Ne vous laissez pas emporter par les indicateurs KPI numériques agrégés en gestion de la qualité
Matériel préparé par : Directeur scientifique du Centre AQT Sergueï P. Grigoriev .
Le libre accès aux articles ne diminue en rien la valeur des matériaux qu'ils contiennent.
Une entreprise russe a annoncé sur son site Web la création d'un modèle unifié de gestion de la qualité des produits pour toutes les divisions de l'entreprise. Dans le même temps, des objectifs chiffrés spécifiques ont été cités comme un autre exemple de l’ignorance du management moderne.
« Les résultats des travaux d'ici 2025 devraient être une réduction jusqu'à 25 % des coûts d'élimination des défauts des produits identifiés au stade du développement et de la production, ainsi qu'une réduction de moitié du nombre de contrats non exécutés en raison d'une qualité insuffisante. Cela devrait nous permettre de dresser un tableau unifié de l'état de la qualité des produits de toutes les organisations au sein de l'entreprise et d'améliorer l'efficacité des systèmes de gestion de la qualité.
Notre équipe a présenté l'importance des changements fondamentaux dans la structure de gestion de la qualité de ce groupe d'entreprises et a démontré, à l'aide d'exemples concrets, le manque de connaissances nécessaires à cet effet dans le groupe d'entreprises.
« Si vous pouvez atteindre un objectif sans méthode, alors pourquoi ne l’avez-vous pas fait l’année dernière ?
Il y a un plus dans la déclaration : l'entreprise a ouvertement signalé ses problèmes à une telle échelle. Mais ces problèmes ne peuvent apparemment pas être résolus par nous-mêmes. Sinon, pourquoi ne l’ont-ils pas fait plus tôt ?
« Nous ne pouvons pas résoudre nos problèmes avec le même niveau de réflexion qui les a créés. »
Les méthodes acceptées de gestion par objectifs (chiffres) sont étonnantes. Il suffit de réduire le coût d'élimination des défauts de 25 % d'ici 2025. D'où vient ce chiffre de 25 % ? Pourquoi pas 23 ou 27 % ? Qu’en est-il des 75 % restants ? Par quelles méthodes ?
L'entreprise connaît-elle actuellement tous les coûts de reprise engagés au cours des périodes précédentes ou uniquement ceux enregistrés ? S’agit-il uniquement de coûts directs ou s’agit-il de pertes indirectes et incommensurables ? Parmi ces derniers figurent la démotivation des travailleurs due à l’incapacité d’être fiers de leur travail, la perte de la réputation de l’entreprise en tant que fournisseur, etc.
Les processus de l’entreprise qui produisent des produits défectueux sont-ils statistiquement contrôlés ? Si tel est le cas, seule la haute direction des entreprises de l'entreprise peut changer la situation par des changements systémiques. Dans le cas contraire, il est urgent de s’attaquer aux causes particulières au niveau local et de ramener ces processus dans un état statistiquement contrôlable (prévisible). Ce n’est qu’à ce moment-là qu’il sera possible d’engager des changements systémiques.
Fixer des objectifs numériques pour des processus instables (imprévisibles) est inutile : personne ne peut prédire leur comportement. Les objectifs numériques pour des processus stables n'ont pas non plus de sens, puisque la stabilité indique un meilleur état du processus avec une répartition naturelle (aléatoire) des données de haut en bas par rapport à la moyenne dans une plage de +/- 3 sigma, conformément à la règle empirique des données. distribution. Ces déclarations sont expliquées plus en détail dans la décision ouverte « Contrôle statistique des processus (SPC) vs. Standardisation des processus et opérations de fabrication ».
Edwards Deming, dans son livre « Overcoming the Crisis », a écrit sur les objectifs adéquats de l'entreprise :
« De véritables objectifs sont nécessaires pour optimiser l’organisation dans son ensemble, et non pour sous-optimiser ses différentes parties. Un objectif peut paraître assez général. Un objectif sans préciser les méthodes pour l’atteindre n’a aucun sens.
