Le plan du tout ou rien s’oppose à l’utilisation de tables pour l’inspection aléatoire de réception de la qualité. Edwards Deming
"L'utilisation de tables d'inspection par échantillonnage pour acceptation ne peut pas être adaptée pour minimiser le coût total moyen de l'inspection des matériaux entrants et les conséquences de l'autorisation de la production de matériaux défectueux."
Source des documents cités : [2] - W. Edwards Deming, « Out of the Crisis » (« Out of the Crisis », W. Edwards Deming - M. : Alpina Publisher, 2017. Editeurs scientifiques Y. Rubanik, Y. Adler , V. Shper). Vous pouvez acheter le livre auprès de l'éditeur Éditeur Alpina .
L'article a été préparé par le directeur scientifique du Centre AQT Sergueï P. Grigoriev
Le libre accès aux articles ne diminue en rien la valeur des matériaux qu'ils contiennent.
Préface
Devrions-nous essayer de rejeter tout ou partie des articles défectueux d’un envoi entrant ? Ou devrions-nous envoyer chaque lot, sans passer par l’inspection, directement en production ? Une solution économiquement rationnelle serait d'utiliser le plan de contrôle « tout ou rien » pour les matières premières, matériaux et composants entrants proposé par Edwards Deming.
Dans tous les cas, pas un seul produit fabriqué par l'entreprise qui ne répond pas aux exigences ne devrait parvenir à notre acheteur.
La règle de contrôle des intrants tout ou rien est utilisée pour minimiser le coût total moyen par unité de production d’une entreprise. La règle du « tout ou rien » est une règle permettant de prendre une décision concernant le contrôle à 100 % d'un lot de matériaux entrant avec le rejet des matériaux défectueux ou la mise en production d'un tel lot sans contrôle entrant, suivi du remplacement et du remaniement des la proportion de produits défectueux formés à la suite d'un tel passage sans contrôle entrant.
Si vous effectuez un contrôle à l'arrivée des matières premières, des matériaux et des composants pour le contrôle par échantillonnage, il est préférable de savoir que :
« Si le degré de contrôle statistique sur la qualité des matériaux entrants est élevé, le contrôle des échantillons ne fournirait pas d’informations sur le reste du lot inspecté, en raison du manque de preuves de corrélation entre eux dans ce cas. »
Une confirmation pratique de l'affirmation d'Edwards Deming selon laquelle le contrôle d'échantillonnage, par exemple, à l'aide de tableaux de contrôle qualité d'acceptation aléatoire ne donne pas une idée du nombre de produits défectueux dans le lot contrôlé, peut être expérimentez avec des perles rouges , dans lequel des échantillons mécaniques aléatoires d'un mélange de billes rouges et blanches donnent à chaque fois une valeur de la proportion de billes rouges qui diffère de la proportion réelle de billes rouges dans le mélange contrôlé, à la fois supérieure et inférieure. L’expérience a utilisé une carte np de contrôle du nombre de billes rouges pour des échantillons de même taille.
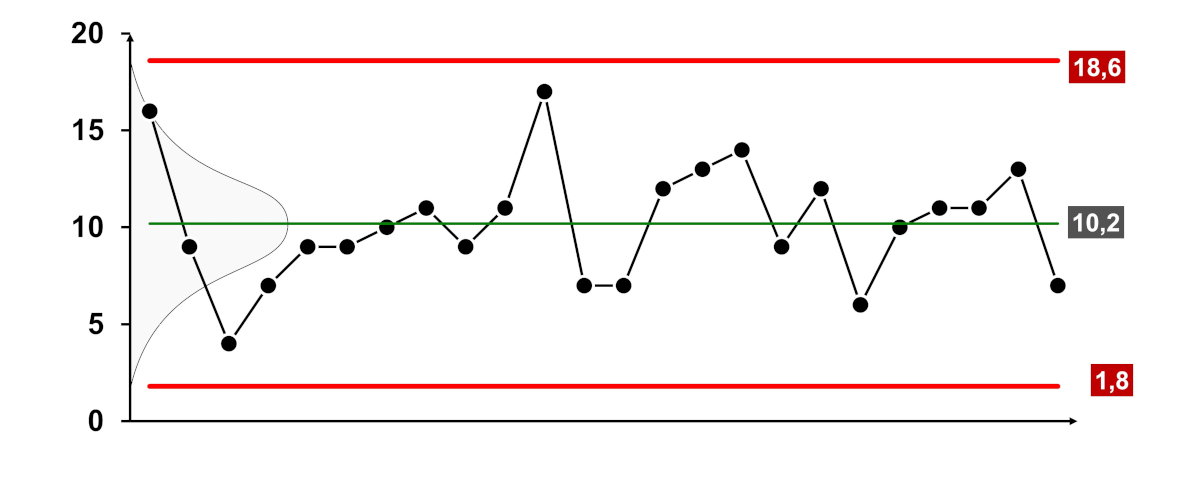
Riz. Carte np de contrôle de l'expérience des perles rouges menée par Edwards Deming en 1983.
