous donner un exemple mondialement connu.
Pendant la Seconde Guerre mondiale, le commandement des forces aériennes américaines et britanniques a chargé Abraham Wald, qui travaillait dans le programme secret du Statistical Research Group (SRG) des États-Unis, de déterminer quelles parties du fuselage de l'avion devaient être protégées par des moyens supplémentaires. armure. L'armée a proposé d'installer une protection supplémentaire sur les parties de l'avion qui ont le plus souffert lors des combats aériens. Wald a étudié les avions revenant de missions de combat, notant les emplacements des impacts. En conséquence, il a recommandé d'installer une protection supplémentaire dans les zones (parties centrale et arrière du fuselage) où le nombre de trous, au contraire, était minime. La recommandation était basée sur la conclusion qu'il était nécessaire de se protéger contre les coups que Wald n'avait pas vus - les avions qui les recevaient ne revenaient tout simplement pas. Par la suite, les décisions prises sur la base de l’analyse de données connues uniquement ont été appelées « biais de survie ».
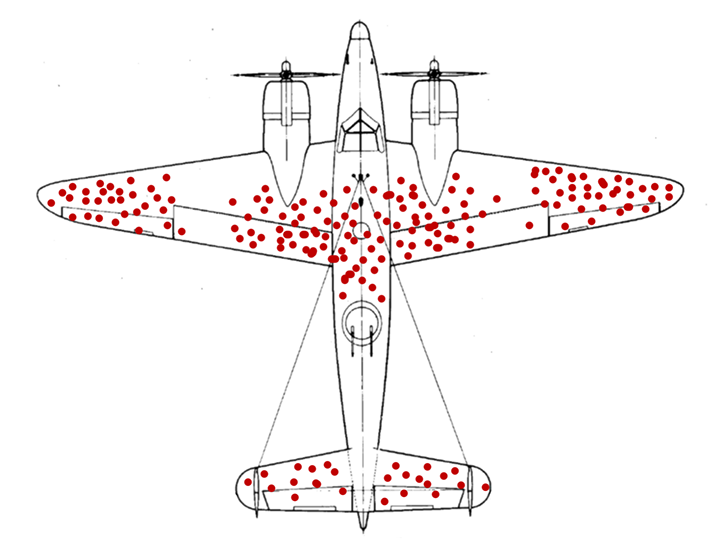
Figure 1. Abraham Wald. Biais de survie. Un avion avec des points rouges représentant les statistiques d'impacts de balles sur les avions américains de retour.
Si vous envisagez de comparer ultérieurement les résultats du modèle numérique avec des tests de prototypes réels, combien de prototypes comptez-vous produire et tester pour cela : 1 ; 5 ; 8 ; 25 ? Ces prototypes seront-ils les mêmes ? Comment sais-tu cela? Pour revendiquer l'homogénéité des prototypes, vous devez avoir la preuve de la contrôlabilité statistique de vos propres processus de fabrication et des processus de fabrication des fournisseurs impliqués dans la production des prototypes. Pouvez-vous démontrer les cartes de contrôle de Shewhart de ces processus pour tous les paramètres clés ?
Explication de notre déclaration
La conception dans des systèmes de conception assistée par ordinateur (CAO) réalisée en termes nominaux, un modèle numérique, n'est pas ce qui se produira dans le matériel. Les concepteurs doivent utiliser des données sur la variabilité inhérente des processus de fabrication réels pour décider des modifications nécessaires dans la conception, les matériaux, la technologie et les tolérances, ou pour exiger des services de fabrication et des fournisseurs qu'ils améliorent les processus et la technologie avant le début de la production du prototype réel.
Nous avons soigneusement étudié la publication d'entreprise ouverte d'une entreprise manufacturière clé de cette société. Dans la publication, les employés de l'entreprise ont rapporté de manière suffisamment détaillée les problèmes qu'ils rencontrent en production.
En particulier, l'ingénieur des procédés de l'atelier d'assemblage a rapporté :
« Le technologue doit rechercher la solution optimale à un problème qui survient lors du processus d'assemblage, il est donc obligé de réagir rapidement à la situation actuelle. Considérant que plusieurs situations d'urgence peuvent survenir, il doit se précipiter et suivre tout. C’est le rythme de travail normal d’un ingénieur de procédés dans l’atelier d’assemblage.
Ce technologue est tellement habitué à l'apparition constante de situations d'urgence lors de l'assemblage de produits qu'il reconnaît lui-même cela comme normal. Confirmant ainsi la persistance (stabilité) des problèmes lors du montage. Et la stabilité est le signe de problèmes systémiques. La gestion des problèmes systémiques relève de la responsabilité de la direction et non du technologue.
Le forgeron a dit ce qui suit :
«Lorsqu'un forgeron chauffe une pièce dans une forge, il détermine visuellement la température et sent que le métal est prêt à être forgé. Lorsqu'il est chauffé, le carbone et d'autres éléments d'alliage en brûlent, il est donc important de ne pas surchauffer. Par exemple, les débutants obtiennent la forme souhaitée du métal en quatre chauffages ; un forgeron expérimenté n'en a besoin que de deux".
Les designers ont-ils pris en compte cette incertitude du processus de production ? Quelqu'un sait quel type d'alliage est obtenu après une quantité indéfinie de chauffage à une température déterminée « à l'œil nu » par différents forgerons dans différentes conditions ? Dans ce cas, les calculs automatisés de résistance d’un modèle numérique permettront-ils de prédire les propriétés mécaniques et, par exemple, la résistance à la corrosion de produits réels ?!
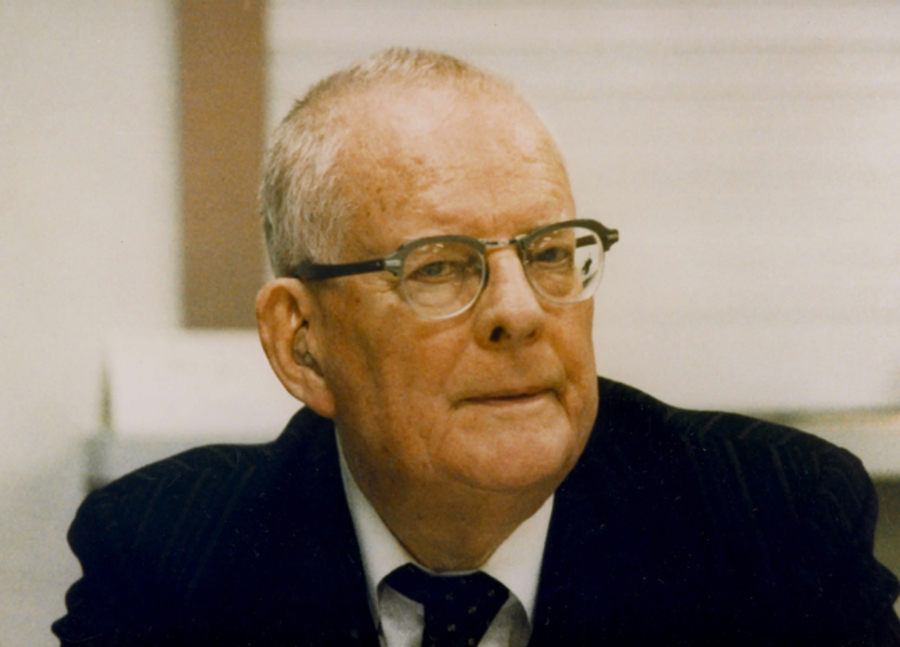
"La pratique est plus précise que la science pure ; plus précise que la formation. Selon Shewhart, les normes de connaissances et de compétences requises dans les industries manufacturières et de services sont plus strictes que celles de la science pure."
La citation d’Edwards Deming ci-dessus explique en partie la situation actuelle dans laquelle la science russe résiste avec confiance à la concurrence au niveau international, tandis que l’industrie russe est perdante dans de nombreux domaines.
Nous avons donné d’autres exemples démontrant le manque de compréhension de la direction de l’entreprise quant à sa responsabilité en matière de qualité, que je ne publie pas dans cet article.
J'espère qu'il devient désormais plus clair à quel point un modèle numérique, construit à partir de pièces avec des tolérances nominales et des alliages répondant aux exigences définies lors de la conception, peut différer d'un prototype réel. Si nous parlons de produits en série, ces différences seront encore plus grandes. Compte tenu de l'existence de barrières entre les services impliqués dans la conception, la production, l'approvisionnement et la collaboration avec les fournisseurs, le refus de tester à grande échelle des produits comportant des centaines, voire des milliers de pièces, entraînera d'énormes pertes, dont les véritables raisons ne seront jamais reconnues par la gestion de cette société.