Et qu’en est-il de la réduction de moitié du nombre de contrats non exécutés en raison d’une qualité insuffisante ? Cet indicateur est-il dans un état statistiquement contrôlé ou non ? Pourquoi 2 fois ? Comment cette valeur sera-t-elle évaluée à l’avenir ? Par quelles méthodes ? Ici, mes commentaires sont probablement inutiles.
Comment, en général, quelqu’un peut-il se fixer de tels objectifs ?
Il est surprenant que dans le premier indicateur, nous parlions de réduire les retouches, en particulier les retouches. Pas un mot sur les nouvelles méthodes permettant d’améliorer la qualité des processus qui génèrent ces altérations. Comment vas-tu faire ça ? Par quelles méthodes ? En quoi ces méthodes sont-elles différentes de ce que vous faisiez auparavant ? Même si de telles méthodes étaient prévues, comment comprendre, même lors de leur planification, qu'elles entraîneront une réduction de 25 % du coût d'élimination des défauts ?
Qu'arrivera-t-il aux rares organisations dont le coût absolu pour éliminer les défauts, grâce à un travail continu réussi avec la qualité de tous les processus, est minime parmi toutes les organisations incluses dans l'entreprise ? Eux, tout comme ceux qui ne l'ont pas fait du tout, devront trouver un moyen de réduire cet indicateur de 25 % ? Pas moins? Sinon ils perdront cette compétition ?
« Gérer par les chiffres est une tentative de gérer sans savoir quoi faire, ce qui revient en fait généralement à gérer par la peur. »
Le principal danger ne réside pas dans les indicateurs déclarés eux-mêmes, mais dans la forte probabilité de leur utilisation dans le système de rémunération (paiements) des dirigeants des organisations de l'entreprise. Comment pourrait-il en être autrement dans le style de management dominant aujourd’hui ? Le degré élevé d’agrégation des indicateurs dans la gestion de la qualité constitue un autre obstacle à la recherche des causes « en amont ». Tout indicateur agrégé (résultant) masque les signaux dans les sources de données de variabilité, les transformant en bruit au niveau résultant, privant ainsi le personnel de la capacité de voir les signaux dans les sources. Trouver des signaux indiquant la présence de causes spécifiques de variabilité est ce qui doit être fait en premier lieu pour améliorer les processus. Dans le même temps, toute action réactive de la direction face au bruit est erreur de première espèce , ne faisant qu'aggraver la situation. Il est important de comprendre qu'à un niveau d'agrégation élevé, seuls des changements catastrophiques seront perceptibles sous forme de signaux (E. Deming). Que faire après avoir éliminé ou pris le contrôle des sources de causes particulières de variabilité, voir d'autres documents sur notre site Web.
"La recherche amont est un levier puissant pour résoudre les problèmes de mélange."
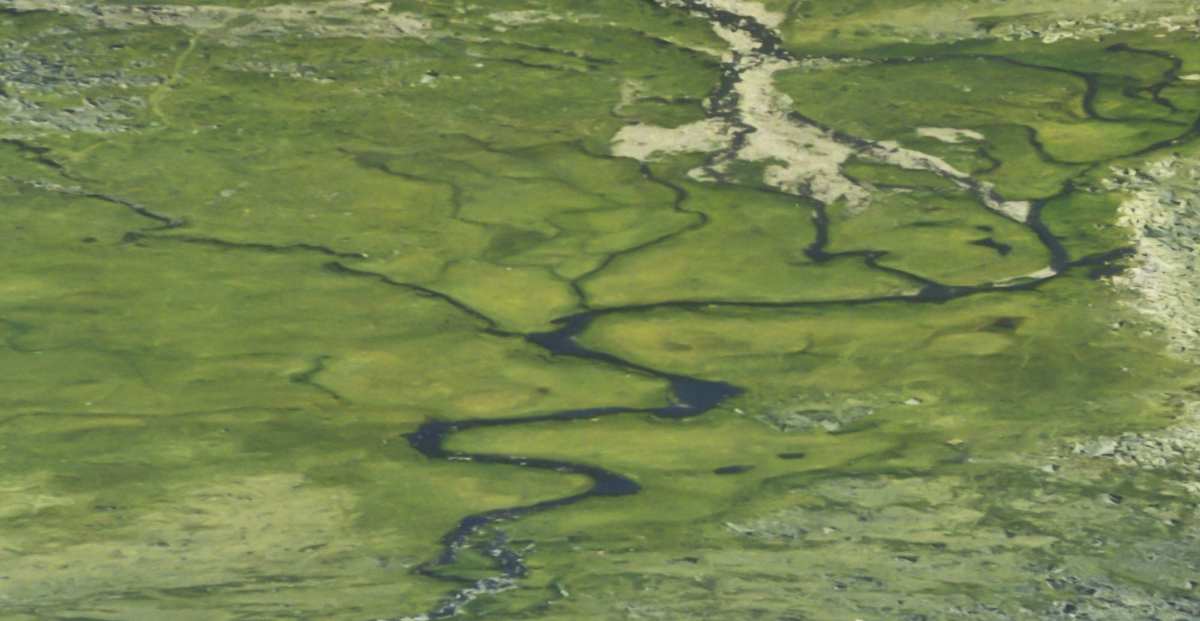
Figure 1. La recherche en amont est un levier puissant pour résoudre les problèmes de mélange.