« Les règles permettant de minimiser les coûts moyens totaux s'avèrent extrêmement simples dans certaines conditions.
Désignations :
p est la proportion moyenne de produits défectueux dans le lot de pièces entrant ;
k 1 - coût du contrôle à réception d'une pièce ;
k 2 - les frais de démontage, de réparation, de remontage et de nouveau test d'une unité qui est tombée en panne en raison d'une pièce défectueuse entrée en production.
Condition 1 :
Le pire lot entrant aura un taux moyen de défauts (p) inférieur à (k 1 /k 2 ).
p<k 1 /k 2
Dans ce cas : Pas de contrôle d’entrée. Il faut se fier entièrement à l'inspection au moment des tests des composants.
Explication, Sergey P. Grigoryev :
Dérivation de la formule Condition 1, lorsque le coût total de correction de toutes les unités comportant des pièces défectueuses du lot entrant (N×p×k 2 ) sera inférieur au coût d'inspection de la totalité des pièces entrantes (N×k 1 ).
(N) - taille du lot de pièces entrant, pcs., avec la part de pièces défectueuses (p) :
N×p×k 2 <N×k 1
réduire l'expression à :
p×k 2 <k 1
Alors:
p<k 1 /k 2
Condition 2 :
Le meilleur lot entrant aura une proportion d'articles défectueux (p) supérieure à (k 1 /k 2 ).
p>k 1 /k 2
Dans ce cas : contrôle d’entrée à 100 %. Et effectuer un contrôle au point de test des produits finis.
Explication, Sergey P. Grigoryev :
Dérivation de la formule Condition 2, lorsque le coût total de correction de toutes les unités comportant des pièces défectueuses du lot entrant (N×p×k 2 ) sera supérieur au coût d'inspection de la totalité des pièces entrantes (N×k 1 ).
(N) - taille du lot de pièces entrant, pcs., avec la part de pièces défectueuses (p) :
N×p×k 2 >N×k 1
réduire l'expression à :
p×k 2 >k 1
Alors:
p>k 1 /k 2
(k 1 /k 2 ) - qualité d'équilibre, ou point d'équilibre.
(k 2 ) sera toujours plus grand (k 1 );
donc le rapport (k 1 /k 2 ) sera compris entre 0 et 1.
Si vous appliquez la règle de la Condition 2 dans une situation où la règle de la Condition 1 devrait être appliquée, alors le coût total sera maximum. L'inverse est également vrai."
Exemple (Sergey P. Grigoryev)
Donné:
p (proportion moyenne d'articles défectueux dans le lot de pièces entrant) = 0,05 ;
k 1 (coût du contrôle à réception d'une pièce) = 100,00 ₽ ;
k 2 (le coût du démontage, de la réparation, du remontage et du nouveau test d'une unité qui est tombée en panne en raison d'une pièce défectueuse entrée en production) = 1 000,00 ₽ ;
lot d'entrée = 1 000,00 pièces.
Condition 1 : p<k 1 /k 2 - Pas de contrôle d'entrée.
Condition 2 : p>k 1 /k 2 - Contrôle entrant à 100%.
Calculs
p = 0,05
k 1 /k 2 = 100,00 ₽ / 1 000,00 ₽ = 0,10
0,05 < 0,10
p<k 1 /k 2 - correspond à la Condition 1 - Pas de contrôle d'entrée.
Solution
Sélectionnez le plan « Aucun contrôle ».