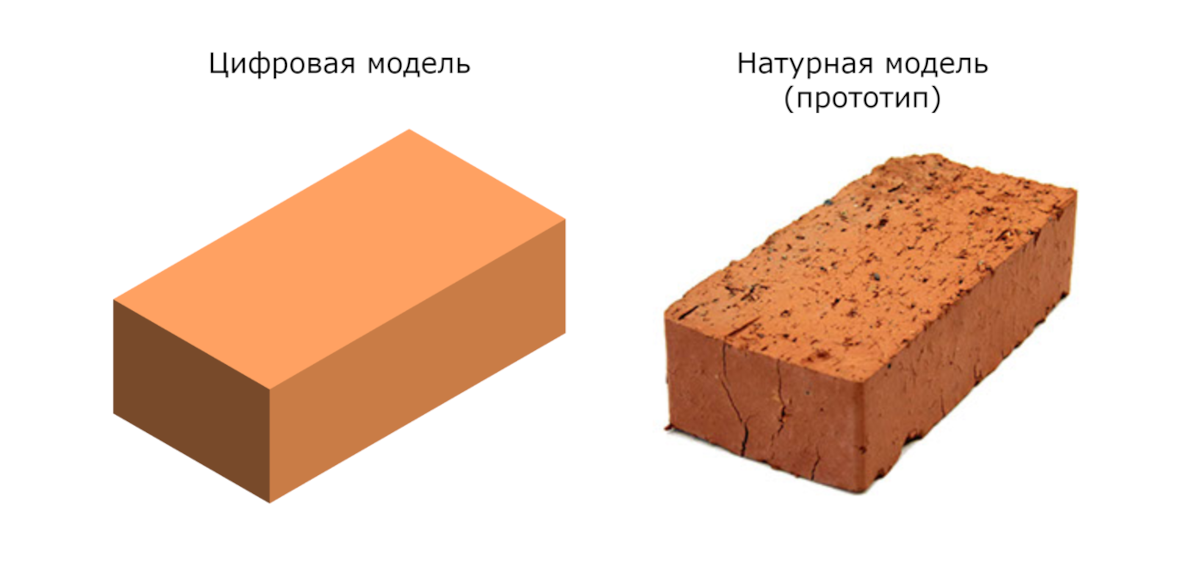
Figure 2. Modèle numérique versus modèle naturel.
Ensuite, nous avons invité les personnes présentes à la réunion à envisager des options pour l'appariement bidimensionnel le plus simple des champs de tolérance de l'arbre et du trou dans l'ajustement avec jeu. La variabilité des dimensions géométriques des pièces réelles est ce qui distingue le moins un modèle numérique d'un modèle grandeur nature.
Vous trouverez ci-dessous un affichage conditionnel de l'appariement des champs de tolérance de l'arbre et du trou. Les concepteurs créeront des pièces en CAO au pair. Dans le meilleur des cas (dans les entreprises russes les plus avancées), le modèle numérique sera vérifié pour la combinaison des champs de tolérance des pièces en interaction et le respect du champ de tolérance dépendant obtenu à la suite de leur interaction.
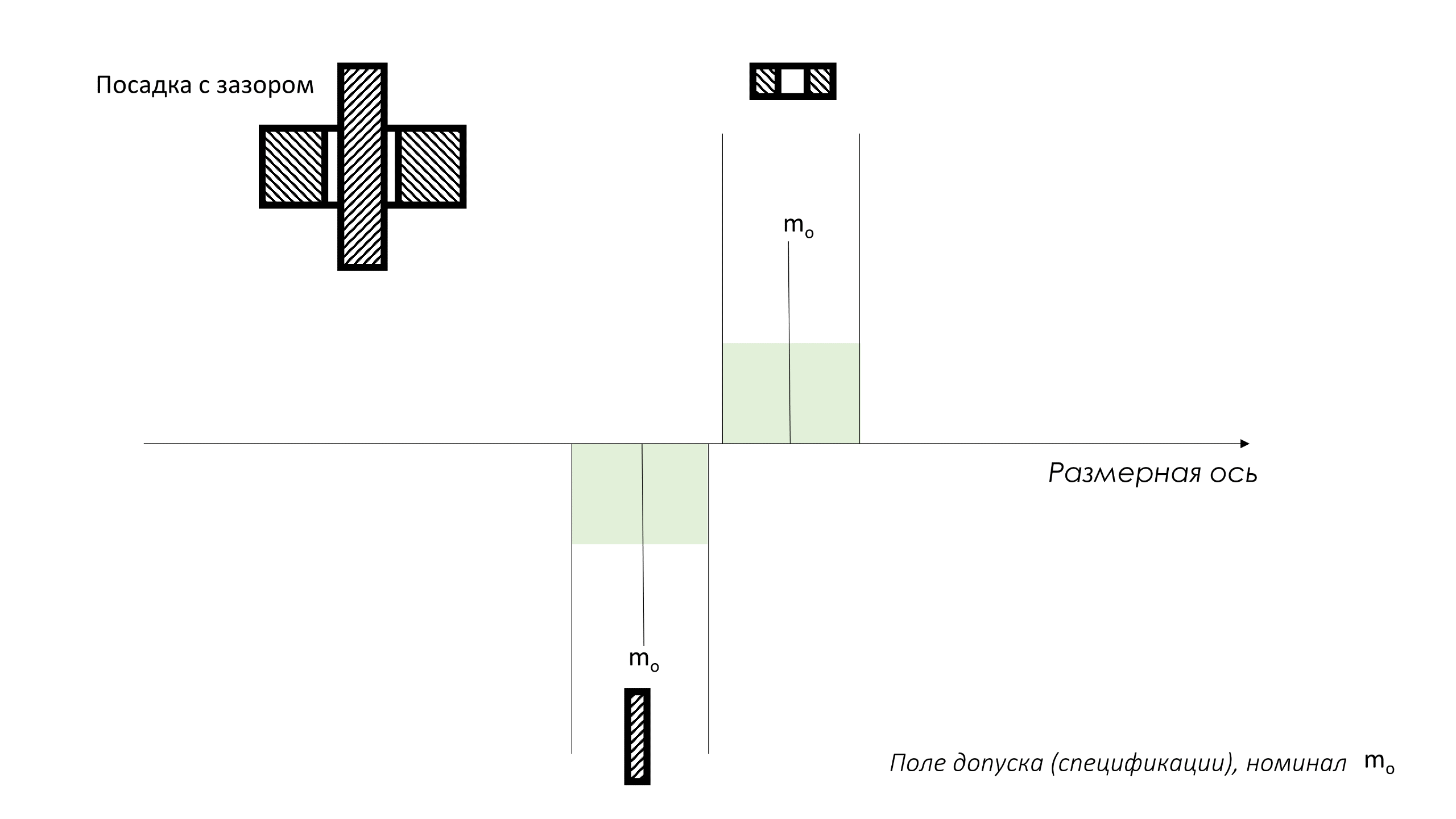
Figure 3. Affichage conditionnel de l'appariement des champs de tolérance de l'arbre et du trou (ajustement avec jeu).
Les procédés de fabrication idéaux qui produiront les pièces, dans ce cas, doivent correspondre aux densités de répartition des mesures individuelles (des courbes symétriques en cloche sont choisies arbitrairement), comme présenté dans la figure 4 ci-dessous : stables, parfaitement centrées et avec une répartition de valeurs individuelles dans la zone de tolérance avec un peu d'espace libre. Dans ce cas, on sait d’avance que toutes les pièces seront adaptées à 100 %. Il suffira d'effectuer un rare échantillonnage de pièces à contrôler pour confirmer l'état stable des procédés et contrôler l'ajustement de la moyenne (ligne centrale) de la répartition de ces procédés au champ de tolérance nominal.
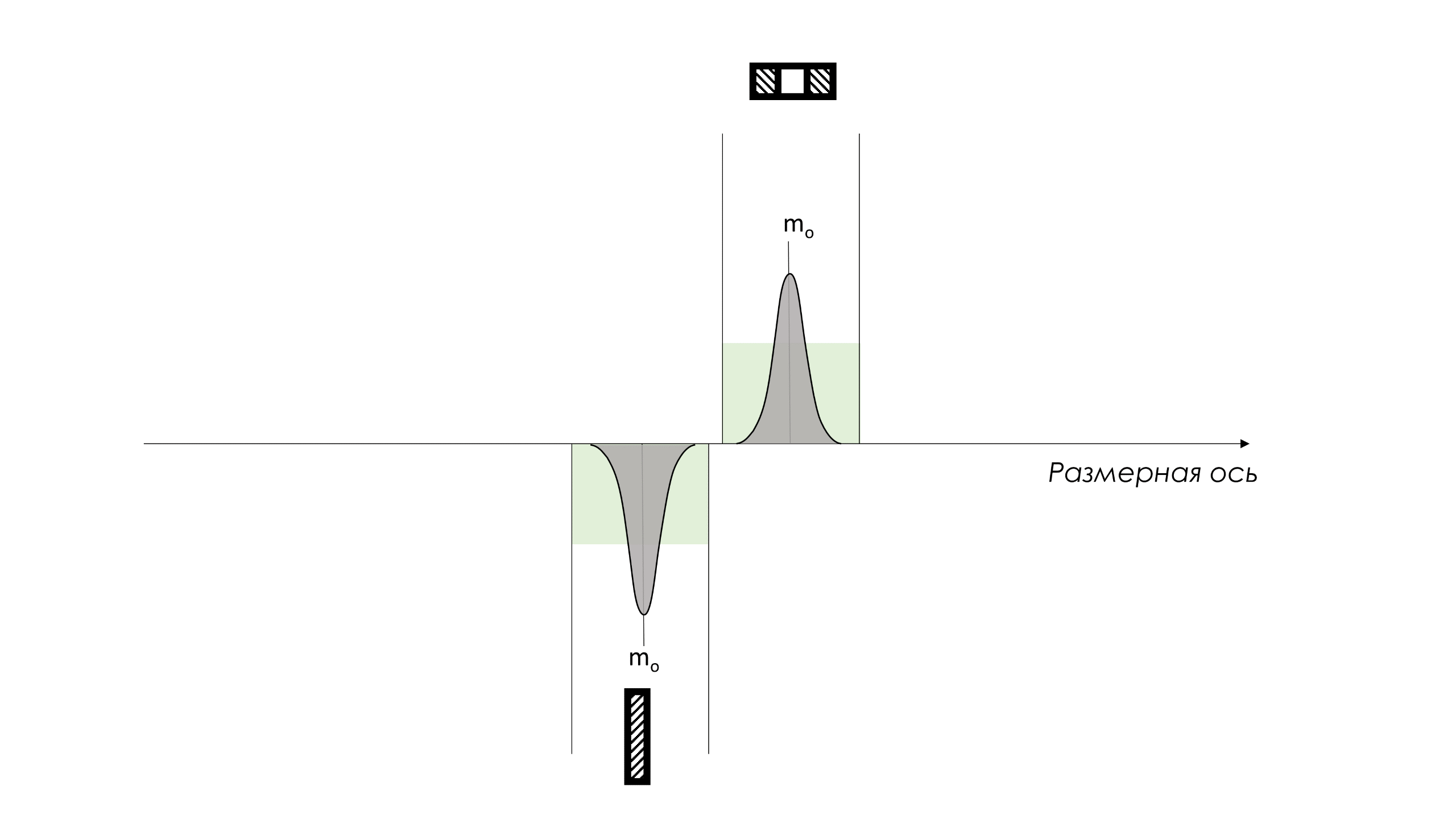
Figure 4. Processus de production stables et parfaitement centrés, avec des valeurs individuelles réparties dans une zone de tolérance avec un certain espace libre.