Je suis sûr que les chefs d'organisation atteindront cet indicateur (réduction jusqu'à 25 % des coûts d'élimination des défauts des produits). L’avantage de la gestion par objectifs (MBO) est qu’il existe de nombreuses mauvaises façons d’y parvenir. Voici quelques exemples:
- Sans améliorer la qualité des processus de conception et de production, réduire le volume ou la part de production des produits présentant les plus grands défauts.
- Redistribuez une partie du coût d'élimination des défauts vers d'autres postes de dépenses non affectés par les KPI.
- Réduisez le temps et les coûts de développement de nouveaux produits grâce à réduction des tests grandeur nature , en les remplaçant par des tests sur modèles numériques.
- Les tolérances des spécifications peuvent être élargies ou les définitions des défauts peuvent être vagues. "C'est bien" que l'industrie n'y prête pas suffisamment attention définitions opérationnelles , y compris les défauts.
- La soi-disant « liste de permis », très courante dans les « grandes » entreprises, où les défauts et les défauts coûtent très cher. L'essence de cette méthode est de donner aux produits défectueux, en fonction du degré de défectuosité, le statut des produits de 1ère, 2ème et 3ème classes de qualité. Tous les services concernés signent la « Feuille d'autorisation » pour chaque pièce défectueuse, chacun devant signer que ce défaut n'est pas du tout un défaut.
Dans ma pratique, il y a eu un exemple où un lot produit a été rejeté par un inspecteur du contrôle qualité, et le lendemain, un autre inspecteur n'a trouvé aucune raison de rejet et a autorisé l'expédition du lot à l'acheteur. Alors y avait-il des défauts ou pas ?
Dans un autre exemple, le chef du service de contrôle qualité a suggéré de « mélanger » les produits défectueux dans un lot avec les bons, espérant ainsi réduire les pertes de l’entreprise liées à l’élimination des défauts. Cela pourrait en effet réduire le coût des retouches, mais compromettrait la poursuite de la coopération avec l'acheteur du lot « mixte ».
Alors, à quoi sert un indicateur aussi agrégé que les « coûts de reprise » ? Que feront vos salariés si leurs salaires ou leurs notes dépendent de la valeur de l’indicateur ? Vous pourriez affirmer que vous devez travailler avec des processus qui produisent des produits défectueux. Oui je suis d'accord. Comment travailler? Ce qu'il faut faire? Comment savez-vous? Si vous savez quoi faire, pourquoi ne l’avez-vous pas fait avant ? Dans tous les cas, une véritable amélioration des processus et des opérations technologiques nécessite de nouvelles connaissances et du temps, et les salaires peuvent être réduits ou la note d’un employé dégradée dès maintenant. Pensez-y.
Il est dommage que le temps et les ressources intellectuelles de tous les niveaux des salariés de l'entreprise soient consacrés à la recherche d'astuces pour atteindre cet indicateur en utilisant les méthodes les plus accessibles. C’est ce qui se passe habituellement dans un système de gestion basé sur des objectifs ou des résultats.