Vérification de la solution
Le coût d'un contrôle à 100% à l'entrée sera de :
1 000 pièces × 100,00 ₽=100 000,00 ₽
Le coût du passage des matériaux défectueux sera de :
1 000 pièces × 0,05 × 1 000,00 RUR=50 000,00 RUR
Par conséquent, autoriser la mise en production d'une pièce défectueuse, dans ce cas, avec démontage, réparation, remontage et test ultérieurs d'une unité défaillante en raison de l'entrée en production d'une pièce défectueuse, coûtera en effet 50 000,00 de moins qu'une inspection à l'arrivée de 100 % ₽.
« Ainsi, un état de contrôle statistique présente un net avantage. Pour savoir si le flux de lots entrants répond à la condition 1 ou à la condition 2 ou s'il est dans un état proche du chaos, il suffit de suivre le contrôle statistique et le taux moyen de défauts à l'aide de graphiques construits. sur la base d'essais continus sur de petits échantillons (comme dans tous les cas), de préférence en collaboration avec et dans les locaux du fournisseur.
Autres conditions observées en pratique (Edwards Deming)
Une position intermédiaire de la distribution avec un écart modéré par rapport à la contrôlabilité statistique.
Nous allons maintenant analyser deux types de situations intermédiaires pour la répartition de la proportion d'articles défectueux dans les lots entrants. Peut-être qu'en utilisant nos propres cartes de contrôle, ou les cartes du fournisseur, ou des cartes entretenues conjointement, nous pouvons prédire que seule une petite partie de la distribution se situera à droite du point d'équilibre. Dans ce cas, nous pouvons adopter une règle de « non-contrôle ». Cette règle permettra de s'approcher du minimum des coûts totaux moyens, à condition que la partie de la distribution qui se situe à droite du point d'équilibre soit petite.
Situation inverse : seule une petite partie de la répartition de la part des produits défectueux dans les lots entrants se situe à gauche du point d'équilibre. Sachant cela, vous pouvez accepter en toute sécurité la règle du contrôle à 100 % des lots entrants.
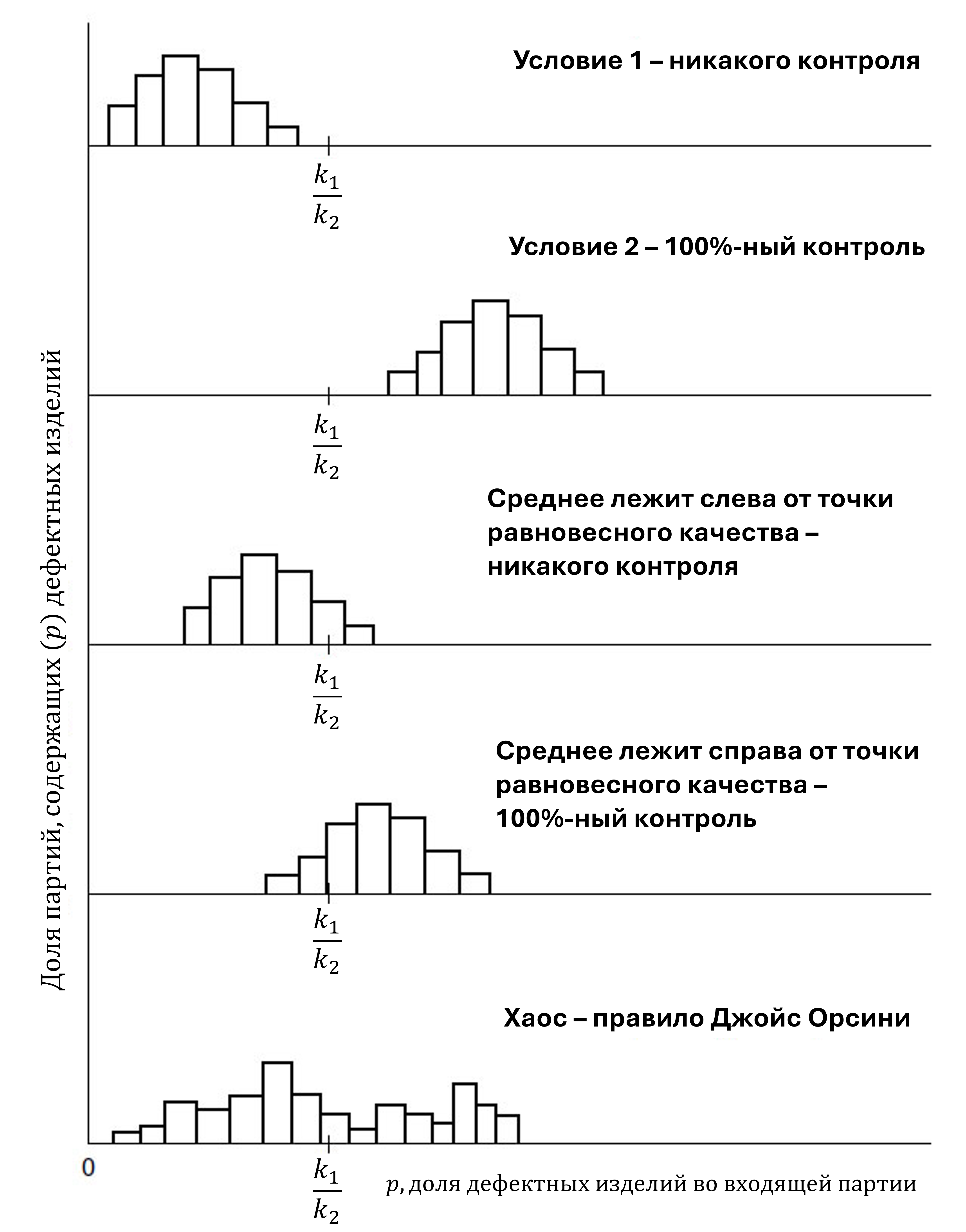
Riz. 1. Situations possibles lors de la réception de produits entrants par lots.
Le point B est le point de qualité d'équilibre, auquel p = k
1
/k
2
. Source:
[2]