Considérons maintenant l'option de la figure ci-dessous, lorsque les processus de production sont dans un état statistiquement contrôlé (stable), leur écart 6σ est inférieur à la largeur du champ de tolérance (par exemple, Cp≥1,33), mais ils ne sont pas centrés. Ensuite, certains produits seront en dehors de la plage de tolérance et défectueux. Il n’y aura pas un seul détail à sa valeur nominale. Il faudra diviser toutes les pièces produites entre celles qui respectent la zone de tolérance et celles qui ne le font pas, en effectuant un contrôle à 100 %, ce qui est coûteux et inefficace. Dans ce cas, on sait d’avance que près de la moitié des pièces ne respecteront pas la plage de tolérance. Voir description des formules calcul des indices de reproductibilité Cp et Cpk .
Formule de calcul de l'indice de reproductibilité : Cp = plage de tolérance / 6σ
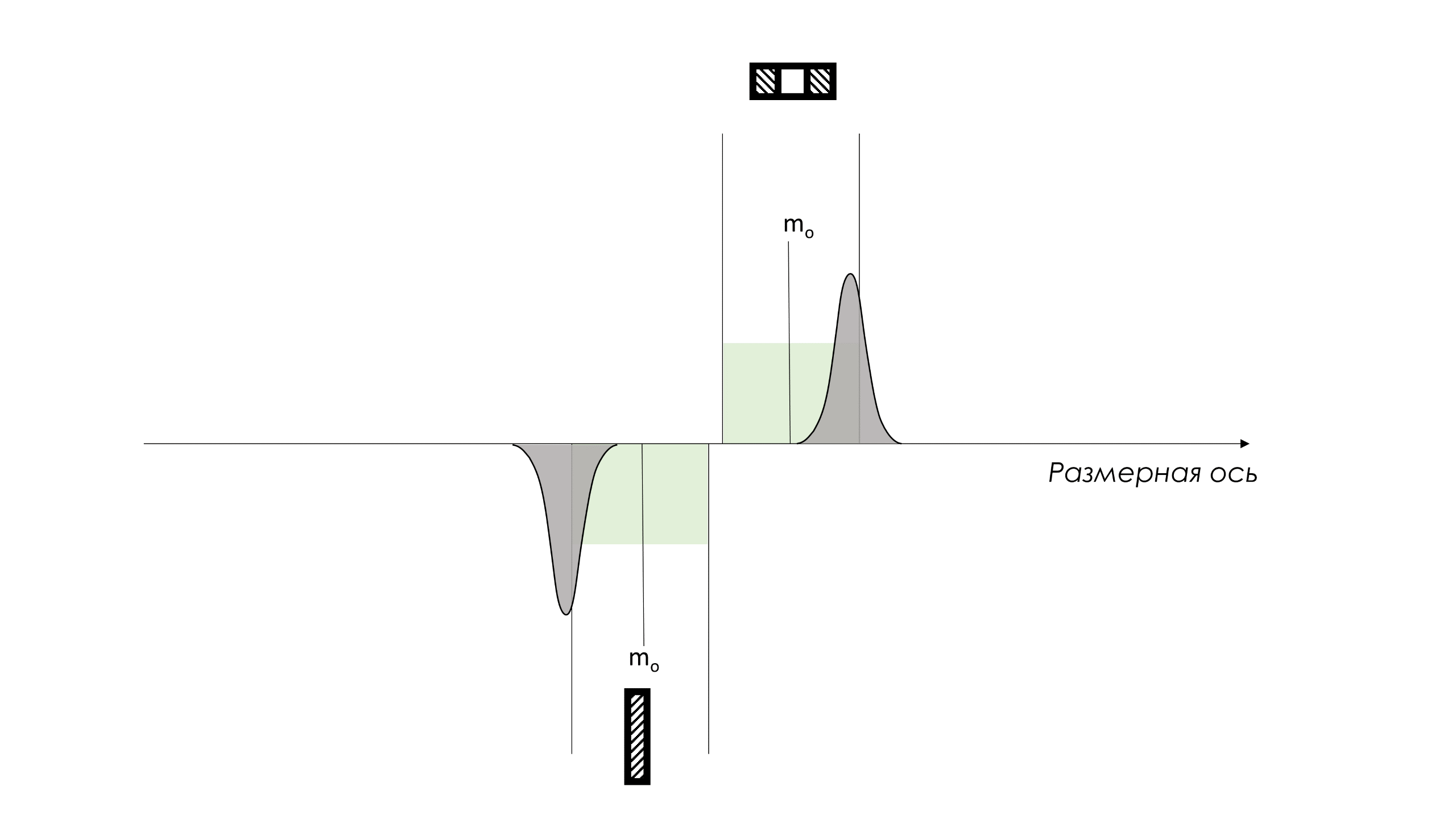
Figure 5. Les processus de production sont dans un état statistiquement contrôlé (stable), leur écart 6σ est inférieur à la largeur du champ de tolérance (par exemple, Cp≥1,33), mais ils ne sont pas centrés.
Considérons ensuite l'option (voir Figure 6 ci-dessous) lorsque les processus de production sont dans un état statistiquement contrôlé, que leur écart 6σ est supérieur à la largeur du champ de tolérance (par exemple, Cp<1,00) et qu'ils sont parfaitement centrés (par exemple , Cpk≈Cp). Là encore, une partie des produits fabriqués se trouveront en dehors de la plage de tolérance. Toutes les pièces produites devront être divisées entre celles qui respectent la zone de tolérance et celles qui ne le sont pas, en effectuant un contrôle à 100 %. Dans ce cas, on sait d’avance que certaines pièces ne respecteront pas la tolérance.