Lors d'une conversation avec le directeur qualité d'une grande entreprise russe, il m'a dit :
- Pour calculer les salaires, nous n'utilisons pas tous les KPI dont nous disposons.
"Il est clair que vos collaborateurs sont prêts à sacrifier d'autres KPI pour atteindre ceux pour lesquels les salaires sont calculés", répondis-je.
"Que pouvez-vous faire, c'est la Russie", s'est plaint mon interlocuteur.
- Trop général. C'est la direction de votre entreprise qui crée ces règles du jeu, et les travailleurs sont obligés de s'adapter s'ils veulent nourrir leur famille. Le pays n’a pas d’importance », ai-je expliqué, comme dans le vide.
« Les limites de la « gestion par objectifs » sont ancrées dans des normes numériques. La « gestion par objectifs » accorde peu, voire aucune attention, aux processus et aux systèmes de l'organisation, aux capacités potentielles de l'organisation dans son ensemble. ces normes, standards, tâches s'avèrent n'être rien d'autre que des nombres arbitraires.
En conséquence de cette approche, les ouvriers, les contremaîtres et les gestionnaires se retrouvent à participer à des « jeux » : le besoin de bien paraître l'emporte sur le souci des intérêts à long terme de l'organisation. Très souvent, les gens perdent la perspective, le but de ce qu'ils font sur leur lieu de travail. »
Si vous en avez assez des indicateurs et des évaluations KPI, il est préférable de créer des cartes de contrôle Shewhart basées sur eux et de les analyser. À l'aide de cartes de contrôle, découvrez à quel niveau des changements sont nécessaires dans les processus qui génèrent vos indicateurs, c'est-à-dire s'il est nécessaire d'éliminer des causes particulières ou d'apporter des changements systémiques.
Développez des actions spécifiques, passez à l'action, vérifiez leur efficacité à l'aide d'une carte de contrôle, confirmez vos hypothèses sur les méthodes d'amélioration retenues, et si nécessaire, ajustez-les ou abandonnez-les pour développer de nouvelles méthodes. Voici le cycle PDSA Shewhart-Deming pour vous aider.
Cette approche d’amélioration sera plus scientifique que toute autre, rendra les efforts de changement véritablement systémiques et mesurables, et contribuera à acquérir une réelle connaissance de vos processus.
Et les cartes de contrôle Shewhart vous permettront de suivre les résultats des changements à la fois rapidement et à long terme.
Beaucoup de choses ont été écrites sur l’interprétation des cartes de contrôle Shewhart sur notre site Web.
Vidéo 1. Cycle Shewhart-Deming PDSA (Plan-Do-Study-Act, Deming Cycle), qui sous-tend la principale norme dans le domaine de la gestion de la qualité ISO 9001, ainsi qu'un certain nombre de normes industrielles : IATF 16949 (industrie automobile) , ISO TS 22163 (IRIS - industrie ferroviaire), EN/AS 9100 (aviation), GOST RV 15.002 (industrie de la défense), STO GAZPROM 9001, etc. Souvent appelé PDCA (Plan-Do-Check-Act).
"Lorsque j'ai découvert pour la première fois le concept du cycle PDSA, en 15 minutes, j'ai pensé que je savais tout ce qu'il y avait à savoir sur ce modèle. Aujourd'hui, après des décennies de pratique active et d'études, je pense qu'un jour j'en saurai assez sur ce modèle. concept ".
Il existe déjà des exemples documentés de « réduction » du nombre de reprises grâce à la méthode n°4 de cet article : Vous pouvez élargir les limites de tolérance des exigences techniques ou donner des définitions vagues des défauts.
"Au broyeur 5000, nous avons reçu un effet positif de l'utilisation de brames d'un groupe de qualité inférieure. Il a été prouvé (qui en douterait - note de Sergey P. Grigoryev) qu'une diminution de la qualité de la billette est acceptable et n'a pas d'impact sérieux sur la qualité des produits de l'étape de transformation suivante. Le produit fini répond à toutes les exigences des normes.