Edwards Deming, Sortir de la crise
Evolution de la part des produits défectueux dans les lots entrants
Supposons qu'une tendance se dessine vers une augmentation de la proportion de produits défectueux. Aujourd'hui, nous sommes dans la condition 1 et n'avons aucun contrôle, mais (p) dépend du temps et augmente, peut-être à un rythme constant et peut-être de manière irrégulière. Dans deux jours nous entrerons dans la zone Condition 2 : nous sommes prévenus. Les cartes de contrôle du fournisseur ou les nôtres révéleront une tendance si elle existe. Ce problème peut être facilement résolu.
Problèmes causés par le basculement entre différents fournisseurs
En raison des changements dans les sources matérielles à l’entrée du système, des problèmes surviennent toujours. Limitons-nous à considérer deux sources. Si les deux sources sont bien ou modérément contrôlées statistiquement et peuvent être séparées l’une de l’autre, alors en principe chaque source satisfait à la condition 1 ou à la condition 2, selon que la moyenne de cette source se situe à gauche ou à droite du point d’équilibre. Cette idée est simple en termes, mais peut s'avérer difficile à mettre en œuvre dans certaines usines.
Si les matériaux provenant de deux sources sont mélangés de manière homogène dans des proportions constantes, et si les deux sources présentent un contrôle statistique suffisant, alors les lots mélangés peuvent être considérés comme un mélange binomial, dont le coût moyen minimum de contrôle peut être atteint en utilisant la méthode du tout ou rien. règle.
Les matériaux provenant de deux sources posent des problèmes supplémentaires à la production. Un mélange homogène de matériaux provenant de deux sources constitue le pire des cas pour un responsable de fabrication.
La première étape consiste à réduire le nombre de fournisseurs à un. Si un produit de qualité variable est fourni par une source unique, alors le fournisseur et son client doivent travailler ensemble pour l'améliorer, dans le but de satisfaire à la Condition 1 et d'atteindre finalement le zéro défaut.
État de chaos
Il est relativement facile de décider quoi faire dans une situation où la position de la distribution fluctue légèrement plus près ou plus loin du point d’équilibre.