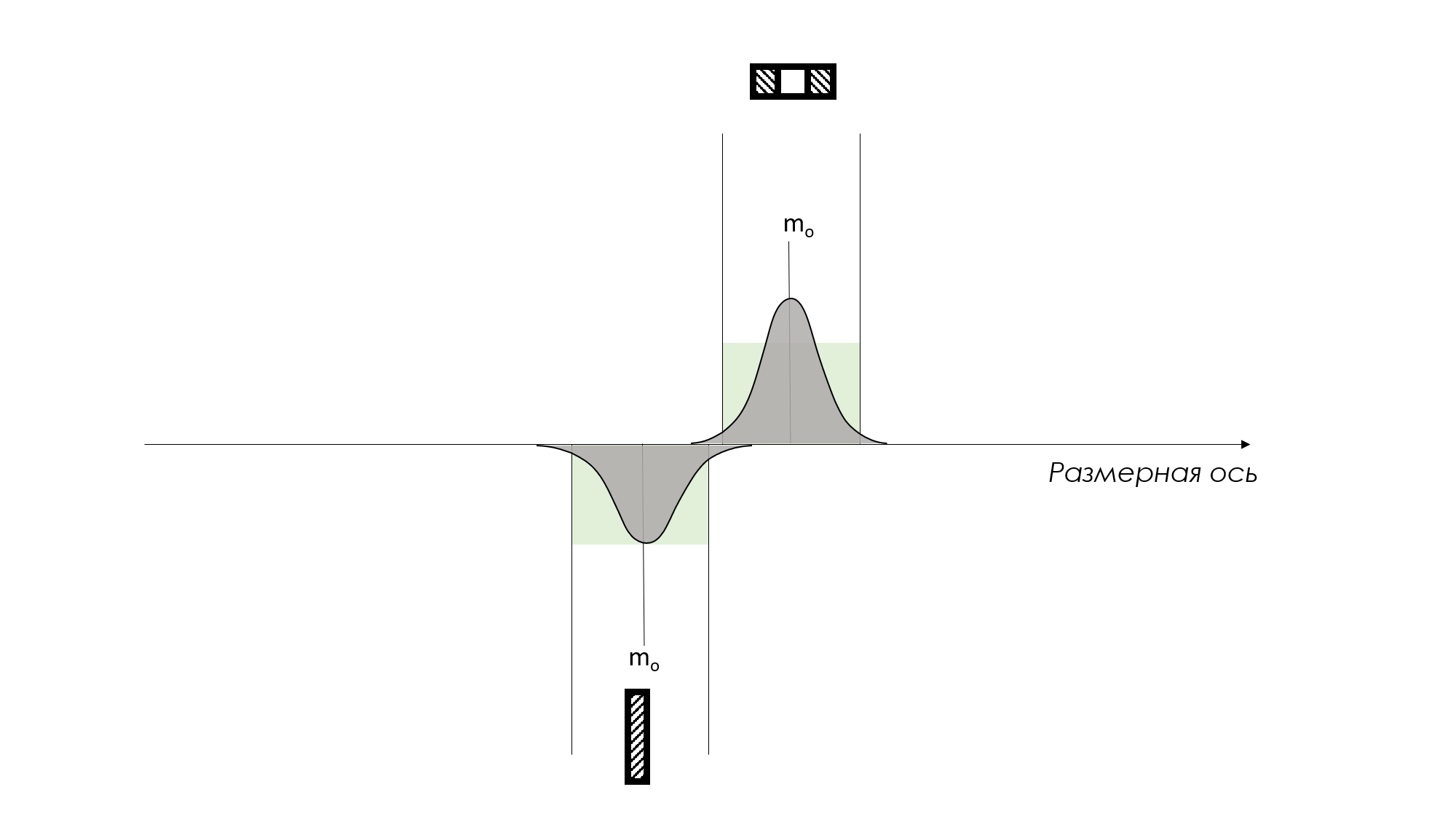
Figure 6. Les procédés de fabrication sont dans un état statistiquement contrôlé (stable), leur étalement 6σ est supérieur à la largeur du champ de tolérance (par exemple, Cp<1,00) et ils sont parfaitement centrés (par exemple, Cpk≈Cp).
Considérons ensuite l'option (voir Figure 7 ci-dessous) lorsque les processus de production sont dans un état statistiquement contrôlé, que leur écart 6σ est supérieur à la largeur du champ de tolérance (par exemple, Cp<1,00) et qu'ils ne sont pas centrés (Cpk< Cp). Un nombre encore plus grand de produits se trouveront alors en dehors de la plage de tolérance. Les conséquences sont évidentes. Toutes les pièces produites devront être divisées entre celles qui respectent la zone de tolérance et celles qui ne le sont pas, en effectuant un contrôle à 100 %. Dans ce cas, on sait d’avance que plus de la moitié des pièces seront inappropriées.
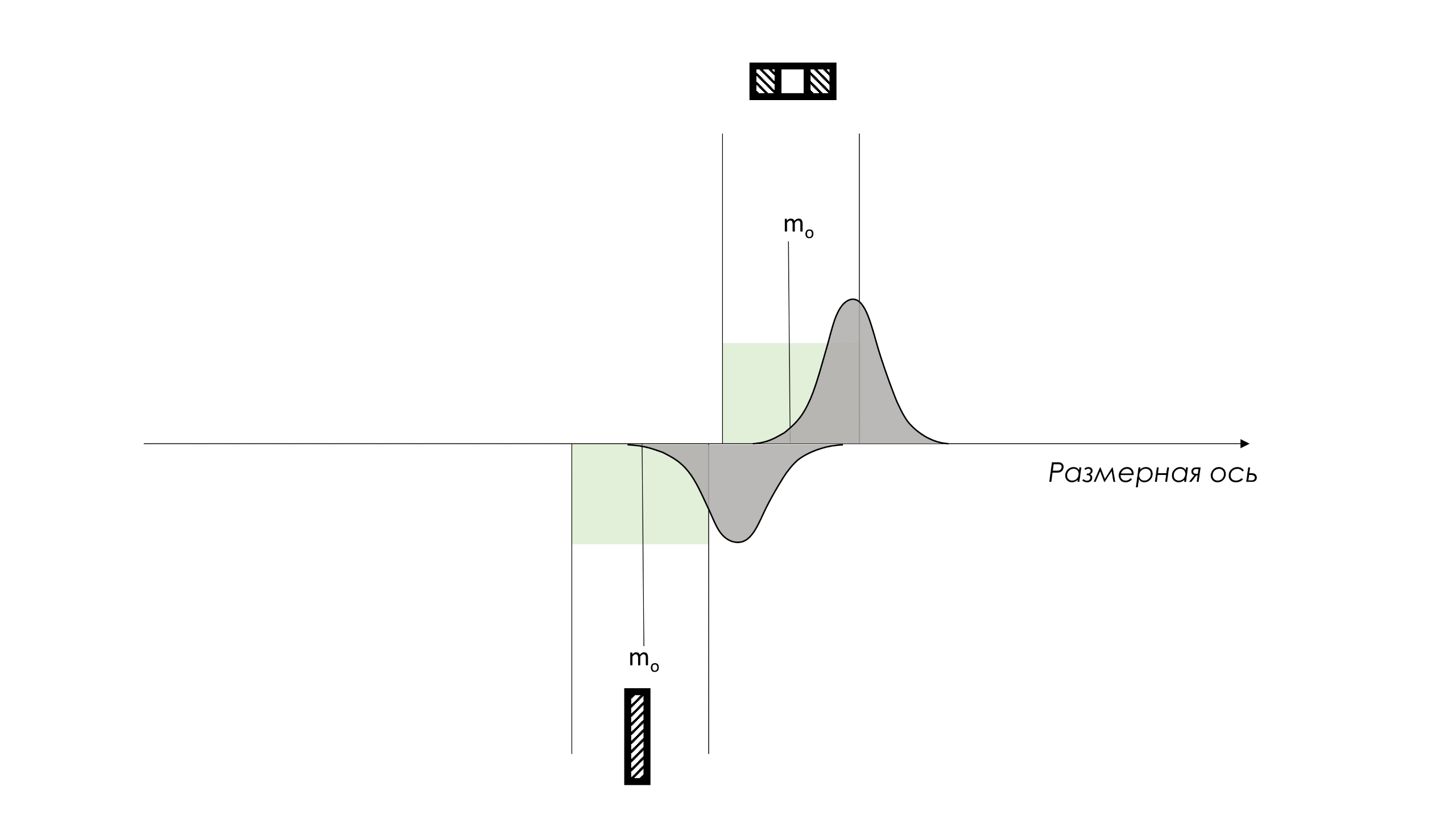
Figure 7. Les processus de production sont dans un état statistiquement contrôlé (stable), leur étalement 6σ est supérieur à la largeur du champ de tolérance (par exemple, Cp<1,00) et ils ne sont pas centrés (Cpk<Cp).
La figure 8 ci-dessous est une autre option qui correspond à la condition décrite pour la figure 7 ci-dessus. Là encore, les conséquences sont évidentes. Toutes les pièces produites devront être divisées entre celles qui respectent la zone de tolérance et celles qui ne le sont pas, en effectuant un contrôle à 100 %. Dans ce cas, on sait d’avance que plus de la moitié des pièces seront inappropriées.
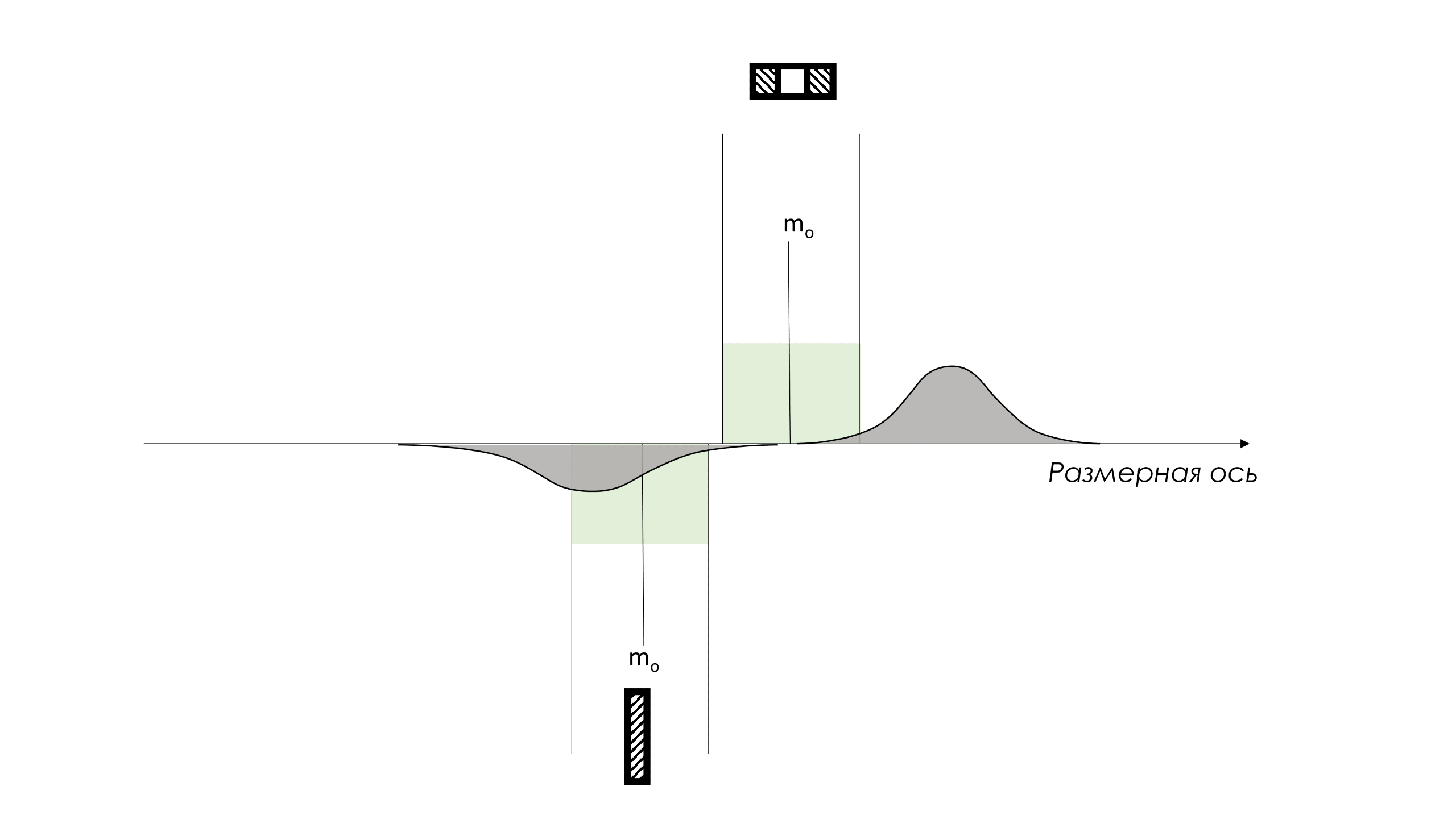
Figure 8. Un cas particulier de l'option de la Figure 7. Les processus de production sont dans un état statistiquement contrôlé (stable), leur écart 6σ est supérieur à la largeur du champ de tolérance (par exemple, Cp<1,00), et ils ne sont pas centré (Cpk<Cp).
La figure ci-dessous montre une autre option, lorsque les processus de production réels sont dans un état statistiquement incontrôlable (imprévisible). Leur écart 6σ se rétrécit puis s'étend de manière imprévisible, leur moyenne change également de manière imprévisible sa position par rapport au champ de tolérance nominal. Toutes les pièces produites devront être divisées entre celles qui respectent la zone de tolérance et celles qui ne le sont pas, en effectuant un contrôle à 100 %. Personne ne sait à l’avance combien de détails seront incohérents, peut-être à 100 %. Personne ne peut prédire le comportement de processus statistiquement incontrôlables. Les pertes totales totales de l'entreprise dues à l'imprévisibilité des processus de production sont maximales ! Les pièces produites par de tels procédés ne sont pas uniformes.
Le modèle numérique est peut-être idéal, mais les pertes de l'entreprise dans son ensemble peuvent être maximales.
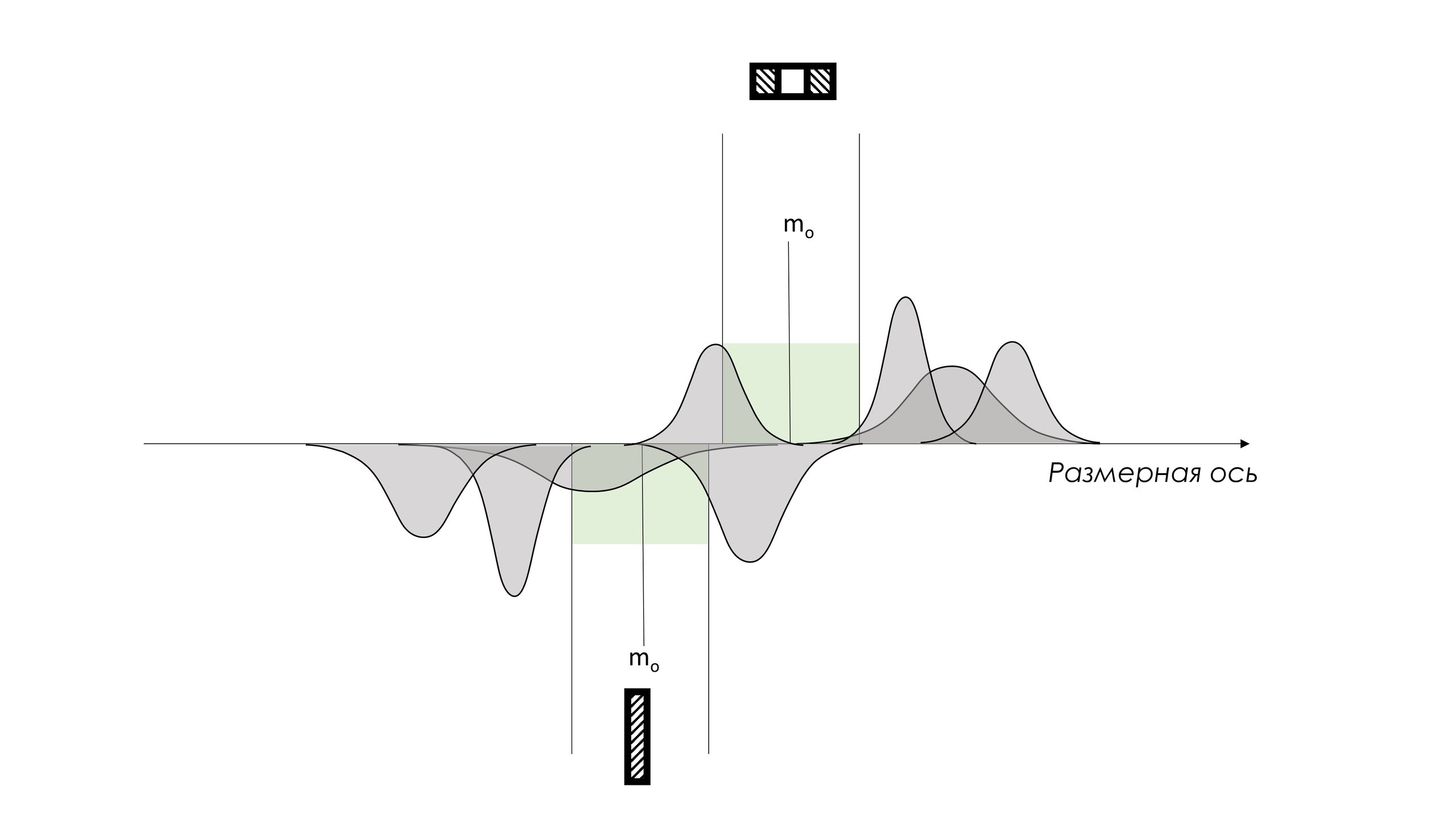
Figure 9. Les processus de production sont dans un état statistiquement incontrôlable (imprévisible). Leur écart 6σ se rétrécit ou s'étend de manière imprévisible, leur moyenne change également de manière imprévisible sa position par rapport au champ de tolérance nominal.
Des points supplémentaires et importants à cet égard sont l'exigence obligatoire de stabilité du système de mesure, l'analyse du biais du système de mesure, la prise en compte de l'erreur du système de mesure dans des spécifications de production plus strictes. Ce dernier est abordé dans notre article : Le produit conforme aux spécifications est-il réellement conforme ? .
Enfin, nous sommes arrivés au problème lié à la sous-optimisation sur un modèle numérique au lieu de la nécessité d'optimiser les activités de toutes les divisions de l'entreprise, en tant que système dans son ensemble, selon ses objectifs, par exemple, la production de produits fiables. moteurs de série avec un coût de possession minimum pour les opérateurs.
"La sous-optimisation est plus facile à réaliser que l'optimisation. Cependant, la sous-optimisation n'est pas bon marché. La sous-optimisation peut créer l'illusion d'une amélioration, mais en réalité elle crée des obstacles qui empêchent de réels progrès. De plus, la sous-optimisation d'une partie est souvent nuit à d’autres parties, de sorte que le changement global cause davantage de dommages. » "Ce n'est pas bénéfique. Cela rend également plus difficile la réalisation de changements véritablement rentables."
D'autres conversations ont montré que ni la direction de la production ni les concepteurs de cette société ne savaient comment fonctionnaient réellement leurs processus de production. Mais les cartes de contrôle Shewhart ne sont toujours pas utilisées pour évaluer l’état et améliorer les processus.
Dans une telle situation, les ingénieurs de conception doivent se contenter des champs de tolérance et des propriétés théoriques, encore une fois, des matériaux nominaux, et le personnel de production, sans l'aide de la direction et sans comprendre la nature de la variabilité, effectue erreurs du premier et du deuxième type dans le but de produire des pièces présentant les caractéristiques requises et d'assembler le produit fini.
Des KPI distincts pour différents départements de l’entreprise ne font qu’empirer les choses.
Que se passe-t-il dans votre entreprise ?
Edwards Deming préparé questions pour aider la direction , En voici quelques uns:
- Vos processus de production sont-ils stables ?