Près du point d’équilibre, peu importe que nous ayons un contrôle à 100 % ou aucun contrôle. Je choisirais un contrôle à 100 % pour collecter les informations le plus rapidement possible. Si nous ne pouvons pas affirmer que la qualité des matériaux entrants se situe principalement à droite ou à gauche du point d'équilibre, mais qu'au contraire elle fluctue largement, passant par le point de qualité d'équilibre, alors nous sommes dans un état de chaos.
1. Cette situation inacceptable peut survenir lorsque du matériel présentant une grande variabilité et une qualité imprévisible est fourni par une source unique.
2. Une telle variation autour du point de qualité d’équilibre peut résulter de l’obtention de matériaux provenant de deux ou plusieurs sources de qualité très variable. Dans ce cas, le passage d'une source à une autre s'effectue de manière incontrôlable, sans séquence réfléchie. Nous devrions sortir de cet état le plus rapidement possible et passer à la Condition 1. Mais les lots continuent d’arriver et nous devons faire quelque chose avec eux. Comment devrions-nous les traiter ?
Si chaque lot était accompagné d’une étiquette nous indiquant la proportion d’articles défectueux qu’il contient, il n’y aurait aucun problème. On obtiendrait un coût total moyen minimum en plaçant chaque lot, l'un après l'autre, à droite ou à gauche du point d'équilibre et en appliquant la règle du tout ou rien de lot en lot.
Mais les lots ne sont pas marqués. Cependant, dans un état de chaos, il existe une certaine corrélation entre la qualité des produits de l’échantillon et celle du reste du lot. Par conséquent, dans un état de chaos, vous pouvez tester des échantillons et, en utilisant une règle, décider d'envoyer complètement la pièce restante en production ou de la rejeter.
L'échantillonnage, quelle que soit la façon dont il est utilisé, aura pour conséquence que certains lots se retrouveront du mauvais côté du point d'équilibre, avec pour conséquence de maximiser les coûts totaux pour le lot mal identifié.
Dans un état de chaos, on pourrait être enclin à un contrôle à 100 %. Cette décision a du sens.
Ne soyez jamais laissé sans informations
La règle d’interdiction d’entrée n’implique pas de conduire dans l’obscurité avec les phares éteints. Tous les matériaux entrants doivent être examinés (en sautant éventuellement certains lots) pour obtenir des informations et comparer la livraison réelle avec les notes d'expédition du fournisseur, l'inspection des tests du fournisseur et les cartes de contrôle qui l'accompagnent. S'il y a deux fournisseurs, conservez des registres pour chacun séparément.
Le conseil suivant est de s'adresser à un fournisseur pour chaque produit sur la base d'une relation à long terme et de travailler avec lui pour améliorer la qualité entrante.
Essais destructifs
La théorie précédente est basée sur le contrôle non destructif d'un prototype. Certains tests sont destructifs ; ils détruisent l'échantillon contrôlé. Un exemple est la durée de vie d'une ampoule, le nombre de calories thermiques produites en brûlant un pied cube de gaz, ou la durée de fonctionnement d'un fusible, ou en testant la teneur en laine d'un morceau de tissu. Rejeter l’intégralité du lot n’aurait aucun sens, puisqu’il n’y aurait rien à transférer en production.
Bien évidemment, pour les contrôles destructifs, la seule solution est de parvenir à un état de contrôle statistique dans la fabrication des pièces afin de les réaliser immédiatement correctement. Cette solution est la meilleure pour les contrôles destructifs et non destructifs.
Possibilité d'assemblage défectueux de nombreuses pièces
Dans les sections précédentes, nous avons parlé de produits simples constitués d’une seule pièce. Certaines pièces peuvent nécessiter une inspection à 100 % pour minimiser le coût global. Une fois testés, ils ne provoqueront pas l’échec de l’assemblage (assemblage). Les pièces restantes ne seront pas testées et la pièce défectueuse, si elle entre en production, provoquera une panne. Disons que nous avons deux pièces non testées.
Deux pièces non testées présentent des parts de p défectueuses 1 et P 1 . Alors la probabilité que l'assemblage échoue sera égale à :
Pr (je refuserai) = 1 – Pr (je ne refuserai pas) = 1 – (1 – p 1 )(1 – p 2 ) = p 1 +p 2 -p 1 p 2
Si les deux valeurs p 1 et P 2 -petit, alors cette probabilité sera proche de la valeur :
Pr (je refuserai) =p 1 +p 2
Un moyen simple d’écrire la probabilité de défaillance d’un nombre quelconque de pièces consiste à utiliser les diagrammes de Venn (décrits dans n’importe quel livre sur la théorie des probabilités).