- Comment sais-tu cela?
- De quelles données disposez-vous ?
- Que faites-vous pour combler le fossé entre la conception du produit, la production réelle et la livraison ?
Si vous n'avez pas de réponses claires aux questions ci-dessus, comment pouvez-vous vous appuyer sur un processus d'assemblage numérique et remplacer les tests sur le terrain par des tests de votre modèle numérique ?!
"Nous avons déploré le gaspillage de matériaux, d'efforts humains et de temps machine. Le gaspillage de connaissances lorsqu'une entreprise est incapable d'utiliser et de développer son potentiel existant est encore plus déplorable."
Nous constatons de nombreuses preuves de sous-optimisation dans les modèles numériques eux-mêmes, sans prendre en compte les objectifs globaux du système que les modèles numériques étaient censés servir. Tout cela dans un souci de sous-optimisation de la fameuse productivité du développement et de réduction des coûts souvent irréfléchie, sans prêter attention aux processus de production.
« Les résultats ne peuvent être considérés sans tenir compte des objectifs pour lesquels ils ont été créés. »
Dans un environnement où l’efficacité des développeurs de produits est considérée en termes de réduction du temps et des coûts de développement, remplacer les tests de produits réels par des tests virtuels est une erreur qui peut s’avérer très coûteuse pour l’entreprise dans son ensemble. Tout cela n’est qu’une tentative de prendre des raccourcis. L'analyse des données du processus de production et du service après-vente à l'aide des cartes de contrôle Shewhart montrera comment l'optimisation du processus de conception les a affectés.
"Cependant, une analyse systématique des performances de production est nécessaire pour déterminer si les étapes d'amélioration permettent d'atteindre l'objectif et si elles sont appropriées."
L’outil le meilleur et le plus simple pour analyser l’efficacité des mesures d’amélioration prises est les cartes de contrôle Shewhart.
L'extrait suivant est tiré de l'ouvrage de Marvin Mandel intitulé Measurement and Enhancing the Productivity of Service and Government Organizations - Aoyama Dai-ichi Mansions, 4-14 Akasaka 8-chome, Minatoku, Tokyo 107, 1975. – pp. 3–4) qui met en lumière ce point. problème:
« Les résultats... ne peuvent être pris en compte sans prendre en compte les objectifs pour lesquels les systèmes ont été créés.
Pour créer un peu de contexte, analysons quelques exemples. On raconte que Thomas Edison, le grand inventeur américain, aurait proposé une machine à voter pour améliorer cette procédure au Congrès des États-Unis. Il a fait la démonstration de son appareil au président du Parlement et au président du Sénat. Selon l'idée de l'inventeur, chaque membre du Congrès et sénateur aurait trois boutons sur sa chaise : rouge pour dire « non », vert pour « oui » et blanc pour « s'abstenir ».
Edison a suggéré qu'au début du vote, les participants appuyaient sur le bouton correspondant, après quoi un rapport apparaîtrait instantanément sur la façon dont chaque personne a voté et quels ont été les résultats globaux. Edison a fièrement assuré au Président et Président du Sénat que son appareil éliminerait les erreurs qui se produisent dans la méthode de vote par appel nominal séquentiel, réduirait considérablement le temps de vote et offrirait d'autres avantages.
Il a été complètement choqué lorsque le Président de la Chambre des Représentants et le Président du Sénat l'ont interrompu au milieu d'une phrase et ont déclaré qu'un tel système était totalement indésirable et qu'au lieu d'améliorer le travail de la Chambre ou du Sénat, il perturberait complètement le fonctionnement de la Chambre des Représentants et du Sénat. bon fonctionnement du Congrès des États-Unis. Ce qui constituait une amélioration du point de vue d'Edison était au contraire une détérioration du point de vue du Congrès. La durée du processus d'appel nominal faisait partie intégrante du processus délibératif par lequel le Congrès décidait quoi faire.
La proposition d'Edison – un vote rapide – était incompatible avec les objectifs du Congrès. »
Ce qu'il faut faire?
Tout d’abord, vous devrez changer votre style de management et vous débarrasser des maladies mortelles et obstacles à la transformation .
Lors de la conception de produits, allez au-delà de l’utilisation de tables de tolérance pour prendre en compte les capacités de processus réelles avec une variabilité inhérente à la géométrie, aux propriétés des matériaux et à d’autres caractéristiques.
Veuillez noter que les spécifications de production (tolérances) doivent prendre en compte l'erreur de vos systèmes de mesure, avec une probabilité d'au moins 96 % que votre contrôle ne manque pas de produits défectueux, c'est-à-dire être plus étroites que la tolérance du client pour deux erreurs probables du système de mesure sur chaque côté de l'accès client sur le terrain. Les systèmes de mesure eux-mêmes doivent être stables ! Voir cet article pour une explication : Le produit conforme aux spécifications est-il réellement conforme ?
Pilotez les modifications de conception, les changements de tolérance ou demandez aux départements de fabrication et aux fournisseurs d'améliorer les processus si nécessaire à l'aide des cartes de contrôle Shewhart sous la direction d'un instructeur expérimenté. Et ne vous contentez pas de réponses vides de sens, exigez une confirmation statistique des caractéristiques de qualité sous la forme de cartes de contrôle des caractéristiques clés des produits et des processus.
J'ai démontré des recommandations pour améliorer les processus de production dans la courte vidéo ci-dessous.
Vidéo 1. Feuille de route pour l'amélioration des processus. Symboles des éléments dans la vidéo :. НГД et IOP - limites de tolérance inférieure et supérieure, respectivement (Eng, LSL et USL) ; m0 - champ de tolérance nominal ; LGP et ВГП - limites inférieures et supérieures du processus (anglais LCL et UCL) ; CL - ligne centrale du processus (moyenne).
Une assistance sérieuse dans l'échange d'informations et l'établissement d'un travail d'équipe entre les services de conception, de production, d'achat et de vente peut être fournie par des outils de gestion de la qualité d'un nouveau logiciel de système de gestion de la qualité (logiciel QMS), même selon les normes mondiales. avec les modules R&D SPC QM, en utilisant des données sur la variabilité des caractéristiques de qualité clés de leurs propres processus de production et des processus de leurs fournisseurs à l'aide des cartes de contrôle Shewhart.
Nous proposons l'intégration de toute la puissance de nos logiciel aux applications d'entreprise russes : CAD (CAD)- , PLM- , ERP , MES- , Systèmes LIMS , la formation et l'apport d'un soutien scientifique et pratique continu et efficace aux salariés de l'entreprise.
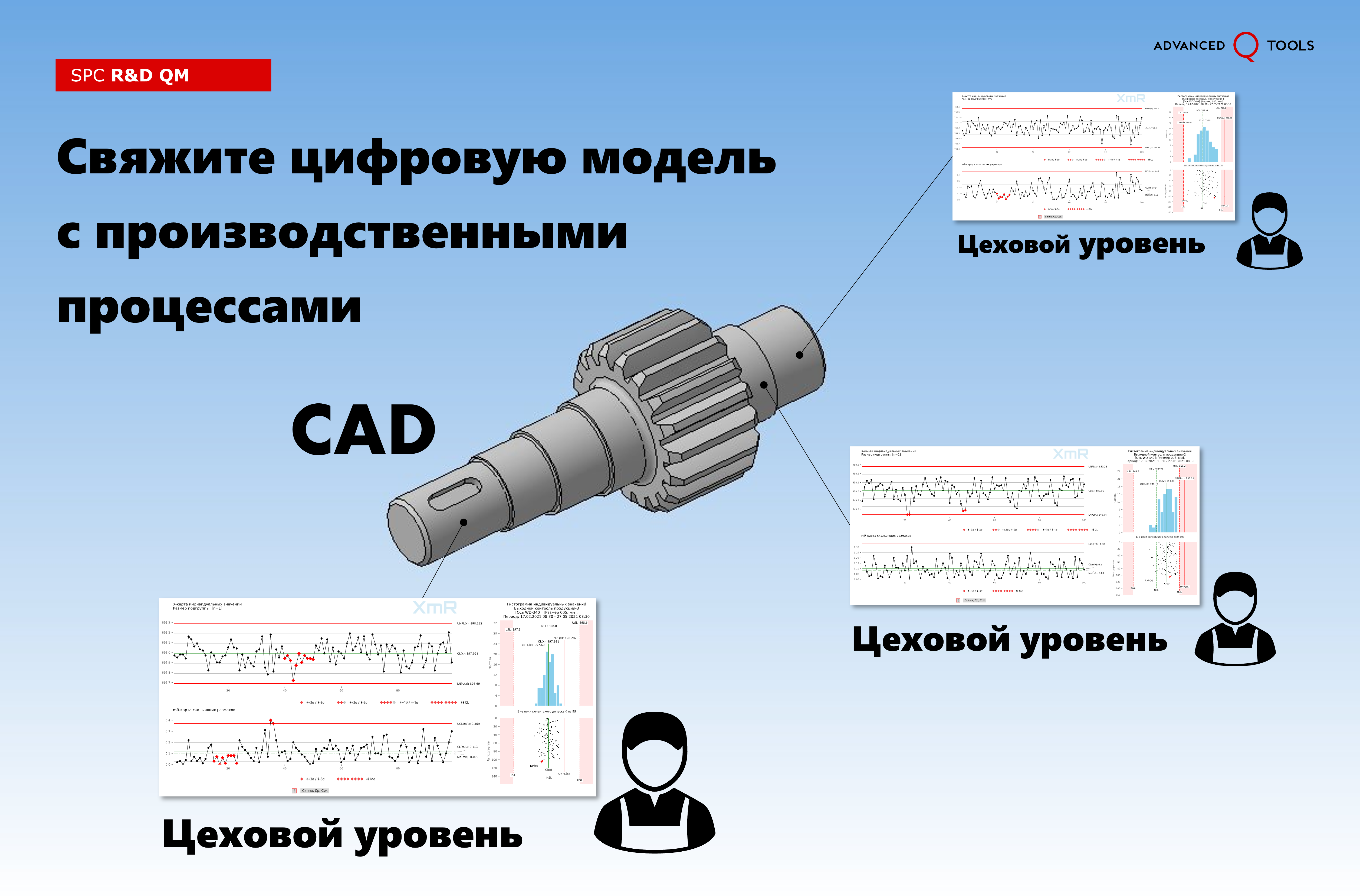
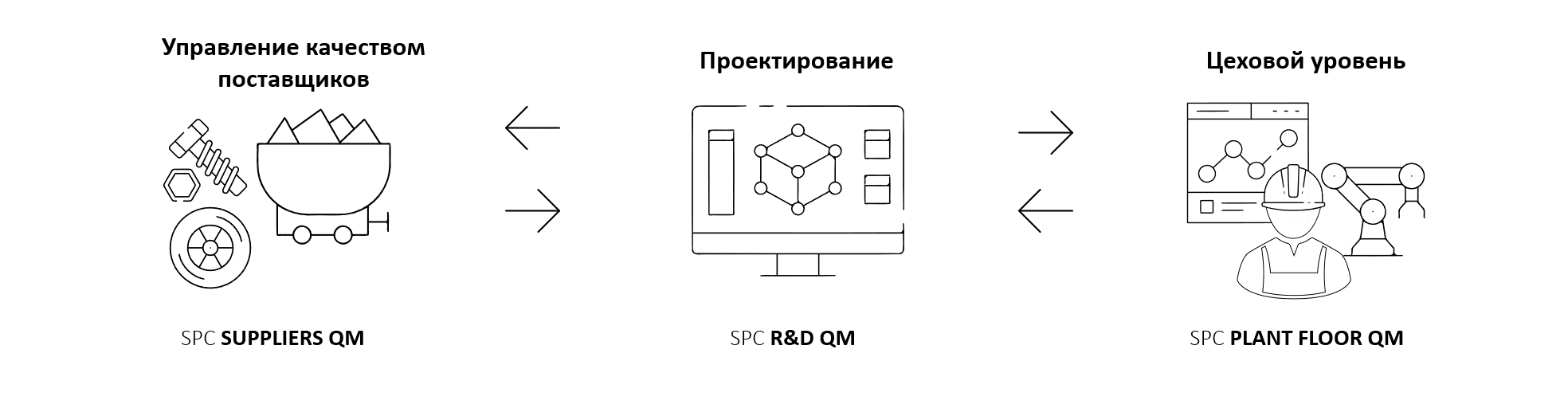
Figure 10. Outils de gestion de la qualité de nouvelle génération SPC R&D QM. Interaction des fonctions de gestion de la qualité des fournisseurs, de conception et de production.
Un exemple d'utilisation du contrôle statistique des processus avec un module de conception de produits est Système de gestion de la qualité IBS – une solution interindustrielle de classe QMS (Quality Management System) développée par Siemens PLM Software.
Encore une fois, l'utilisation fragmentée et non systématique des méthodes de contrôle statistique des processus (SPC), sans une compréhension approfondie de celles-ci, n'apportera pas d'améliorations significatives à l'entreprise dans son ensemble.
"Toute organisation envisageant d'utiliser efficacement les cartes de contrôle doit d'abord toutes les barrières décrit par Deming.
Vous ne pouvez pas simplement « mettre en œuvre un contrôle statistique des processus ». Les cartes de contrôle ne fonctionnent pas en vase clos. Leur utilisation impose certaines exigences aux travailleurs et à la direction, et l'organisation doit faire tout son possible pour répondre à ces exigences. Une fois que la philosophie de la carte de contrôle fera partie de la culture d’entreprise ou même de la structure de l’organisation elle-même, les interférences occasionnelles des travailleurs ou de la direction ne pourront plus interférer avec quoi que ce soit.
Le contrôle statistique des processus est avant tout une vision du monde globale, soutenue par certaines méthodes. C'est une façon de penser, et c'est de cela qu'il s'agit. Sans une telle réflexion, les méthodes sont complètement inutiles ! Seule la haute direction peut souligner l’importance des cartes de contrôle pour l’amélioration continue. Si la haute direction y apporte un soutien actif, l’impact potentiel de la mise en œuvre de cartes de contrôle dépassera toutes les attentes ! "
Enfin, je voudrais vous rappeler l'une des quatre parties inextricablement liées Systèmes de connaissances approfondies , formalisé par Edwards Deming, notamment en termes de compréhension des systèmes. Et je propose de ne pas se laisser emporter par la sous-optimisation d'aucune partie (divisions) du système, mais de se concentrer sur l'amélioration de l'interaction de tous les composants du système pour atteindre ses objectifs principaux.
« Un système est une chaîne de fonctions ou d’activités interdépendantes au sein d’une organisation qui travaillent ensemble pour atteindre les objectifs de l’organisation.
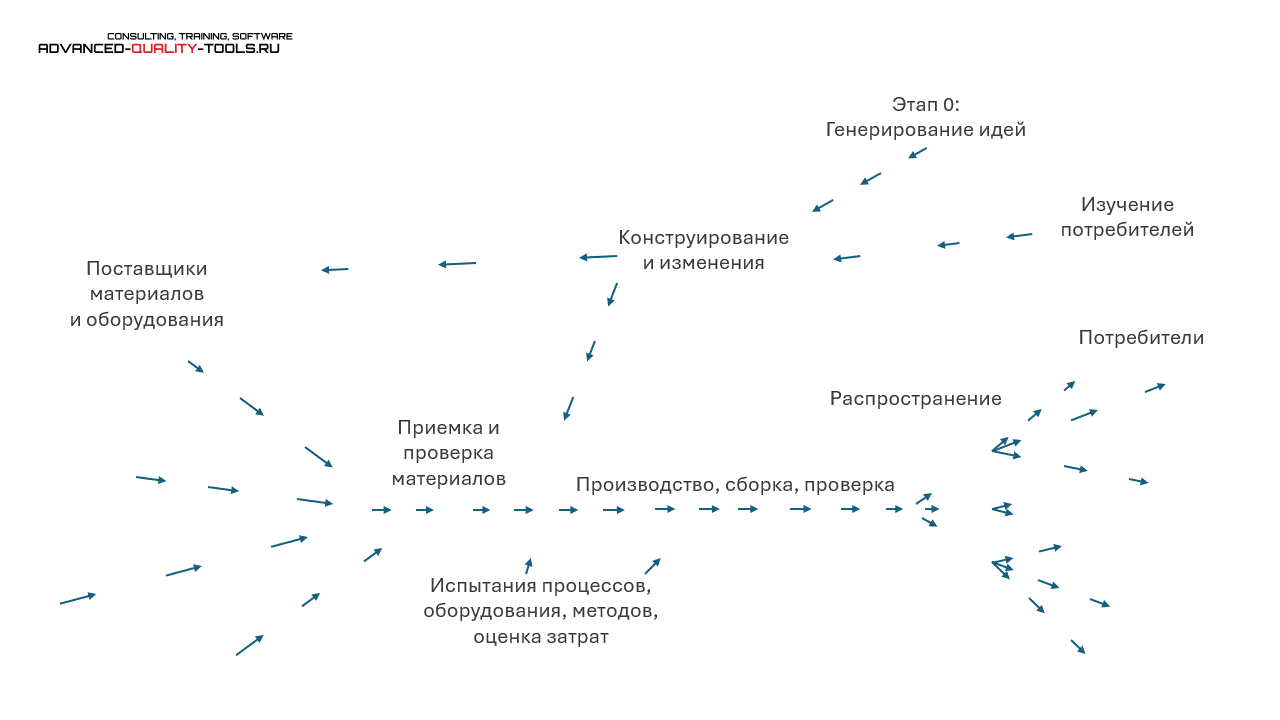
Figure 11. La production est considérée comme un système (matériel tiré des conférences d'Edwards Deming, 1950, Japon)
Le diagramme illustre la direction non seulement du flux de matériaux, mais également du flux d'informations nécessaires à la gestion de l'entreprise en tant que système. L'utilisation d'un framework fournit des retours pour l'amélioration continue d'un produit ou d'un service, pour un apprentissage continu."
Pour référence
Les sociétés industrielles étrangères ont depuis longtemps commencé à utiliser une méthodologie d’analyse statistique bidimensionnelle (2D) pour améliorer les processus de conception. Ci-dessous une capture d'écran des pages d'un document Boeing de 1998, téléchargeable dans la rubrique bibliographies notre site.