À condition que tout p je petit. La généralisation à m parties donne :
Pr (je refuserai) =p 1 +p 2 + … +p m
Ainsi, la probabilité de défaillance augmente à mesure que le nombre de pièces augmente. Une radio peut contenir 300 pièces, bien que ce nombre dépende de la façon dont vous les comptez. Une voiture peut contenir 10 000 pièces, encore une fois selon la façon dont vous comptez. La radio dans une voiture est-elle une pièce ou 300 ? La pompe à essence est-elle en 1 pièce ou en 7 ? Quoi que vous en pensiez, le nombre de pièces dans un seul assemblage peut être écrasant.
` Mais il y a un autre problème : k 2 (le coût de correction d'un assemblage défectueux) augmente à mesure que le nombre de pièces augmente. Lorsqu’un assemblage échoue, quelle pièce est en cause ? Il est trop facile de faire un mauvais diagnostic. De plus, sur deux pièces, les deux peuvent être défectueuses.
Pour les produits composés de plusieurs pièces :
1. Nous ne pouvons autoriser que quelques pièces à satisfaire à la condition 2 (contrôle à 100 %) ; sinon le coût du contrôle sera excessif.
2. Pour les autres pièces, seule une qualité proche du zéro défaut est acceptable.
Assemblages à partir de composants complexes
Économies possibles lors de la création de sous-systèmes auxiliaires. Dans la théorie précédente, le coût k 2 augmente généralement (peut-être une multiplication par 10) à chaque étape du processus et peut atteindre des valeurs très élevées lors de l'assemblage final. Parfois, des coûts inutilement élevés peuvent être évités en créant des sous-systèmes qui se déplacent tout au long du flux d’assemblage et forment le produit final. Certains sous-systèmes, passés sous contrôle et nécessitant des remplacements et des ajustements mineurs, constituent un nouveau point de départ. Coûtk 2 sera désormais le coût de la surveillance et de l’ajustement du sous-système. La théorie, associée à des expériences utiles, peut montrer que certains sous-systèmes n'ont pas besoin d'être testés du tout, tandis que d'autres devraient être soumis à un contrôle à 100 % pour éviter une augmentation des coûts à mesure que le processus progresse. La théorie présentée dans ce chapitre vous permet de prendre la bonne décision.
Notre objectif dans les sections précédentes est de montrer qu’il existe des moyens de minimiser les coûts et de maximiser les profits si vous suivez la bonne théorie.
Dans le même temps, nous nous efforçons d’éliminer complètement les produits défectueux du processus. Nous le faisons systématiquement en comparant nos résultats de tests avec ceux du fournisseur et en appliquant des méthodes statistiques appropriées telles que les cartes X et R (cartes de contrôle Shewhart).
Une coopération fructueuse avec le fournisseur de pièces, particulièrement les plus critiques, ainsi que des tests et ajustements réussis des sous-systèmes réduisent tous les problèmes majeurs lors de l'inspection finale des systèmes à des événements rares.
Les matières entrantes sont un sous-produit pour le fournisseur
Lorsqu'un matériau critique pour le client d'un fournisseur peut être un sous-produit, représentant moins de 1 % de son activité. On ne peut pas s'attendre à ce que le fournisseur supporte le coût et le risque liés à l'installation d'équipements pour améliorer le produit.
Une recommandation possible est de considérer ce matériau comme du minerai de fer ou d’autres intrants très variables et non purifiés. Installez votre propre système de nettoyage des matériaux ou utilisez les services d'une entreprise tierce. Ce plan est efficace dans certains cas.
Difficultés à détecter des défauts rares
Les défauts rares sont difficiles à détecter. À mesure que la proportion de produits défectueux diminue, il devient de plus en plus difficile de déterminer à quel point ce nombre est petit. Il n’est pas possible de détecter tous les défauts par inspection, surtout lorsqu’ils sont rares, et cela est vrai aussi bien pour l’inspection visuelle que automatique. Il n’y a aucune raison de faire confiance à un fabricant qui prétend n’avoir qu’un défaut sur 10 000, pas plus qu’à un fabricant qui affirme avoir un défaut sur 5 000 produits. Dans les deux cas, cette proportion est difficile à estimer.