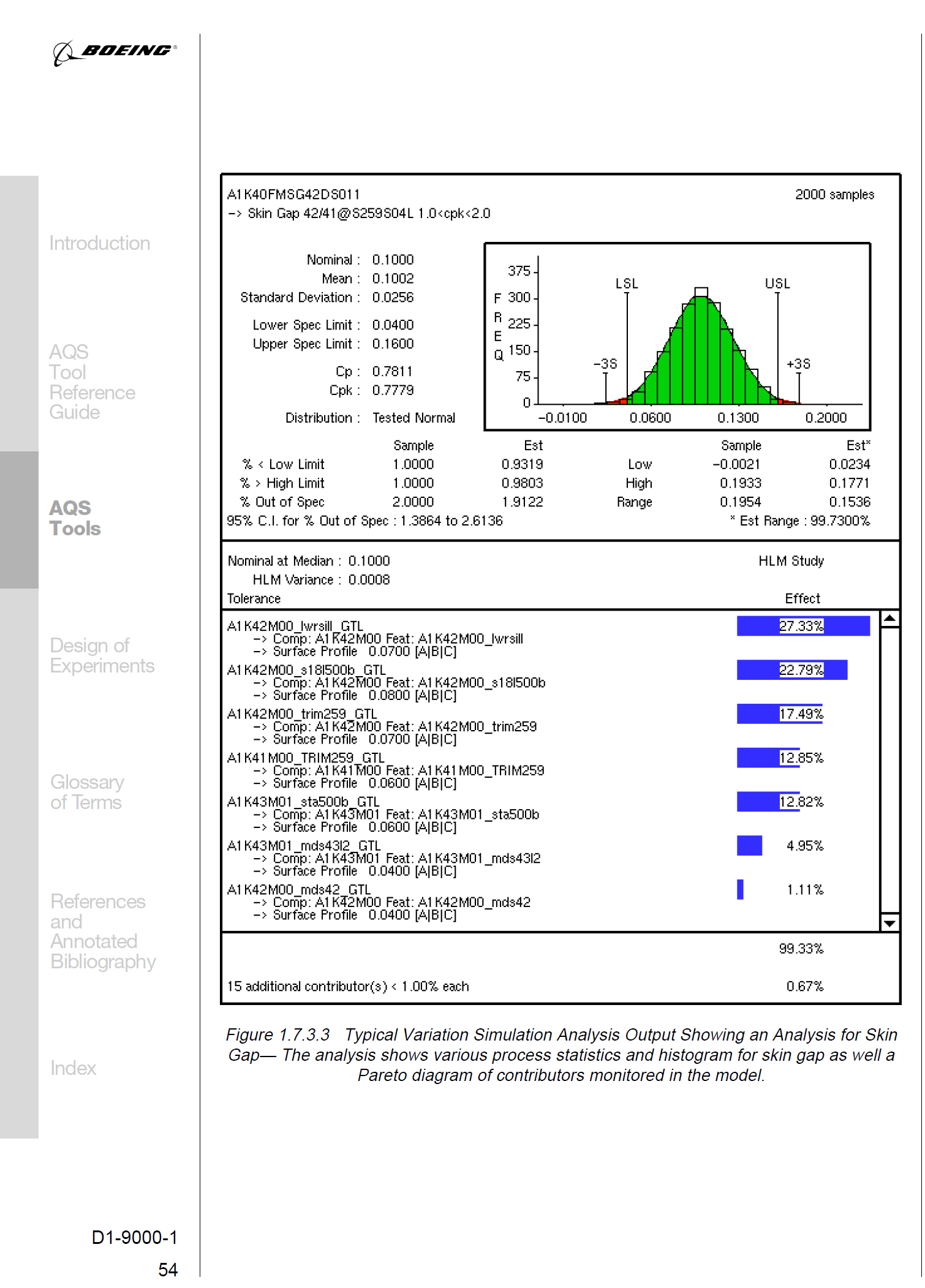
Figure 12. Analyse de variation statistique bidimensionnelle (2D) dans le domaine du GD&T (dimensionnement et tolérancement géométriques). Page du livret de la société Boeing « Outils avancés du système qualité » | "Outils avancés du système qualité Boeing", 1998.
De plus, même l’analyse statistique des variations tridimensionnelles (3D) dans le domaine du GD&T (dimensionnement et tolérancement géométriques) est utilisée depuis longtemps par les grandes entreprises occidentales.
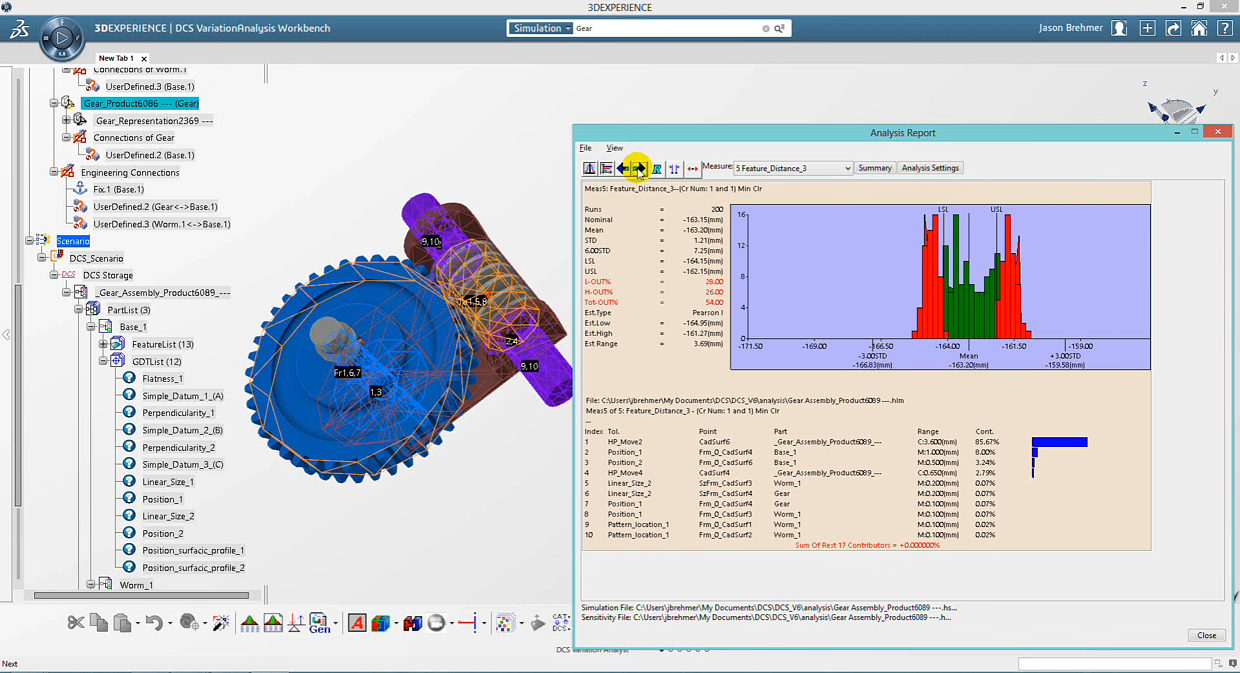
Figure 13. Analyse de variation statistique tridimensionnelle (3D) dans le domaine du GD&T (dimensionnement et tolérancement géométriques). Produit logiciel 3DCS Variation Analyst de la société américaine Dimensional Control Systems Inc. utilisé comme outil intégré à CAD CATIA V5, SOLIDWORKS, CREO, NX, 3DEXPERIENCE, ainsi que comme outil autonome.
Ces entreprises utilisent des outils de simulation automatisés dans le domaine du GD&T (Dimensionnement et tolérancement géométriques) pour vérifier le bon alignement des champs de tolérance dans la maquette numérique. Ainsi, par exemple, dans la publication [22] Les « Advanced Quality System Tools » de la société Boeing (page 51) de 1998 décrivent l'objectif et le principe de fonctionnement de l'analyse variationnelle statistique tridimensionnelle. Voir la discussion de cette question plus en détail dans le document [23] Rapport de la société Boeing ISSTECH-95-030, Tolerance Stack Analysis Methods, rédigé par Fritz Scholz (1995) dans la section bibliographies notre site.
Et ils peuvent faire des erreurs
Bien que l'analyse statistique de la variation 3D soit la prochaine étape vers la compréhension de la variabilité des produits conçus (modèle numérique), il s'agit d'une sous-optimisation avancée car elle n'est pas liée à la variabilité réelle des processus de production.
Faiblesses de l’analyse statistique des variations 2D et 3D
1. Les processus peuvent se trouver dans un état statistiquement incontrôlable (imprévisible), ce qui rend une telle analyse purement théorique.
2. La diffusion des caractéristiques contrôlées des processus stables peut s’étendre au-delà de la zone de tolérance ou dépasser la zone de tolérance. Si, dans le même temps, la direction de la production décide de conserver certains produits qui se situent en dehors des limites de tolérance, par exemple en abaissant sa « classe de qualité », l'analyse des variations ne donnera pas une idée des options possibles d'appariement. de telles pièces.
3. La propagation des caractéristiques contrôlées de processus stables peut s'opérer dans la plage de tolérance, vous ferez alors inutilement des calculs d'options qui ne se produiront pas dans la réalité.
4. Les processus peuvent être mal centrés dans le champ de tolérance, il existe alors un risque de commettre des erreurs par rapport aux paragraphes 2 et 3 ci-dessus.