Ainsi, si (p) était égal à 1/5 000 et si le processus était dans un état statistiquement contrôlé, il faudrait alors inspecter 80 000 pièces pour en trouver 16 défectueuses.
Sergueï P. Grigoriev :
5000×16=80000
Ces données donneraient une estimation du taux moyen de défauts de p = 1/5000 pour un processus de production avec une erreur standard de σ = √16 = 4. Cette estimation du taux de défauts est imprécise, malgré la difficulté de suivre un grand nombre de 80 000 pièces. La question se pose : le procédé est-il resté stable tout au long de la production de 80 000 pièces ? Si non, quelle est la signification du chiffre 16 produits défectueux ? Question difficile.
Sergueï P. Grigoriev :
Dans ce cas, si le processus du fournisseur est dans un état statistiquement contrôlé, il est supposé fonctionner autour de la valeur moyenne c = 16 défauts pour des lots sous forme de sous-groupes de 80 000 pièces avec les valeurs de la valeur supérieure (VKG , UCL) et limites de contrôle inférieures (NKG, LCL) C- chartes : UCL, LCL = c ±3σ ou UCL, LCL = c ±3√c, ce qui se traduit par un étalement des valeurs autour de la moyenne (c=16) dans ±12.
Les formules peuvent être trouvées dans GOST R ISO 7870-1-2011 (ISO 7870-1:2007), GOST R ISO 7870-2-2015 (ISO 7870-2:2013) - Méthodes statistiques. Cartes de contrôle Shewhart [onze] .
Pour calculer (σ), Deming utilise une carte C du nombre de défauts par zone de définition constante égale à 80 000 parties.
Pourquoi 16 ? La valeur moyenne (16) permet un calcul facile de la valeur (σ) pour la carte C et fournit des limites de contrôle inférieure et supérieure.
Ainsi, pour qu'un fournisseur revendique un tel taux de défauts (1/5 000), il faut comprendre la stabilité de son processus de production, ce qui ne peut être confirmé qu'à l'aide des cartes de contrôle Shewhart, et la carte de contrôle doit être construite, par exemple, à un moment donné. minimum de huit points, où chaque point correspond au nombre de défauts par lot de 80 000 pièces avec des valeurs entières possibles de 4 à 28 défauts répartis sur règle générale autour de la moyenne : 16 défauts par lot de 80 000 pièces.
Pourquoi était-il impossible de réaliser ces opérations mathématiques simples avec la valeur moyenne des défauts c = 1 pour un domaine constant de définition de 5000 pièces ? Oui, car vous ne pourrez pas obtenir de points à partir d'entiers du nombre de défauts sur la carte de contrôle inférieurs à la valeur moyenne c=1, sauf zéro. Bien que mathématiquement il soit facile d'obtenir un nombre décimal dans les calculs, par exemple = 0,3, comment imaginez-vous la possibilité d'obtenir en conditions réelles le nombre de défauts de 0,3 dans un lot (sous-groupe) testé ?
Il existe des exemples où il n'y a pas une seule panne sur des millions de pièces, ou leur nombre est très petit ou il en manque sur 10 milliards. Aucun contrôle des produits finis ne permettra d'obtenir les informations requises lorsque la proportion de produits défectueux est si faible. La seule façon possible de savoir ce qui se passe dans des conditions aussi extrêmes est d'utiliser des cartes de contrôle avec les mesures réelles des pièces au cours du processus. Cent observations, telles que 4 éléments consécutifs 25 fois par jour, donneraient 25 points d'échantillonnage pour les graphiques X et R des moyennes et des plages de sous-groupes. Les cartes de contrôle Shewhart indiqueraient si le processus se déroule sans changement ou si une défaillance s'est produite quelque part et que la production d'un certain nombre de produits doit être arrêtée jusqu'à ce que la cause soit découverte. Une fois la raison trouvée, vous pouvez décider de refuser l’ensemble des produits pendant une certaine période ou d’ignorer certains produits. Les capacités toujours croissantes des cartes de contrôle XbarR des sous-groupes de moyenne et de plage deviennent de plus en plus évidentes.
Sergey P. Grigoryev : Donald Wheeler dans l'article Cartes de contrôle pour les données alternatives (comptes) p-chart, np-chart, C-chart et u-chart ou une carte XmR de valeurs individuelles ? renforce cette recommandation d’Edwards Deming :
"Comme il est rarement judicieux d'utiliser des quantités discrètes (comptes) lorsque des résultats de mesure peuvent être obtenus, l'utilisation d'attributs est généralement limitée aux situations dans lesquelles les "bloopers" peuvent être comptés. Cependant, définir un "blooper" pose généralement de grandes difficultés. la principale difficulté dans la définition de « bêtisier » est un problème définitions opérationnelles ".
Utiliser les réservations
Parfois, il est possible et raisonnable, lors de la conception d'équipements complexes, de placer deux ou plusieurs pièces en parallèle, de sorte que si l'une d'elles tombe en panne, l'autre reprend automatiquement ses fonctions. Deux pièces parallèles, chacune avec un taux de défauts moyen p je , sont équivalents à un avec un taux moyen de défauts égal à p je ². Si, par exemple, p je =1/1000, alors p je ²=1/1000000.
Les restrictions de poids et de taille peuvent bien entendu empêcher le recours à la redondance.
Il y a d'autres préoccupations : la partie de secours fonctionnera-t-elle en cas de besoin ? La meilleure solution est peut-être une fiabilité élevée dans une seule pièce.
Conclusion
Les matériaux et la fabrication défectueux ne seront pas tolérés dans le processus de fabrication. La théorie exposée ci-dessus nous enseigne combien il est important de ne tolérer des matériaux défectueux à aucune étape de la production. Le produit d’une opération est la matière première de la suivante. Un matériau défectueux, une fois produit, reste défectueux jusqu'à ce que le défaut soit découvert, même si, heureusement, plus tard lors des tests, la correction et le remplacement ne seront pas bon marché.
L’état de contrôlabilité statistique présente un net avantage. Pour savoir si le flux de lots entrants satisfait à la condition 1 ou à la condition 2 ou s'il est dans un état proche du chaos, il suffit de surveiller le contrôle statistique et le pourcentage moyen d'articles défectueux à l'aide de cartes de contrôle Shewhart construites à partir de tests en cours sur de petits échantillons (comme dans tout cas), de préférence en coopération avec le fournisseur et sur son territoire.
Des exceptions
De nombreux documents d’entrée ne suivent pas la théorie décrite ci-dessus. Par exemple, un réservoir de méthanol après agitation avec un tuyau d'air. Un échantillon de méthanol prélevé dans presque n’importe quelle partie du réservoir sera presque le même. Cependant, les entreprises chimiques échantillonnent le méthanol à plusieurs niveaux. Un exemple plus proche serait peut-être de déguster un verre de gin ou de whisky. Nous sommes d'accord que peu importe d'où nous prenons la portion : du haut, du milieu de la bouteille ou du bas.
Explication Sergey P. Grigoryev : Le paragraphe ci-dessus fait référence à des cas exceptionnels où le résultat du contrôle de l'échantillon peut être attribué à l'ensemble du lot.
Le chauffage des hauts fourneaux crée des problèmes et constitue un autre exemple auquel la théorie présentée dans ce chapitre ne s’applique pas. Le chauffage n'est pas uniforme. Certaines entreprises prélèvent de petits échantillons sur chaque bouteille. Ces échantillons, s'ils sont analysés, fournissent des données pour un diagramme de processus qui pourrait montrer les variations de qualité du premier au dernier moulage, fournissant ainsi des indices sur les améliorations.
Explication de Sergey P. Grigoryev : Le paragraphe ci-dessus traite de cas exceptionnels où le procédé est, par définition, hétérogène à différentes étapes du procédé avec la possibilité de prélever un échantillon à chaque étape ; dans de tels cas, pour analyser la variation entre les différents lots (coulées), il est nécessaire d'utiliser une carte XmR de contrôle des valeurs individuelles.
Voir la solution open source : Problèmes liés à l'utilisation de tableaux pour le contrôle qualité de l'acceptation aléatoire .